Glass sintering is a thermal process that involves heating glass powder to a temperature below its melting point, allowing the particles to bond together without fully liquefying. This process is critical in manufacturing glass products with specific shapes and properties. The temperature required for glass sintering typically ranges between 600°C and 900°C, depending on the type of glass and the desired properties of the final product. The process relies on high temperatures to enable diffusion mechanisms that reduce surface area and curvature, leading to effective consolidation of the glass powder.
Key Points Explained:
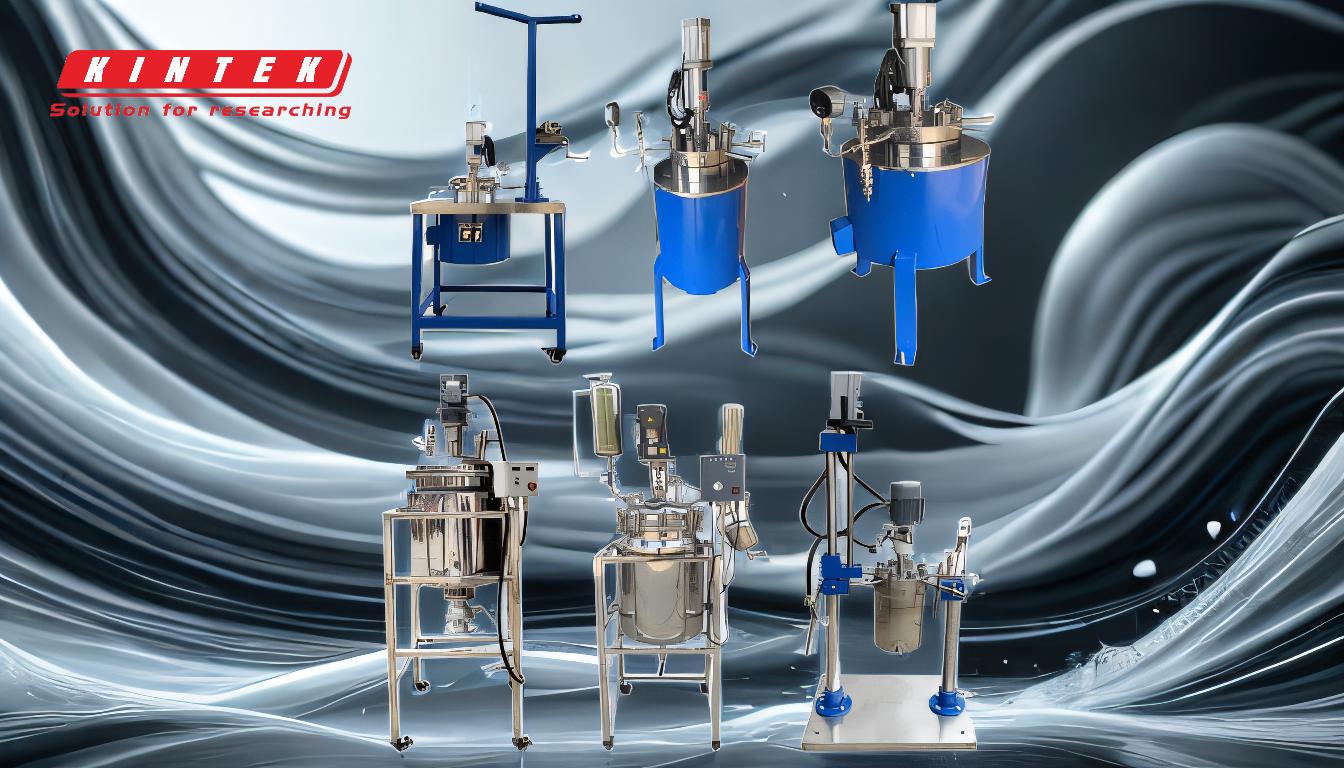
-
Definition of Glass Sintering:
- Glass sintering is a process where glass particles are heated to a temperature below their melting point, causing them to bond together through diffusion mechanisms. This results in a dense, solid structure without the glass reaching a fully liquid state.
-
Temperature Range for Glass Sintering:
- The sintering temperature for glass typically falls between 600°C and 900°C. This range is chosen because it is high enough to facilitate particle bonding but low enough to prevent complete melting, which could alter the desired shape and properties of the final product.
-
Influence of Material Properties:
- The exact sintering temperature depends on the type of glass being used. Different glass compositions have varying melting points and thermal behaviors, which influence the optimal sintering temperature. For example, soda-lime glass may sinter at a lower temperature compared to borosilicate glass due to differences in their thermal properties.
-
Role of High Temperatures in Sintering:
- High temperatures are essential for sintering because they enable the diffusion processes that reduce surface area and local curvature of the glass particles. These processes help in consolidating the powder into a dense, cohesive structure.
-
Importance of Temperature Control:
- Precise temperature control is crucial during the sintering process. If the temperature is too low, the particles may not bond effectively, leading to a weak or porous structure. If the temperature is too high, the glass may melt completely, losing its intended shape and properties.
-
Applications of Glass Sintering:
- Glass sintering is used in various applications, including the production of glass ceramics, optical components, and specialty glass products. The process allows for the creation of complex shapes and tailored properties, making it valuable in industries such as electronics, optics, and construction.
-
Comparison with Other Sintering Processes:
- While glass sintering shares similarities with sintering processes for other materials, such as metals and ceramics, it is unique in its reliance on the glass transition temperature and the avoidance of complete melting. This distinction makes glass sintering a specialized process with specific temperature and control requirements.
By understanding these key points, equipment and consumable purchasers can make informed decisions about the materials and processes needed for glass sintering, ensuring optimal results in their manufacturing applications.
Summary Table:
Key Aspect | Details |
---|---|
Temperature Range | 600°C to 900°C |
Purpose | Bond glass particles without full melting |
Material Influence | Varies by glass type (e.g., soda-lime vs. borosilicate) |
Critical Factors | Precise temperature control, diffusion mechanisms |
Applications | Glass ceramics, optical components, specialty glass products |
Need help optimizing your glass sintering process? Contact our experts today for tailored solutions!