In controlled atmosphere processes, the choice of gases depends on the specific application, material being processed, and desired outcomes. Commonly used gases include inert gases like nitrogen (N₂), argon (Ar), and helium (He), as well as reactive gases such as hydrogen (H₂). These gases are selected based on their properties, such as inertness, reactivity, diffusion rates, and availability. Inert gases are primarily used to prevent oxidation and contamination, while reactive gases can facilitate specific chemical reactions or surface treatments. The selection of gases is also influenced by factors like temperature, material compatibility, and process requirements.
Key Points Explained:
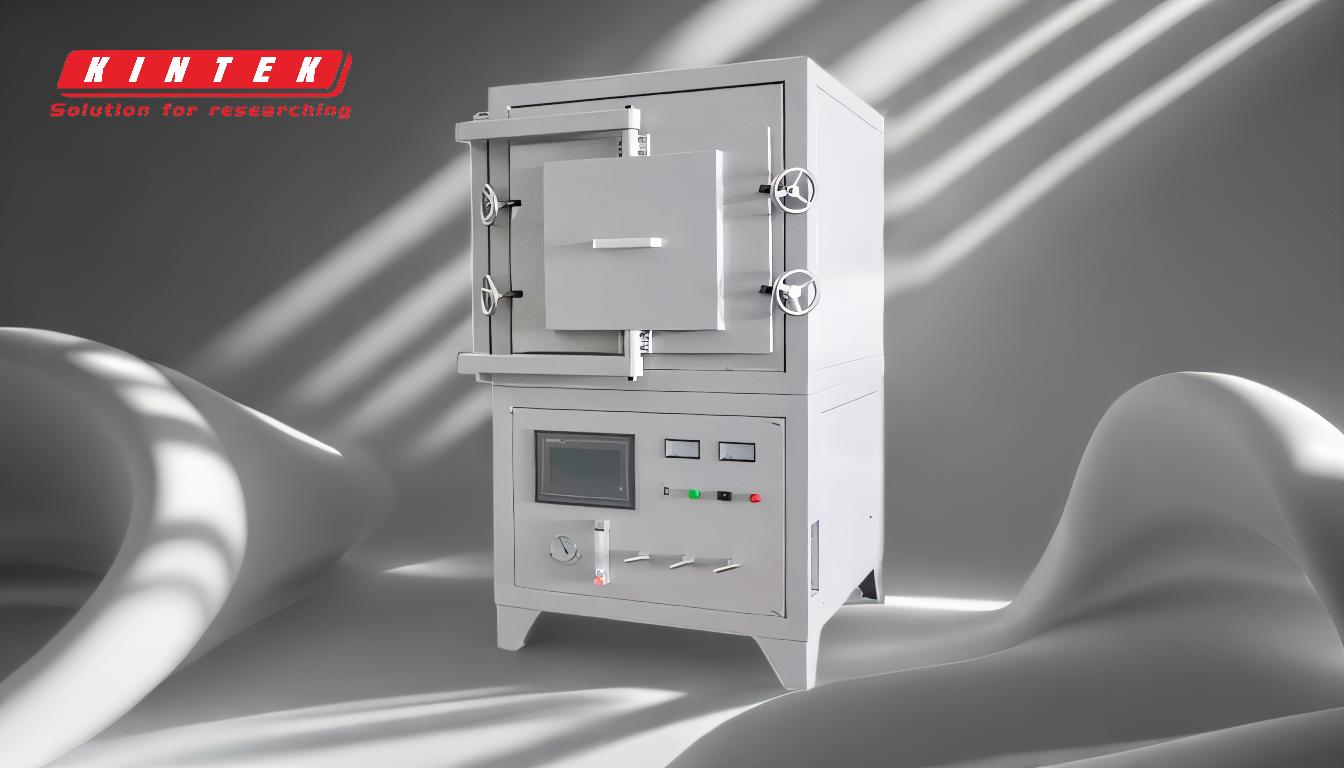
-
Inert Gases in Controlled Atmospheres:
- Nitrogen (N₂): Nitrogen is the most commonly used inert gas due to its high natural abundance, cost-effectiveness, and excellent diffusion properties. It is widely used in processes like annealing, neutral quenching, and tempering to prevent oxidation and decarburization of metals.
