Magnetron sputtering is a plasma-based physical vapor deposition (PVD) method widely used for thin film deposition in various industries. It involves the use of a magnetic field to enhance the efficiency of the sputtering process by confining electrons near the target, increasing ionization and sputter rates. This technique is highly versatile, capable of depositing metals, alloys, and compounds with high purity, excellent adhesion, and uniformity. It is particularly valued for its ability to coat heat-sensitive substrates and achieve high deposition rates, making it a preferred method for applications in electrical, optical, and industrial production settings.
Key Points Explained:
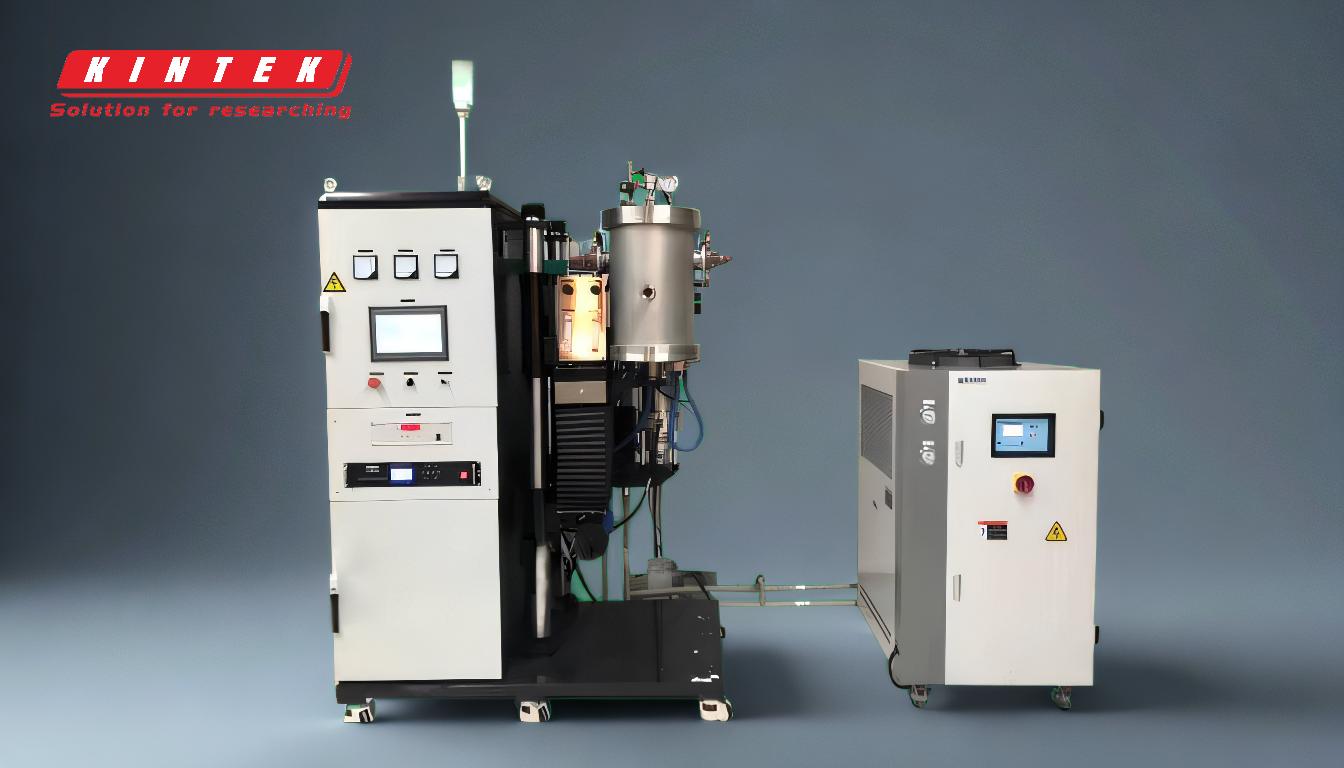
-
Magnetron Sputtering as a Physical Vapor Deposition (PVD) Method:
- Magnetron sputtering is a type of PVD technique where material is ejected from a solid target (cathode) onto a substrate due to bombardment by high-energy ions. This process occurs in a vacuum environment, ensuring high-purity thin films.
- Unlike other PVD methods, magnetron sputtering uses a magnetic field to trap electrons near the target, increasing the ionization of the sputtering gas (typically argon) and enhancing the efficiency of the process.
-
Role of Magnetic and Electric Fields:
- A magnetic field is applied perpendicular to the electric field, causing electrons to spiral along the magnetic field lines. This confinement increases the probability of collisions between electrons and gas atoms, leading to higher ionization rates.
- The target is negatively charged (typically −300 V or more), attracting positively charged ions from the plasma. These ions collide with the target surface, transferring energy and causing atoms to be ejected (sputtered).
-
Sputtering Mechanism:
- When positive ions collide with the target surface, they transfer kinetic energy to the target atoms. If the energy transferred exceeds the binding energy of the target material, atoms are ejected from the surface.
- This process creates a "collision cascade," where ejected atoms (sputtered particles) travel toward the substrate and form a thin film.
-
Advantages of Magnetron Sputtering:
- High Deposition Rates: The magnetic field enhances ionization, leading to faster sputtering and deposition.
- Versatility: Almost any material, including metals, alloys, and compounds, can be used as a sputtering target.
- High-Purity Films: The vacuum environment and precise control over the process result in films with minimal contamination.
- Excellent Adhesion: Sputtered films adhere strongly to the substrate, making them suitable for demanding applications.
- Uniformity and Coverage: The method provides excellent step coverage and uniformity, even on large-area substrates.
- Heat Sensitivity: Magnetron sputtering can deposit films on heat-sensitive substrates without damaging them.
-
Applications of Magnetron Sputtering:
- Electrical and Optical Industries: Used for depositing conductive layers (e.g., ITO for transparent electrodes) and optical coatings.
- Industrial Coatings: Applied for wear-resistant, corrosion-resistant, and decorative coatings.
- Semiconductors: Essential for depositing thin films in semiconductor device fabrication.
- Research and Development: Widely used in laboratories for developing new materials and coatings.
-
Comparison with Other Deposition Methods:
- Unlike evaporation-based PVD methods, magnetron sputtering does not require melting or evaporating the target material. This allows for better control over film composition and properties.
- Sputtered films generally have better adhesion and conformal coverage compared to evaporated films, making them more suitable for complex geometries.
In summary, magnetron sputtering is a highly efficient and versatile thin film deposition method that leverages magnetic and electric fields to enhance the sputtering process. Its ability to deposit high-quality films on a wide range of materials and substrates makes it indispensable in modern manufacturing and research.
Summary Table:
Aspect | Details |
---|---|
Method Type | Plasma-based Physical Vapor Deposition (PVD) |
Key Feature | Uses magnetic fields to enhance sputtering efficiency |
Advantages | High deposition rates, versatility, high-purity films, excellent adhesion |
Applications | Electrical, optical, industrial coatings, semiconductors, R&D |
Comparison with Others | Better adhesion and coverage than evaporation-based PVD methods |
Interested in learning more about magnetron sputtering? Contact us today for expert advice!