PVD (Physical Vapor Deposition) coating is a versatile process used to apply thin, durable, and functional layers to various substrates. The process involves vaporizing a solid material in a vacuum and depositing it onto a substrate, forming a thin film. The choice of chemical used in PVD coating depends on the desired properties of the final product, such as hardness, wear resistance, corrosion resistance, or aesthetic appeal. Common materials used in PVD coatings include metals, alloys, ceramics, and specialized compounds like nitrides, carbides, and borides. These materials are selected based on their ability to enhance the performance and appearance of the coated product across industries such as aerospace, automotive, electronics, and decorative applications.
Key Points Explained:
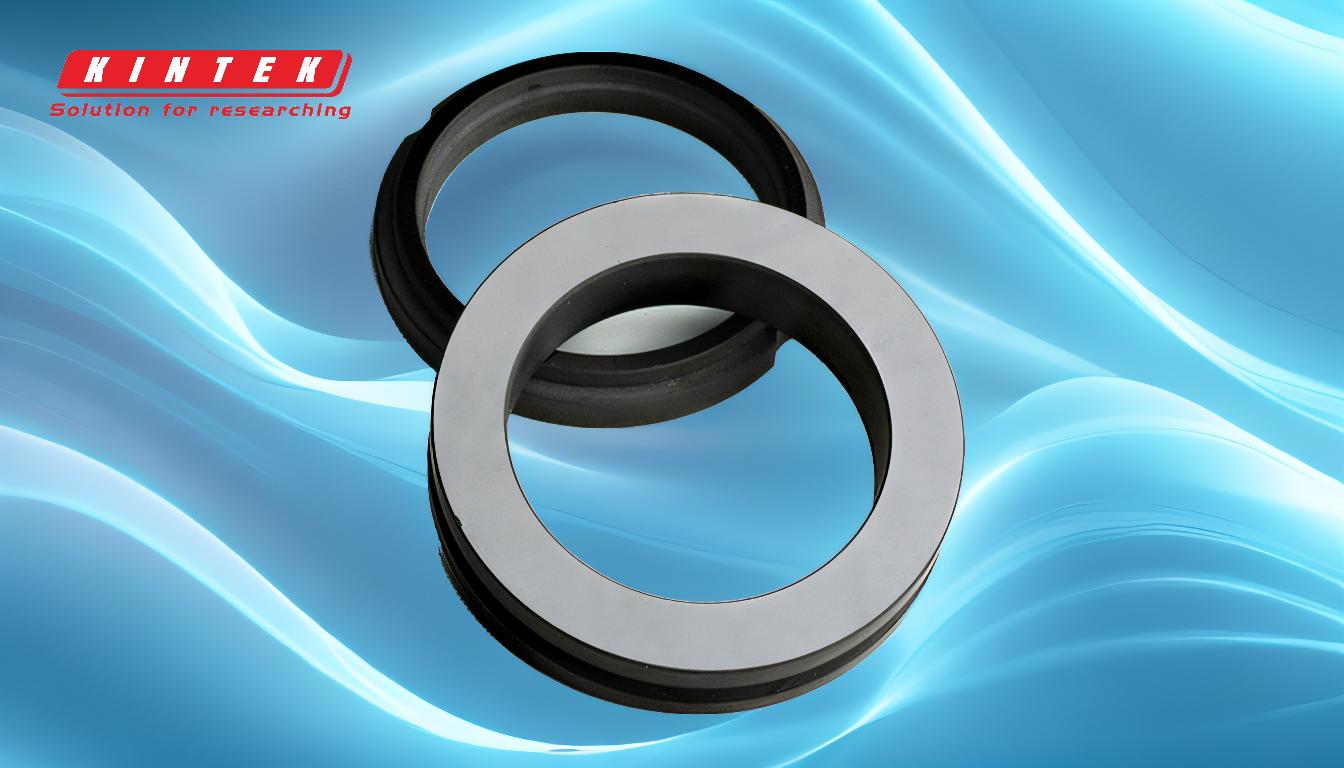
-
Common PVD Coating Materials:
- Metals: Titanium, zirconium, aluminum, stainless steel, and copper are frequently used in PVD coatings. Gold is also popular, especially in aerospace electronics for its conductivity and corrosion resistance.
