Casting is a manufacturing process where molten material is poured into a mold to create a desired shape. The tools used for casting vary depending on the type of casting process (e.g., sand casting, investment casting, die casting) and the materials being used. Common tools include hand tools like rammers, riddles, vent cables, and mallets, as well as equipment like bench presses and clamps. These tools help in preparing molds, ensuring proper compaction, and facilitating the casting process. Below is a detailed explanation of the key tools and their roles in casting.
Key Points Explained:
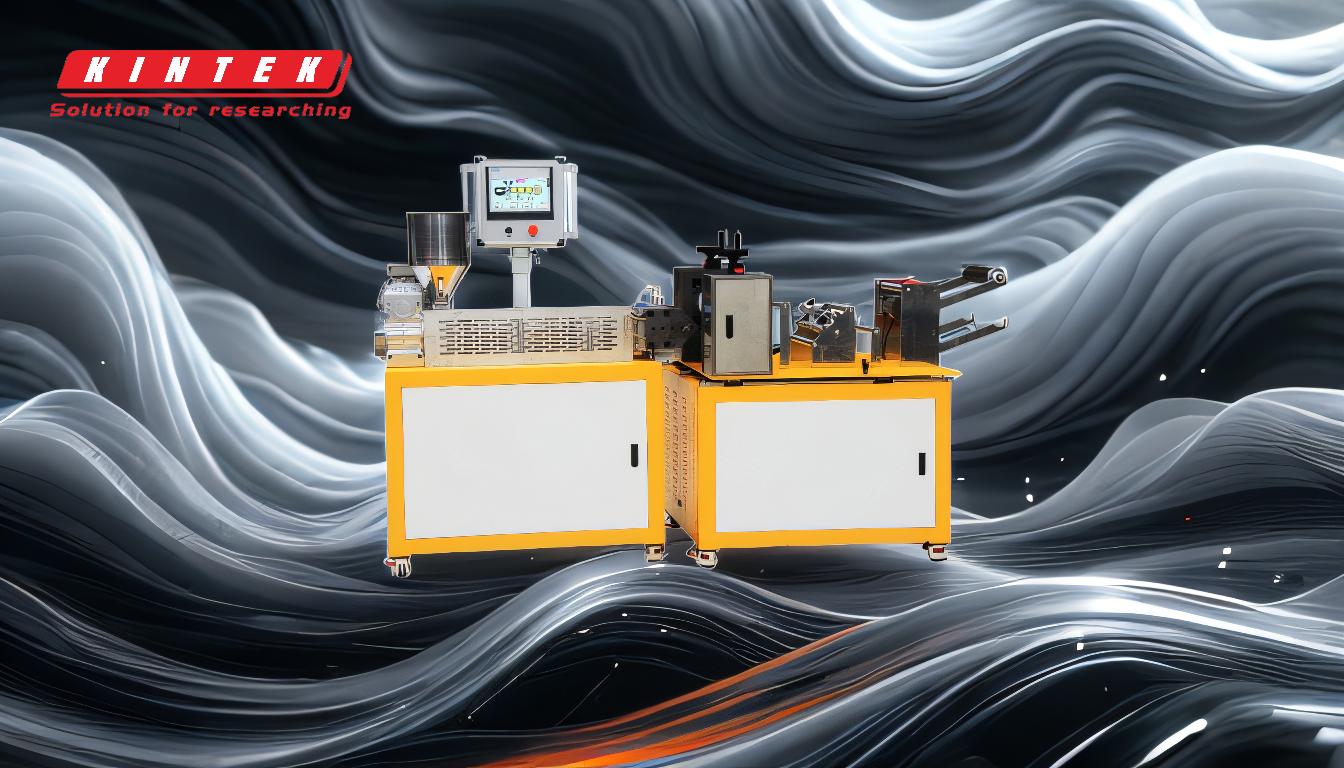
-
Rammer
- A rammer is used to compact the sand or other molding material in the mold. Proper compaction ensures that the mold retains its shape and can withstand the pressure of the molten material.
- Types of rammers include hand rammers (for small-scale work) and pneumatic rammers (for larger, industrial applications).
-
Riddle
- A riddle is a sieve-like tool used to sift sand or powder to remove lumps and ensure a fine, even consistency. This is crucial for creating a smooth surface in the mold.
- Riddles are often used in sand casting to prepare the molding sand before it is packed into the mold.
-
Vent Cables
- Vent cables are thin, flexible rods used to create channels in the mold for gases to escape during the casting process. Proper venting prevents defects like gas porosity in the final cast product.
- These are especially important in sand casting, where trapped gases can compromise the quality of the cast.
-
Bench Press
- A bench press is used to apply pressure to molds or to hold components in place during the casting process. It ensures stability and precision, especially in investment casting or when working with intricate molds.
-
Investment Powder
- Investment powder is a fine ceramic material used in investment casting to create the mold. It is mixed with a binder to form a slurry, which is then poured around a wax or plastic pattern.
- Once the slurry hardens, the pattern is melted or burned out, leaving a cavity for the molten material.
-
Mallet
- A mallet is a hammer-like tool used to gently tap or adjust molds and patterns. It is particularly useful for delicate work where precision is required.
- Mallets are often made of wood or rubber to avoid damaging the mold or pattern.
-
Clamps
- Clamps are used to hold molds or patterns securely in place during the casting process. They ensure that the mold does not shift or open during pouring, which could lead to defects.
- Clamps are essential in processes like die casting and sand casting.
-
Gagger
- A gagger is a tool used to reinforce the mold, especially in sand casting. It helps support the mold walls and prevents them from collapsing under the weight of the molten material.
- Gaggers are typically made of metal and are inserted into the mold during the preparation stage.
-
Bellow
- A bellow is used to blow away loose sand or debris from the mold cavity before pouring the molten material. This ensures a clean surface and reduces the risk of defects.
- Bellows are particularly useful in sand casting for cleaning intricate mold details.
These tools are essential for ensuring the quality and precision of the casting process. Each tool plays a specific role, from preparing the mold to facilitating the pouring and solidification of the molten material. Understanding their functions helps in selecting the right tools for different casting applications.
Summary Table:
Tool | Purpose | Common Applications |
---|---|---|
Rammer | Compacts sand or molding material to retain mold shape | Sand casting, industrial use |
Riddle | Sifts sand to remove lumps and ensure fine consistency | Sand casting |
Vent Cables | Creates channels for gas escape, preventing defects | Sand casting |
Bench Press | Applies pressure to molds for stability and precision | Investment casting |
Investment Powder | Forms ceramic molds for investment casting | Investment casting |
Mallet | Adjusts molds and patterns with precision | Delicate casting work |
Clamps | Secures molds to prevent shifting during pouring | Die casting, sand casting |
Gagger | Reinforces mold walls to prevent collapse | Sand casting |
Bellow | Cleans mold cavities by blowing away loose sand or debris | Sand casting |
Need the right tools for your casting project? Contact our experts today for personalized guidance!