A muffle furnace is a critical piece of equipment used in high-temperature applications, such as material testing, heat treatment, and chemical analysis. The type of gas used in a muffle furnace depends on the specific application and the desired atmosphere within the furnace. Typically, muffle furnaces operate in an air atmosphere, but inert gases like nitrogen or argon are used when an oxygen-free environment is required to prevent oxidation or contamination of the materials being heated. Understanding the role of gases in a muffle furnace helps ensure optimal performance and accurate results for various industrial and laboratory processes.
Key Points Explained:
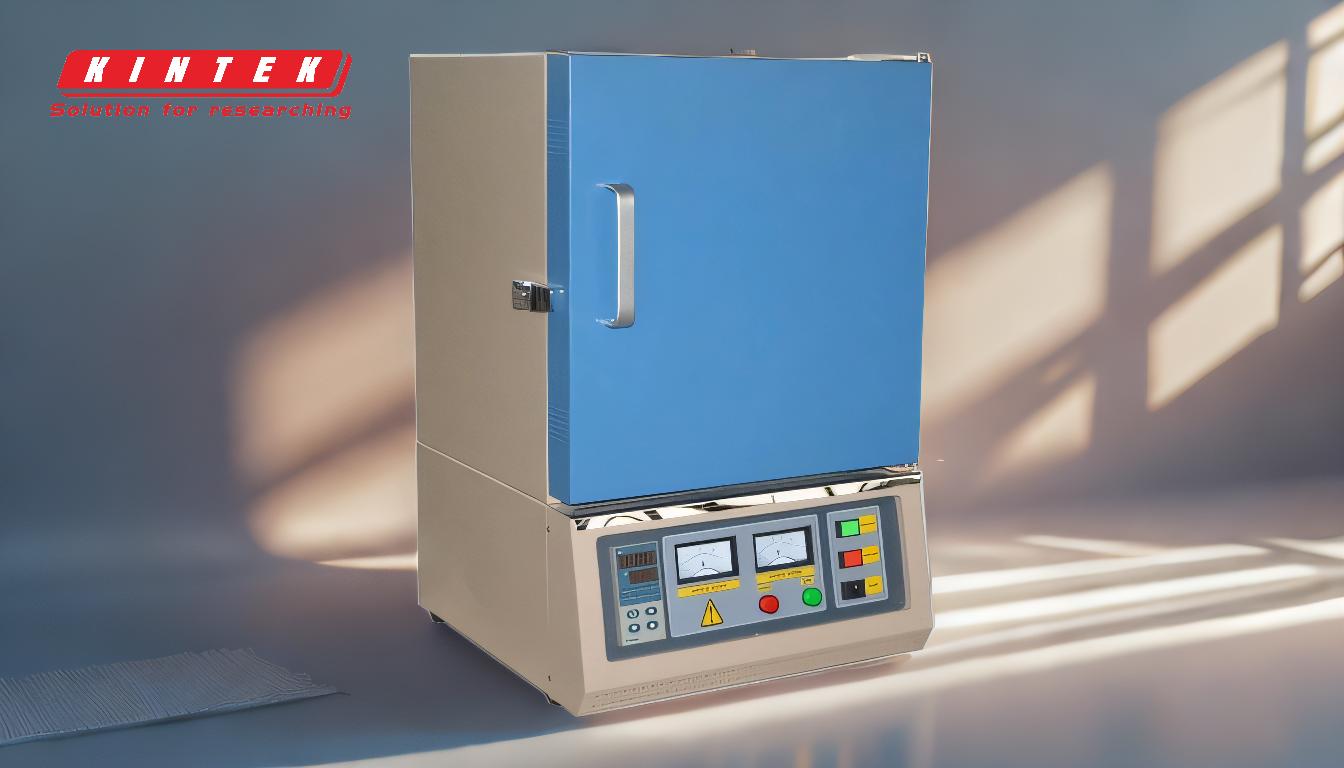
-
Primary Atmosphere in a Muffle Furnace:
- Muffle furnaces are often designed to operate in an air atmosphere, which is the most common and cost-effective option. This is suitable for processes where oxidation is not a concern.
- The air atmosphere provides sufficient oxygen for combustion or oxidation reactions, making it ideal for applications like ashing, calcination, or sintering.
-
Use of Inert Gases:
- In applications where oxidation or contamination must be avoided, inert gases such as nitrogen or argon are introduced into the muffle furnace. These gases create an oxygen-free environment, which is essential for processes like annealing, brazing, or heat-treating sensitive materials.
- Nitrogen is often preferred due to its cost-effectiveness and availability, while argon is used for more sensitive applications due to its higher inertness.
-
Role of Gases in Temperature Control:
- The choice of gas can influence the temperature uniformity and stability within the furnace. Inert gases help maintain consistent heating conditions, especially in high-temperature applications.
- For example, when using a muffle furnace for sintering ceramics, an inert gas atmosphere ensures that the material does not react with oxygen, preserving its properties.
-
Specialized Applications Requiring Specific Gases:
- Some processes may require specialized gases, such as hydrogen or forming gas (a mixture of hydrogen and nitrogen), to achieve specific chemical reactions or reduce oxides.
- These gases are typically used in controlled environments and require additional safety measures due to their flammability.
-
Importance of Gas Purity:
- The purity of the gas used in a muffle furnace is critical, especially in high-precision applications. Impurities in the gas can lead to contamination or inconsistent results.
- High-purity gases (e.g., 99.999% pure nitrogen or argon) are often recommended for sensitive processes.
-
Safety Considerations:
- When using gases in a muffle furnace, proper ventilation and gas handling procedures are essential to prevent leaks, explosions, or exposure to hazardous gases.
- Safety features, such as gas detectors and automatic shut-off valves, are often integrated into the furnace design to mitigate risks.
By understanding the role of gases in a muffle furnace, users can select the appropriate atmosphere for their specific application, ensuring optimal performance and accurate results. Whether operating in an air atmosphere or using inert gases, the choice of gas plays a crucial role in achieving the desired outcomes.
Summary Table:
Gas Type | Common Use Cases | Key Benefits |
---|---|---|
Air | Ashing, calcination, sintering | Cost-effective, provides oxygen for oxidation reactions |
Nitrogen | Annealing, brazing, heat-treating sensitive materials | Cost-effective, creates oxygen-free environment |
Argon | Sensitive applications requiring higher inertness | Highly inert, prevents contamination |
Hydrogen/Forming Gas | Specialized processes like oxide reduction | Enables specific chemical reactions |
Need help selecting the right gas for your muffle furnace? Contact our experts today for personalized guidance!