Heat treatment furnaces utilize a variety of gases to achieve specific thermal and chemical conditions required for processing materials. Commonly used gases include hydrogen, nitrogen, oxygen, helium, argon, carbon monoxide, carbon dioxide, ammonia, propane, methane, and butane. Each gas serves a unique purpose, such as creating inert atmospheres, preventing oxidation, or facilitating chemical reactions like carburization. Oxygen, while reactive, is used cautiously due to its potential to cause oxidation and decarburization. The choice of gas depends on the desired outcome, material properties, and safety considerations.
Key Points Explained:
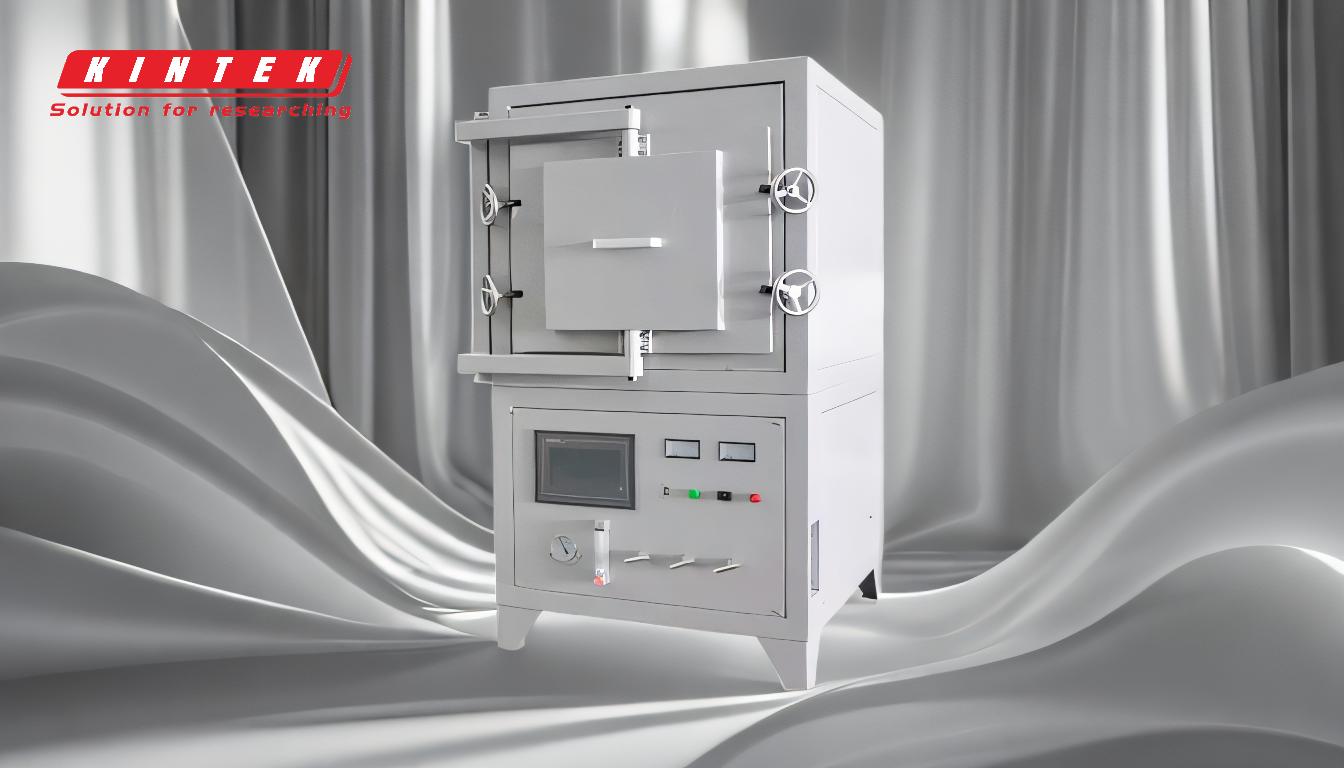
-
Types of Gases Used in Heat Treatment Furnaces:
- Hydrogen (H₂): Often used for its reducing properties, hydrogen helps prevent oxidation and decarburization. It is also used in processes like annealing and sintering.
