Pyrolysis is a thermal decomposition process that occurs in the absence of oxygen, typically at high temperatures ranging from 350°C to 800°C. It involves the breakdown of carbon-rich organic materials, such as biomass, into gaseous products and solid residues. This process is widely used in various industries, including waste management, energy production, and chemical manufacturing, due to its ability to convert organic waste into valuable byproducts like biochar, syngas, and bio-oil. Pyrolysis occurs in specialized equipment designed to maintain an oxygen-free environment and precise temperature control, ensuring efficient decomposition of the feedstock.
Key Points Explained:
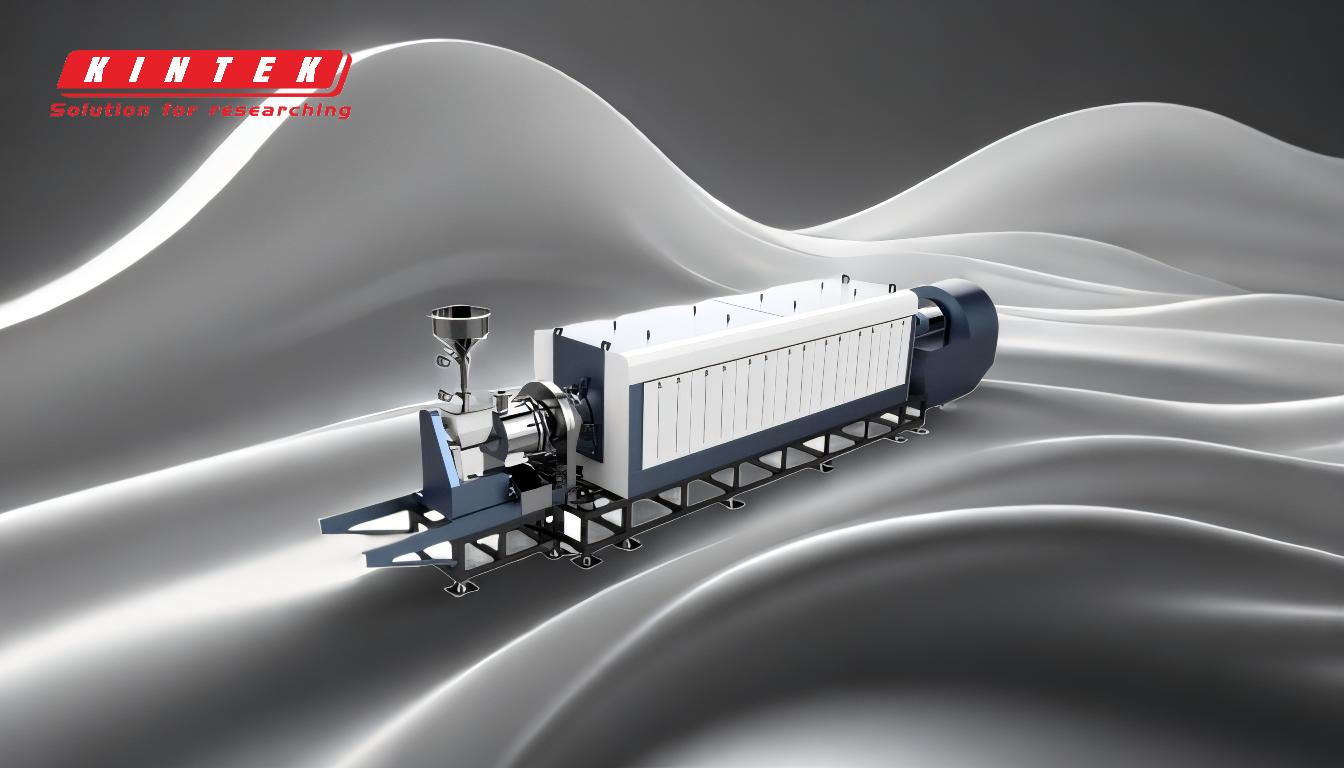
-
Definition of Pyrolysis:
- Pyrolysis is the thermal decomposition of organic materials in the absence of oxygen. It involves breaking down carbon-rich substances into smaller molecules, resulting in gaseous products, liquid bio-oil, and solid residues like biochar.