- Alloys: Combinations of metals like titanium-aluminum (TiAl) are used to create coatings with enhanced properties.
- Ceramics: Materials like titanium nitride (TiN), chromium nitride (CrN), and titanium carbonitride (TiCN) are widely used for their hardness and wear resistance.
-
Specialized Compounds:
- Nitrides: Titanium Nitride (TiN), Chromium Nitride (CrN), and Titanium Aluminum Nitride (TiAlN) are common nitride coatings used for their hardness and resistance to wear and corrosion.
- Carbides: Titanium Carbonitride (TiCN) is a hybrid material that combines the properties of carbides and nitrides, offering high hardness and low friction.
- Borides: Titanium Boron Nitride (TiBN) is used for its exceptional hardness and thermal stability.
-
Reactive Gases in PVD:
- The composition of PVD coatings can be modified by introducing reactive gases during the vaporization process. For example:
- Adding nitrogen results in the formation of metal nitrides (e.g., TiN, CrN).
- Adding oxygen can create metal oxides, which are useful for optical coatings.
- Adding carbon can produce metal carbides (e.g., TiC), which are known for their hardness and wear resistance.
- The composition of PVD coatings can be modified by introducing reactive gases during the vaporization process. For example:
-
Applications of PVD Coatings:
- Decorative Applications: TiN is widely used for its gold-like appearance in watches, jewelry, and hardware parts. Cr2N is used for silver films in decorative items.
- Functional Applications: AlCr coatings extend the service life of tools and machine parts, while ITO (Indium Tin Oxide) thin films are used in LCDs, plasma displays, and touch panels due to their conductivity and hardness.
- Industrial Applications: TiAlN and TiBN coatings are used in aerospace and automotive components for their high-temperature stability and wear resistance.
-
PVD Coating Process:
- Vaporization: The solid material is vaporized using techniques such as heated crucibles, electron beams, ion bombardment, or cathodic arc evaporation.
- Deposition: The vaporized material is deposited atom by atom onto the substrate in a vacuum chamber, ensuring a clean and uniform coating.
- Modification: Reactive gases can be introduced to alter the composition and properties of the coating.
-
Substrates for PVD Coatings:
- PVD coatings can be applied to a wide range of substrates, including:
- Metals: Stainless steel, aluminum, and titanium.
- Non-Metals: Nylon, plastics, glass, and ceramics.
- PVD coatings can be applied to a wide range of substrates, including:
-
Benefits of PVD Coatings:
- Durability: PVD coatings are known for their hardness and resistance to wear, corrosion, and high temperatures.
- Aesthetic Appeal: Coatings like TiN and Cr2N provide decorative finishes with a metallic sheen.
- Functionality: Coatings like ITO and AlCr enhance the performance of electronic components and industrial tools.
By understanding the materials and processes involved in PVD coating, purchasers can select the appropriate chemicals and techniques to meet the specific requirements of their applications.
Summary Table:
Category | Examples | Properties |
---|---|---|
Metals | Titanium, Zirconium, Aluminum, Gold | Conductivity, Corrosion Resistance |
Alloys | Titanium-Aluminum (TiAl) | Enhanced Strength, Wear Resistance |
Ceramics | Titanium Nitride (TiN), Chromium Nitride (CrN), Titanium Carbonitride (TiCN) | Hardness, Wear Resistance, Corrosion Resistance |
Specialized Compounds | Titanium Aluminum Nitride (TiAlN), Titanium Boron Nitride (TiBN) | High-Temperature Stability, Exceptional Hardness |
Reactive Gases | Nitrogen, Oxygen, Carbon | Forms Nitrides, Oxides, and Carbides for Enhanced Properties |
Need the perfect PVD coating for your application? Contact our experts today for tailored solutions!