- Nitrogen (N₂): An inert gas that creates a non-reactive atmosphere, nitrogen is widely used to prevent oxidation and decarburization during heat treatment.
- Oxygen (O₂): While reactive, oxygen is used in controlled amounts for processes like scale removal or surface conditioning. However, excessive oxygen can lead to oxidation and decarburization.
- Helium (He) and Argon (Ar): These inert gases are used to create protective atmospheres, especially in high-temperature applications like sintering and hot isostatic pressing.
- Carbon Monoxide (CO) and Carbon Dioxide (CO₂): These gases are used in carburizing and carbonitriding processes to introduce carbon into the material surface.
- Ammonia (NH₃): Used in nitriding processes to introduce nitrogen into the material surface, enhancing hardness and wear resistance.
- Hydrocarbons (Propane, Methane, Butane, Ethane, Acetylene): These gases are used in carburizing processes to provide a carbon-rich atmosphere for surface hardening.
-
Purpose of Gases in Heat Treatment:
- Inert Atmospheres: Gases like nitrogen, helium, and argon are used to create non-reactive environments, preventing oxidation and decarburization.
- Reducing Atmospheres: Hydrogen is used to reduce oxides on the material surface, ensuring a clean and oxide-free finish.
- Carburizing Atmospheres: Carbon-rich gases like methane, propane, and carbon monoxide are used to increase the carbon content on the material surface, enhancing hardness.
- Nitriding Atmospheres: Ammonia is used to introduce nitrogen into the material surface, improving wear resistance and hardness.
-
Considerations for Gas Selection:
- Material Properties: The choice of gas depends on the material being treated and the desired properties (e.g., hardness, wear resistance).
- Process Requirements: Different heat treatment processes (e.g., annealing, carburizing, nitriding) require specific gas atmospheres to achieve the desired results.
- Safety: Some gases, like hydrogen, are flammable and require special safety measures, such as explosion-proof equipment and proper ventilation.
-
Challenges and Precautions:
- Oxidation and Decarburization: Oxygen and other reactive gases can cause surface degradation if not controlled properly.
- Gas Purity: Impurities in gases can affect the quality of the heat treatment process, so high-purity gases are often required.
- Cost and Availability: Some gases, like helium, are expensive and may not be readily available, influencing their use in industrial applications.
-
Applications of Specific Gases:
- Hydrogen: Used in annealing stainless steel and other alloys to prevent oxidation.
- Nitrogen: Commonly used in brazing and sintering processes to create inert atmospheres.
- Argon: Used in high-temperature processes like hot isostatic pressing to prevent oxidation.
- Carbon Monoxide: Used in carburizing processes to introduce carbon into the material surface.
- Ammonia: Used in nitriding processes to enhance surface hardness and wear resistance.
By understanding the properties and applications of these gases, heat treatment professionals can select the appropriate gas or gas mixture to achieve the desired material properties and ensure the success of the heat treatment process.
Summary Table:
Gas | Purpose | Applications |
---|---|---|
Hydrogen (H₂) | Prevents oxidation, reduces oxides, used in annealing and sintering | Annealing stainless steel, sintering |
Nitrogen (N₂) | Creates inert atmospheres, prevents oxidation and decarburization | Brazing, sintering |
Oxygen (O₂) | Used for scale removal or surface conditioning (controlled amounts) | Surface conditioning, scale removal |
Helium (He) | Creates protective atmospheres in high-temperature processes | Sintering, hot isostatic pressing |
Argon (Ar) | Prevents oxidation in high-temperature processes | Hot isostatic pressing, high-temperature sintering |
Carbon Monoxide (CO) | Introduces carbon for surface hardening (carburizing) | Carburizing, carbonitriding |
Ammonia (NH₃) | Introduces nitrogen for surface hardening (nitriding) | Nitriding processes to enhance hardness and wear resistance |
Hydrocarbons | Provides carbon-rich atmospheres for surface hardening | Carburizing processes (e.g., methane, propane, butane) |
Need help selecting the right gas for your heat treatment process? Contact our experts today for tailored solutions!