-
Temperature Range:
- Pyrolysis typically occurs at temperatures between 350°C and 800°C, depending on the type of feedstock and desired end products. Lower temperatures (350°C–550°C) are often used for slow pyrolysis, which maximizes solid residue (biochar) production, while higher temperatures (550°C–800°C) are used for fast pyrolysis, which favors liquid bio-oil and gaseous products.
-
Oxygen-Free Environment:
- A critical condition for pyrolysis is the absence of oxygen. This prevents combustion and ensures that the organic material decomposes thermally rather than burning. The process is carried out in a non-reactive atmosphere, often using inert gases like nitrogen or carbon dioxide.
-
Types of Pyrolysis:
- Slow Pyrolysis: Occurs at lower temperatures (350°C–550°C) with longer residence times, producing more biochar.
- Fast Pyrolysis: Occurs at higher temperatures (550°C–800°C) with rapid heating rates, maximizing liquid bio-oil yield.
- Gasification: A high-temperature form of pyrolysis (above 700°C) that primarily produces syngas (a mixture of hydrogen, carbon monoxide, and methane).
-
Applications and Equipment:
- Pyrolysis occurs in specialized reactors designed to maintain precise temperature control and an oxygen-free environment. Common types of pyrolysis equipment include:
- Fixed-Bed Reactors: Suitable for slow pyrolysis.
- Fluidized Bed Reactors: Ideal for fast pyrolysis due to their efficient heat transfer.
- Rotary Kilns: Used for large-scale industrial pyrolysis.
- Microwave Pyrolysis Systems: Emerging technology for efficient and uniform heating.
- Pyrolysis occurs in specialized reactors designed to maintain precise temperature control and an oxygen-free environment. Common types of pyrolysis equipment include:
-
Feedstock for Pyrolysis:
- Pyrolysis can process a wide range of organic materials, including:
- Biomass (wood, agricultural residues, algae).
- Municipal solid waste (plastics, rubber, textiles).
- Industrial waste (tires, sludge).
- Fossil fuels (coal, oil shale).
- Pyrolysis can process a wide range of organic materials, including:
-
End Products:
- The pyrolysis process yields three main types of products:
- Gaseous Products: Syngas (hydrogen, carbon monoxide, methane) used for energy generation or chemical synthesis.
- Liquid Bio-Oil: A versatile fuel or chemical feedstock.
- Solid Residue (Biochar): Used as a soil amendment, carbon sequestration agent, or in filtration systems.
- The pyrolysis process yields three main types of products:
-
Industrial and Environmental Significance:
- Pyrolysis is a key technology in waste-to-energy systems, reducing landfill waste and generating renewable energy.
- It contributes to carbon neutrality by converting biomass into biochar, which sequesters carbon in the soil.
- The process is also used in the production of advanced materials, such as activated carbon and carbon nanotubes.
By understanding these key points, purchasers of pyrolysis equipment and consumables can make informed decisions about the type of system and feedstock that best suit their needs, ensuring optimal efficiency and output.
Summary Table:
Aspect | Details |
---|---|
Definition | Thermal decomposition of organic materials in the absence of oxygen. |
Temperature Range | 350°C–800°C (slow pyrolysis: 350°C–550°C; fast pyrolysis: 550°C–800°C). |
Key Products | Gaseous syngas, liquid bio-oil, solid biochar. |
Applications | Waste management, energy production, chemical manufacturing. |
Equipment | Fixed-bed reactors, fluidized bed reactors, rotary kilns, microwave systems. |
Feedstock | Biomass, municipal solid waste, industrial waste, fossil fuels. |
Ready to explore pyrolysis solutions for your industry? Contact us today to get started!