A sealed quench furnace is a specialized type of heat treatment furnace used for processes such as hardening, tempering, and annealing. It operates at high temperatures, typically ranging from 800°C to 950°C (1472°F to 1742°F), depending on the specific application and material being treated. The furnace is designed to maintain a controlled atmosphere, often using inert gases like nitrogen or endothermic gas, to prevent oxidation and ensure consistent results. The quenching process, which involves rapidly cooling the heated material, is performed in a separate chamber or within the same sealed environment to achieve the desired material properties.
Key Points Explained:
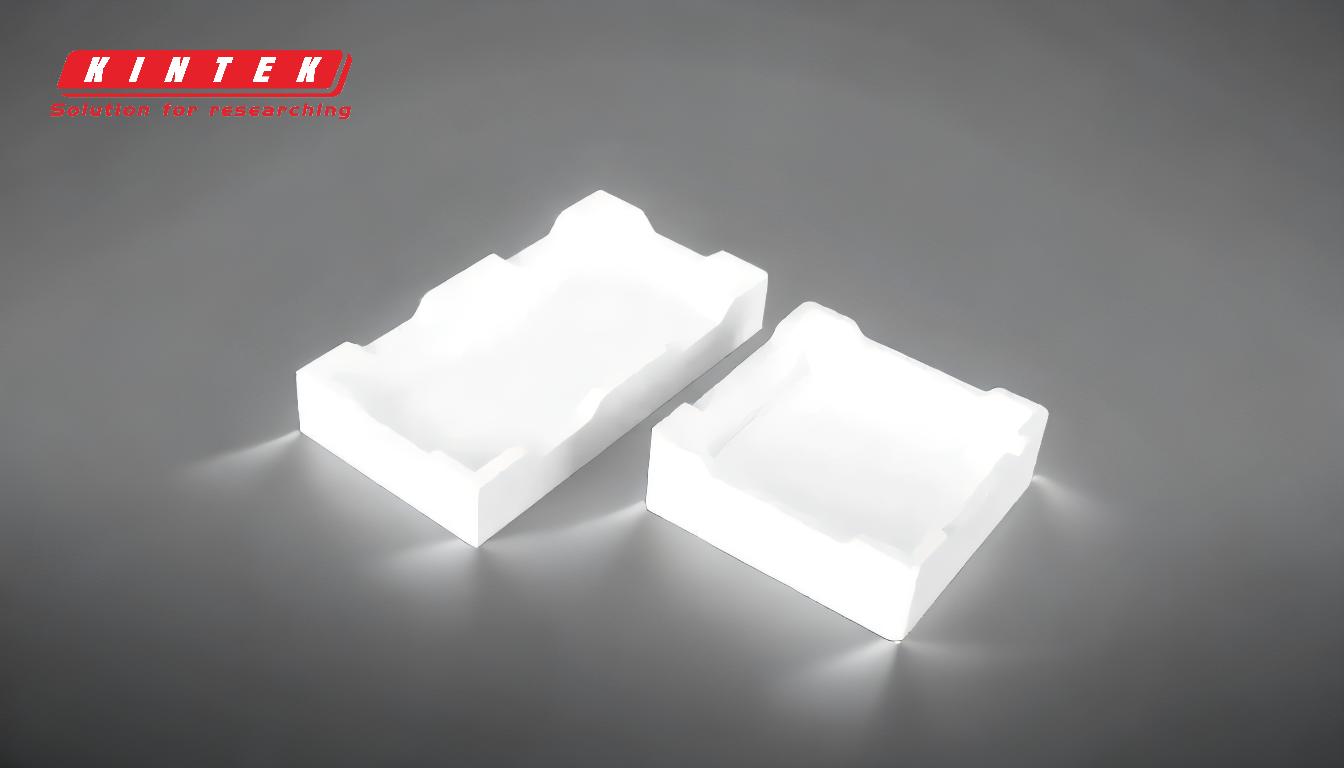
-
Temperature Range of a Sealed Quench Furnace:
- Sealed quench furnaces typically operate at temperatures between 800°C and 950°C (1472°F to 1742°F). This range is ideal for heat treatment processes like hardening, where the material needs to be heated to a critical temperature to alter its microstructure.
- The exact temperature depends on the material being treated. For example, steel alloys may require temperatures closer to the higher end of the range, while other materials might need lower temperatures.
-
Purpose of the Sealed Environment:
- The furnace is sealed to maintain a controlled atmosphere, which is crucial for preventing oxidation and decarburization of the material. This ensures the surface quality and mechanical properties of the treated parts remain intact.
- Common gases used in the sealed environment include nitrogen, hydrogen, or endothermic gas, depending on the material and process requirements.
-
Quenching Process:
- After heating, the material is rapidly cooled (quenched) to achieve the desired hardness and strength. This is done in a separate quenching chamber or within the same sealed environment to maintain consistency and prevent contamination.
- Quenching media can include oil, water, or polymer solutions, depending on the material and desired outcome.
-
Applications of Sealed Quench Furnaces:
- These furnaces are widely used in industries such as automotive, aerospace, and tool manufacturing for processes like case hardening, tempering, and annealing.
- The ability to control both the heating and cooling phases makes sealed quench furnaces highly versatile for producing components with precise mechanical properties.
-
Advantages of Sealed Quench Furnaces:
- Consistency: The sealed environment ensures uniform heating and cooling, leading to consistent results.
- Efficiency: The integrated quenching system reduces the need for additional equipment and handling, saving time and energy.
- Quality: The controlled atmosphere minimizes surface defects, improving the overall quality of the treated parts.
By understanding the temperature range and operational principles of a sealed quench furnace, manufacturers can select the appropriate settings and processes to achieve optimal results for their specific applications.
Summary Table:
Key Information | Details |
---|---|
Temperature Range | 800°C to 950°C (1472°F to 1742°F) |
Purpose of Sealed Environment | Prevents oxidation and decarburization, ensuring consistent results |
Quenching Process | Rapid cooling in a separate chamber or sealed environment |
Applications | Automotive, aerospace, tool manufacturing (hardening, tempering, annealing) |
Advantages | Consistency, efficiency, and high-quality results |
Optimize your heat treatment process with a sealed quench furnace—contact our experts today!