Brazing is a high-temperature joining process that typically involves heating materials above 450°C (842°F) but below the melting point of the base metals. The temperature range a brazed joint can withstand depends on the filler material used, the base metals being joined, and the specific application. While the provided reference mentions a temperature range of -40°C to +260°C, this likely refers to the operational or environmental temperature range of a specific product rather than the brazing process itself. Brazed joints, when properly executed, can often withstand much higher temperatures, depending on the filler metal and base materials.
Key Points Explained:
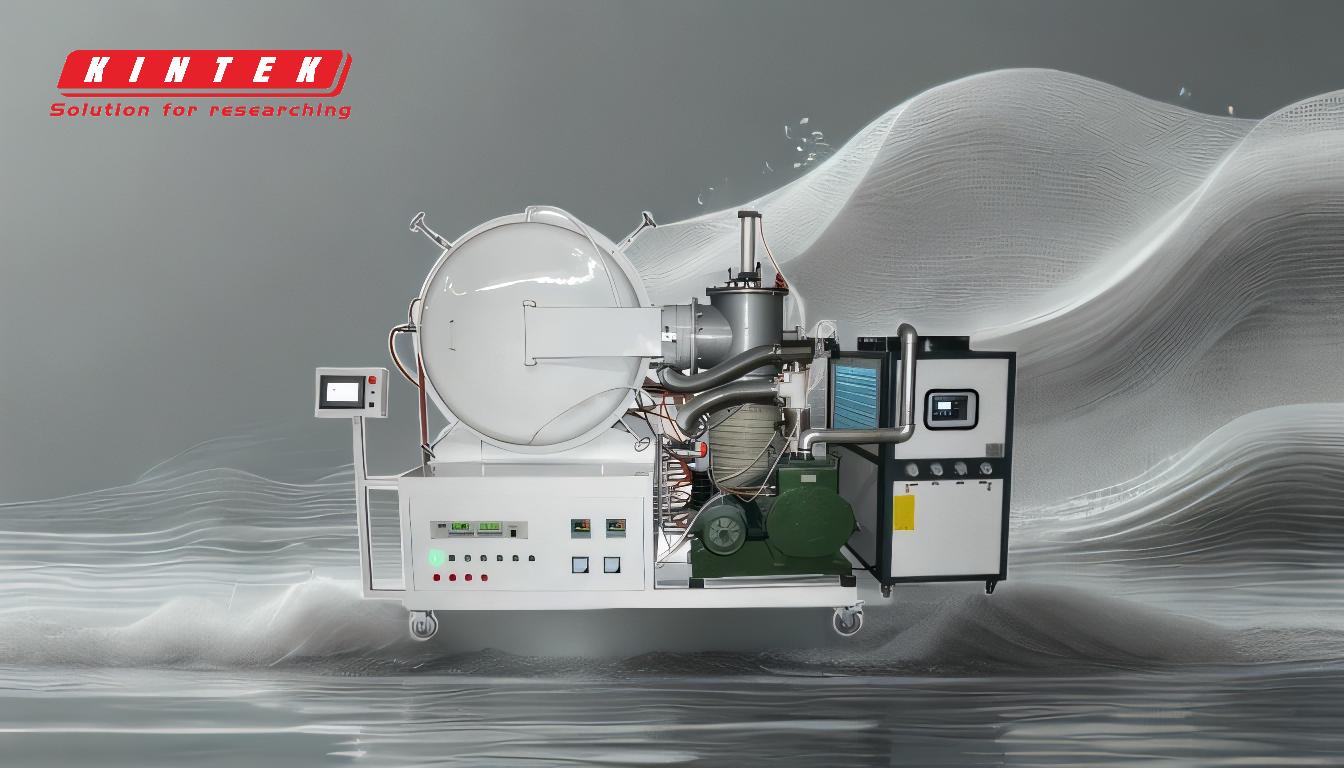
-
Brazing Temperature Range:
- Brazing typically occurs at temperatures above 450°C (842°F) but below the melting point of the base metals. This ensures that the filler metal melts and flows into the joint without melting the base materials.
- The exact temperature depends on the filler metal used. Common filler metals include silver-based alloys, copper-based alloys, and nickel-based alloys, each with different melting points.
-
Temperature Resistance of Brazed Joints:
- Brazed joints are designed to withstand high temperatures, often exceeding the operational range of the base materials. For example:
- Silver-based brazing alloys can withstand temperatures up to 600°C (1112°F).
- Copper-based brazing alloys can handle temperatures up to 800°C (1472°F).
- Nickel-based brazing alloys are suitable for even higher temperatures, up to 1200°C (2192°F), making them ideal for extreme environments like aerospace or industrial furnaces.
- Brazed joints are designed to withstand high temperatures, often exceeding the operational range of the base materials. For example:
-
Operational vs. Brazing Temperature:
- The reference mentions a temperature range of -40°C to +260°C, which likely refers to the operational or environmental temperature range of a specific product. This is not the same as the temperature range for brazing or the temperature resistance of the brazed joint.
- Brazed joints can often withstand higher temperatures than the operational range of the product, provided the filler metal and base materials are chosen appropriately.
-
Factors Affecting Temperature Resistance:
- Filler Metal Selection: The choice of filler metal is critical. High-temperature applications require filler metals with higher melting points and better thermal stability.
- Base Materials: The thermal properties of the base materials (e.g., thermal expansion, melting point) influence the joint's performance at high temperatures.
- Joint Design: Proper joint design ensures even heat distribution and minimizes stress concentrations, enhancing the joint's ability to withstand high temperatures.
-
Applications of High-Temperature Brazing:
- Brazing is widely used in industries requiring high-temperature resistance, such as:
- Aerospace (e.g., turbine components)
- Automotive (e.g., exhaust systems)
- Power generation (e.g., heat exchangers)
- Industrial furnaces (e.g., muffle furnaces)
- In these applications, brazed joints must maintain structural integrity under extreme thermal conditions.
- Brazing is widely used in industries requiring high-temperature resistance, such as:
-
Limitations of Brazing Temperature Resistance:
- While brazed joints can withstand high temperatures, they are not immune to degradation over time. Factors like oxidation, thermal cycling, and mechanical stress can reduce the joint's performance at elevated temperatures.
- Proper post-brazing treatments, such as heat treatment or protective coatings, can enhance the joint's durability.
In summary, while the reference mentions a temperature range of -40°C to +260°C, this is likely specific to a product's operational range. Brazed joints, when designed and executed correctly, can withstand much higher temperatures, depending on the filler metal and base materials used. For high-temperature applications, selecting the appropriate filler metal and optimizing joint design are critical to ensuring long-term performance.
Summary Table:
Aspect | Details |
---|---|
Brazing Temperature Range | Above 450°C (842°F), below base metal melting point |
Filler Metal Resistance | Silver-based: up to 600°C, Copper-based: up to 800°C, Nickel-based: up to 1200°C |
Operational vs. Brazing Temp | Operational range (e.g., -40°C to +260°C) ≠ brazing temperature resistance |
Key Factors | Filler metal, base materials, joint design |
Applications | Aerospace, automotive, power generation, industrial furnaces |
Limitations | Degradation due to oxidation, thermal cycling, mechanical stress |
Need help selecting the right brazing solution for high-temperature applications? Contact our experts today!