PVD (Physical Vapor Deposition) application temperatures typically range between 200°C to 450°C (392°F to 842°F), depending on the substrate material and specific process requirements. This temperature range is significantly lower than that of CVD (Chemical Vapor Deposition), which operates at 600°C to 1100°C. PVD's lower temperatures make it suitable for heat-sensitive materials, such as aluminum and certain plastics, without causing significant thermal distortion or altering the substrate's properties. The process can be adjusted to operate at even lower temperatures (50°F to 400°F) for specific substrates like zinc, brass, or plastics, ensuring minimal thermal impact.
Key Points Explained:
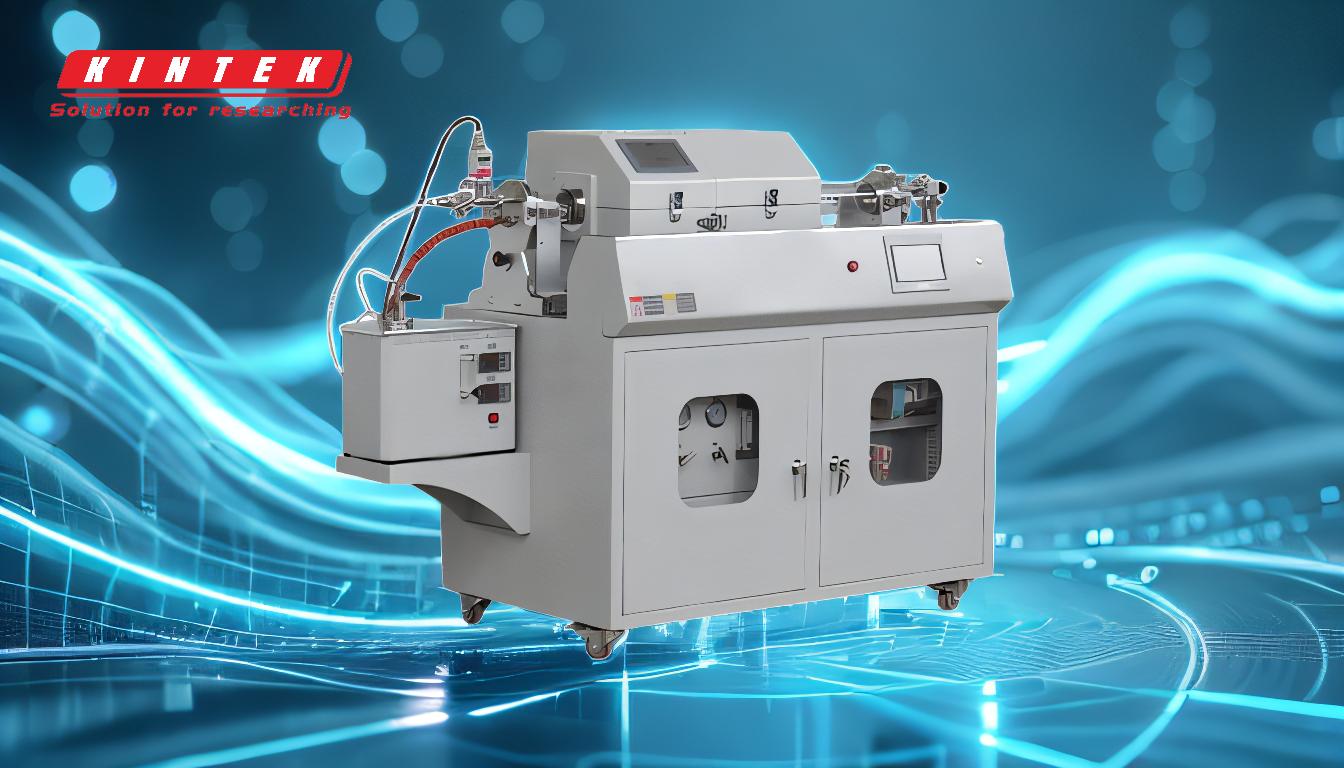
-
Typical PVD Temperature Range:
- PVD coatings are applied at temperatures between 200°C to 450°C (392°F to 842°F). This range is considerably lower than CVD, which operates at 600°C to 1100°C.
- The lower temperature range is critical for maintaining the integrity of heat-sensitive materials, such as aluminum, which has a melting point close to 800°F.
-
Substrate-Specific Temperature Control:
- For substrates like zinc, brass, steel, or plastics, the process temperature can be finely controlled from 50°F to 400°F. This flexibility ensures that the thermal impact on the substrate is minimized, preserving its mechanical and structural properties.
-
Comparison with CVD:
- CVD requires much higher temperatures (600°C to 1100°C) to facilitate chemical reactions between the gas and the substrate. These high temperatures can cause thermal effects, such as phase changes in steel (e.g., austenite formation), which may necessitate post-coating heat treatments.
- In contrast, PVD uses plasma to vaporize the solid material, eliminating the need for high temperatures and reducing the risk of substrate distortion or property alteration.
-
Advantages of Lower PVD Temperatures:
- Minimized Thermal Distortion: The lower temperatures in PVD prevent warping or distortion of heat-sensitive parts, such as precision-engineered components or thin-walled structures.
- Material Compatibility: PVD can be used on a wider range of materials, including those with low melting points or poor thermal stability, such as plastics and certain alloys.
- No Need for Post-Coating Heat Treatment: Unlike CVD, PVD does not typically require additional heat treatment to restore substrate properties, simplifying the coating process.
-
Process Flexibility:
- The ability to adjust PVD temperatures based on substrate requirements makes it a versatile coating method. For example:
- Aluminum: Coated at temperatures below 800°F to avoid melting.
- Plastics: Coated at temperatures as low as 50°F to prevent deformation.
- Steel and Brass: Coated within the 200°C to 450°C range to ensure adhesion without compromising hardness or strength.
- The ability to adjust PVD temperatures based on substrate requirements makes it a versatile coating method. For example:
-
Applications of PVD:
- PVD is widely used in industries where maintaining substrate integrity is critical, such as:
- Aerospace: Coating lightweight, heat-sensitive components.
- Medical Devices: Coating implants and surgical tools without altering biocompatibility.
- Electronics: Coating semiconductors and connectors with minimal thermal impact.
- PVD is widely used in industries where maintaining substrate integrity is critical, such as:
By operating at lower temperatures, PVD provides a reliable and efficient coating solution for a broad spectrum of materials and applications, ensuring high-quality results without compromising substrate properties.
Summary Table:
Aspect | Details |
---|---|
Typical PVD Temperature Range | 200°C to 450°C (392°F to 842°F) |
Substrate-Specific Control | Adjustable from 50°F to 400°F for zinc, brass, steel, or plastics |
Comparison with CVD | CVD operates at 600°C to 1100°C, requiring higher temperatures |
Advantages of PVD | Minimized thermal distortion, material compatibility, no post-coating heat treatment |
Applications | Aerospace, medical devices, electronics |
Learn how PVD can enhance your coating process—contact our experts today for tailored solutions!