Injection molding is a versatile manufacturing process used to produce a wide range of plastic products. It involves injecting molten material into a press mold to create parts with high precision and repeatability. This method is ideal for mass production due to its efficiency, scalability, and ability to produce complex shapes with minimal waste. Common applications include automotive components, consumer goods, packaging, and medical devices. To effectively utilize injection molding, one must understand the process, select appropriate materials, design molds, and optimize production parameters. Below is a detailed breakdown of the key aspects of injection molding.
Key Points Explained:
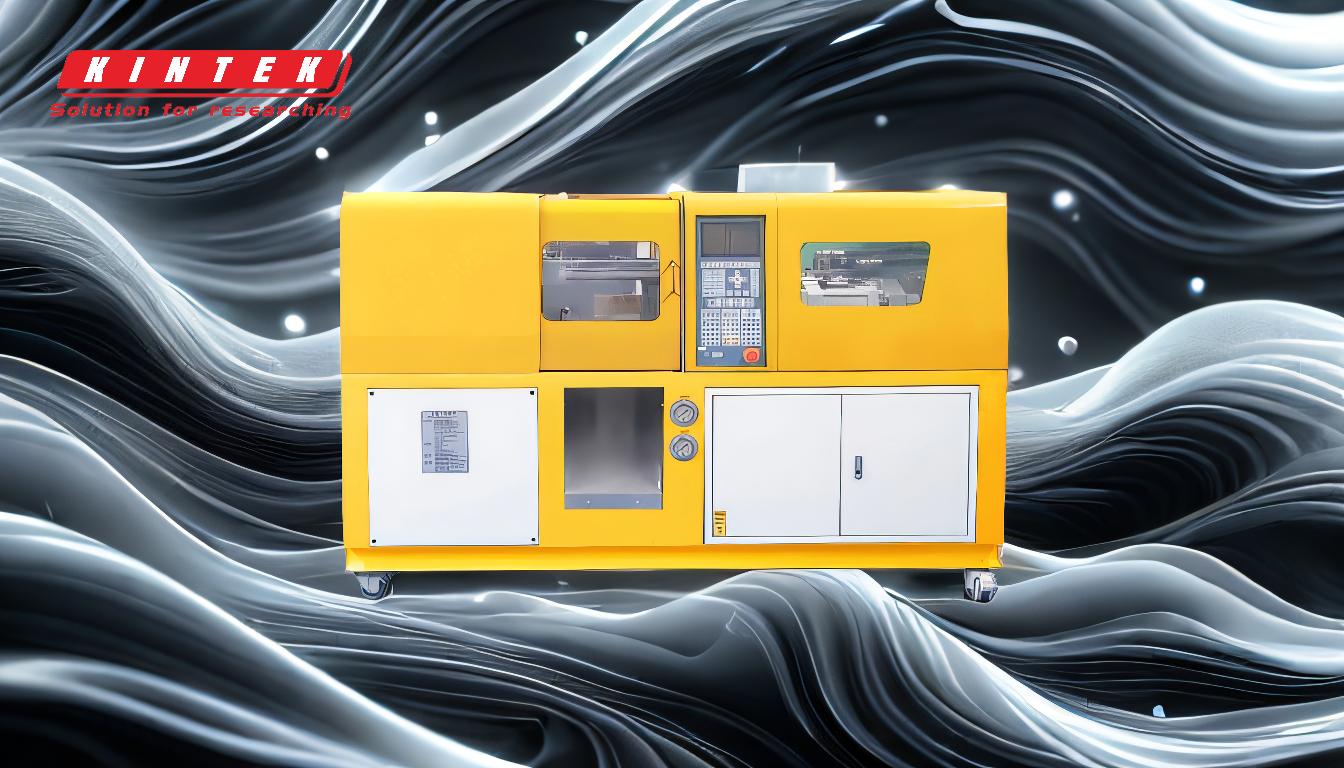
-
Understanding the Injection Molding Process:
- Injection molding involves heating plastic pellets until they melt, then injecting the molten material into a mold cavity under high pressure.
- The material cools and solidifies, taking the shape of the mold, after which the part is ejected.
- This process is highly automated, making it suitable for high-volume production.
-
Applications of Injection Molding:
- Automotive Parts: Components like dashboards, bumpers, and interior trim are commonly made using injection molding due to their durability and precision.
- Consumer Goods: Items such as toys, bottle caps, and storage containers are mass-produced using this method.
- Medical Devices: Syringes, IV components, and surgical tools benefit from the sterility and precision of injection molding.
- Packaging: Thin-walled containers, caps, and closures are efficiently produced using this process.
-
Material Selection:
- Thermoplastics: Commonly used materials include polyethylene (PE), polypropylene (PP), polystyrene (PS), and acrylonitrile butadiene styrene (ABS). These materials are chosen for their versatility, strength, and cost-effectiveness.
- Engineering Plastics: For high-performance applications, materials like polycarbonate (PC) and nylon are used due to their heat resistance and mechanical properties.
- Additives: Fillers, colorants, and reinforcements can be added to enhance material properties such as strength, flexibility, or appearance.
-
Mold Design and Manufacturing:
- Mold Design: The mold must be precisely designed to match the desired part geometry. Factors like gate location, cooling channels, and ejection mechanisms are critical.
- Mold Materials: Molds are typically made from steel or aluminum, depending on the production volume and part complexity.
- Tooling Costs: Initial mold design and manufacturing can be expensive, but the cost is offset by the high production volumes and low per-unit costs.
-
Production Optimization:
- Cycle Time: Reducing cycle time is essential for efficiency. This involves optimizing cooling time, injection speed, and mold design.
- Quality Control: Ensuring consistent part quality requires monitoring parameters like temperature, pressure, and material flow.
- Automation: Incorporating robotics and automated systems can further enhance production speed and consistency.
-
Advantages of Injection Molding:
- High Efficiency: The process is fast and scalable, making it ideal for large-scale production.
- Complex Geometries: Injection molding can produce intricate shapes with high precision.
- Material Versatility: A wide range of materials can be used, allowing for customization of part properties.
- Low Waste: Excess material can often be recycled, reducing waste.
-
Challenges and Considerations:
- High Initial Costs: The cost of mold design and manufacturing can be prohibitive for small production runs.
- Design Limitations: Parts must be designed with moldability in mind, which can restrict certain geometries.
- Material Limitations: Not all materials are suitable for injection molding, and some may require specialized equipment.
-
Future Trends in Injection Molding:
- Sustainable Materials: Increasing use of biodegradable and recycled materials to reduce environmental impact.
- Advanced Technologies: Integration of IoT and AI for real-time monitoring and process optimization.
- Micro-Molding: Development of techniques to produce extremely small and precise parts for medical and electronic applications.
By understanding these key points, one can effectively leverage injection molding for a wide range of applications, from consumer goods to industrial components. The process offers numerous advantages, but careful planning and optimization are essential to overcome its challenges and maximize its potential.
Summary Table:
Aspect | Key Details |
---|---|
Process | Heats plastic pellets, injects molten material into a mold, and ejects the part. |
Applications | Automotive parts, consumer goods, medical devices, and packaging. |
Materials | Thermoplastics (PE, PP, PS, ABS) and engineering plastics (PC, nylon). |
Mold Design | Precise geometry, gate location, cooling channels, and ejection mechanisms. |
Advantages | High efficiency, complex geometries, material versatility, and low waste. |
Challenges | High initial costs, design limitations, and material restrictions. |
Future Trends | Sustainable materials, IoT/AI integration, and micro-molding. |
Ready to optimize your production with injection molding? Contact us today for expert guidance!