Melting aluminum requires furnaces that can efficiently handle its relatively low melting point (around 660°C or 1220°F) while maintaining precise temperature control and minimizing oxidation. The most commonly used furnaces for melting aluminum are induction furnaces, crucible furnaces, and, to a lesser extent, electric arc furnaces. Induction furnaces are particularly popular due to their energy efficiency, precise temperature control, and clean operation. Crucible furnaces are ideal for smaller-scale operations or specialized applications, while electric arc furnaces are less common for aluminum due to their higher operating temperatures and potential for oxidation. Below, we explore the key types of furnaces used for melting aluminum and their specific advantages.
Key Points Explained:
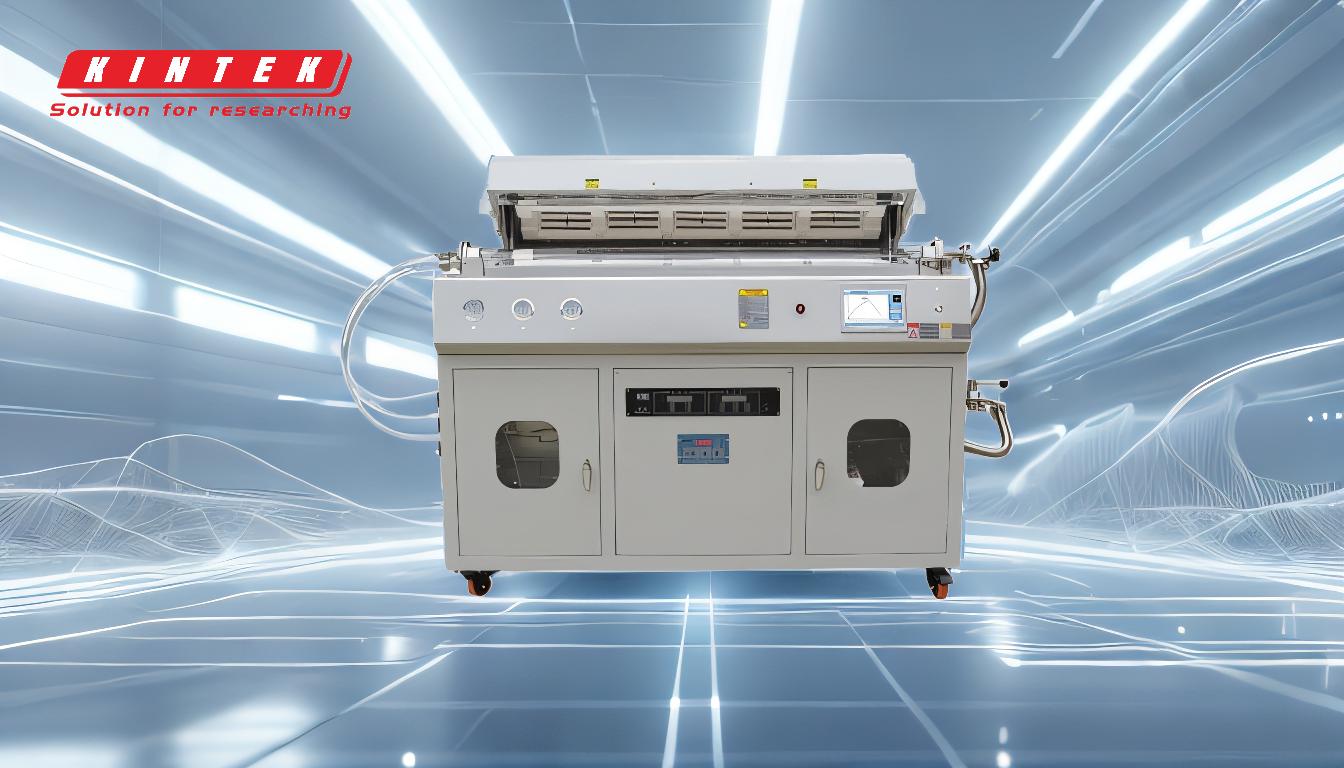
-
Induction Furnaces
- Induction furnaces are the most widely used type for melting aluminum due to their efficiency and precision.
- They use electromagnetic induction to generate heat directly within the metal, ensuring uniform heating and minimizing energy loss.
- These furnaces are divided into two main types:
- Main Frequency Induction Furnaces: Suitable for large-scale operations, offering high power and consistent performance.
- Medium Frequency Induction Furnaces: Ideal for smaller-scale or batch operations, providing faster melting times and better temperature control.
- Induction furnaces are preferred for aluminum melting because they reduce oxidation and contamination, which is critical for maintaining the quality of the molten metal.
-
Crucible Furnaces
- Crucible furnaces are another popular choice, especially for small to medium-scale aluminum melting.
- These furnaces use a refractory-lined crucible to hold the aluminum, which is heated by an external heat source such as gas, oil, or electricity.
- Crucible furnaces are versatile and cost-effective, making them suitable for foundries, laboratories, and artisanal applications.
- They are particularly useful for melting small batches or specific alloys, as they allow for precise control over the melting process.
-
Electric Arc Furnaces
- Electric arc furnaces are less commonly used for aluminum melting compared to induction and crucible furnaces.
- They generate heat using an electric arc between electrodes, which can reach extremely high temperatures.
- While effective for melting metals with higher melting points, such as steel, electric arc furnaces are less ideal for aluminum due to the risk of oxidation and the need for careful temperature control.
- However, they may be used in specialized applications where high throughput is required.
-
Advantages of Induction and Crucible Furnaces for Aluminum
- Energy Efficiency: Both induction and crucible furnaces are highly energy-efficient, reducing operational costs.
- Oxidation Control: Induction furnaces, in particular, minimize oxidation by melting the metal in a controlled environment.
- Precision: These furnaces allow for precise temperature control, which is essential for maintaining the quality of aluminum alloys.
- Scalability: Induction furnaces can be scaled for large industrial operations, while crucible furnaces are ideal for smaller, specialized applications.
-
Considerations for Choosing a Furnace
- Scale of Operation: Induction furnaces are better suited for large-scale production, while crucible furnaces are ideal for smaller batches.
- Energy Source: Induction furnaces rely on electricity, whereas crucible furnaces can use gas, oil, or electricity, offering flexibility in energy sourcing.
- Cost: Crucible furnaces are generally more affordable for small-scale operations, while induction furnaces require a higher initial investment but offer long-term savings through energy efficiency.
- Application: The specific requirements of the aluminum alloy being melted, such as purity and composition, will influence the choice of furnace.
In summary, induction furnaces are the most efficient and widely used option for melting aluminum, offering precise temperature control and minimal oxidation. Crucible furnaces are a cost-effective alternative for smaller-scale operations, while electric arc furnaces are less common due to their higher operating temperatures and potential for oxidation. The choice of furnace ultimately depends on the scale of production, energy source, and specific application requirements.
Summary Table:
Furnace Type | Best For | Key Advantages |
---|---|---|
Induction Furnaces | Large-scale operations | Energy-efficient, precise temperature control, minimal oxidation, clean operation |
Crucible Furnaces | Small to medium-scale operations | Cost-effective, versatile, precise control, suitable for specific alloys |
Electric Arc Furnaces | Specialized high-throughput needs | High temperatures, less ideal for aluminum due to oxidation risks |
Need help choosing the right furnace for melting aluminum? Contact our experts today for personalized advice!