- Argon (Ar): Argon is another popular inert gas, especially in high-temperature applications. It is denser than nitrogen and provides better protection against oxidation in sensitive processes like sintering and brazing.
- Helium (He): Helium is less commonly used due to its higher cost but is valued for its high thermal conductivity and low molecular weight. It is often used in specialized applications where rapid cooling or heat transfer is required.
-
Reactive Gases in Controlled Atmospheres:
- Hydrogen (H₂): Hydrogen is a reactive gas used in processes like annealing and sintering to reduce oxides and remove surface contaminants. It is highly effective but requires careful handling due to its flammability and explosive nature.
- Endothermic Gas: This is a mixture of hydrogen, nitrogen, and carbon monoxide, often used in carburizing and neutral hardening processes. It provides a reducing atmosphere that prevents oxidation while allowing carbon diffusion into the material.
- Exothermic Gas: A mixture of nitrogen, carbon dioxide, and small amounts of hydrogen, exothermic gas is used for processes requiring a protective atmosphere with minimal reactivity.
-
Factors Influencing Gas Selection:
- Material Compatibility: The choice of gas depends on the material being processed. For example, argon is preferred for titanium and other reactive metals, while nitrogen is suitable for steel and non-reactive metals.
- Temperature Requirements: High-temperature processes may require gases with higher thermal stability, such as argon or helium.
- Purity and Contamination Control: High-purity gases are essential in processes where even minor contamination can affect the final product quality.
- Cost and Availability: Nitrogen is often favored due to its low cost and widespread availability, while argon and helium are used in more specialized applications.
-
Applications of Controlled Atmosphere Gases:
- Annealing: Nitrogen and argon are commonly used to prevent oxidation and maintain material properties during annealing.
- Sintering: Inert gases like argon are used to create a protective environment for powder metallurgy and ceramic sintering.
- Brazing: Hydrogen or hydrogen-nitrogen mixtures are used to reduce oxides and ensure strong, clean joints.
- Nitriding: Nitrogen-based atmospheres are used to introduce nitrogen into the surface of metals, enhancing hardness and wear resistance.
-
Safety Considerations:
- Hydrogen Handling: Due to its flammability, hydrogen requires strict safety protocols, including leak detection and proper ventilation.
- Inert Gas Monitoring: While inert gases like nitrogen and argon are non-toxic, they can displace oxygen in confined spaces, posing a suffocation risk. Proper monitoring and ventilation are essential.
By carefully selecting and controlling the gases used in controlled atmosphere processes, manufacturers can achieve precise results, improve material properties, and ensure safety in their operations.
Summary Table:
Gas Type | Key Properties | Common Applications |
---|---|---|
Nitrogen (N₂) | High abundance, cost-effective, excellent diffusion properties | Annealing, neutral quenching, tempering |
Argon (Ar) | Denser than nitrogen, better oxidation protection in high temperatures | Sintering, brazing, high-temperature processes |
Helium (He) | High thermal conductivity, low molecular weight, rapid cooling capabilities | Specialized applications requiring rapid heat transfer |
Hydrogen (H₂) | Highly reactive, reduces oxides, flammable | Annealing, sintering, oxide reduction |
Endothermic Gas | Mixture of H₂, N₂, CO; prevents oxidation, allows carbon diffusion | Carburizing, neutral hardening |
Exothermic Gas | Mixture of N₂, CO₂, H₂; minimal reactivity | Processes requiring protective atmospheres |
Need help selecting the right gas for your controlled atmosphere processes? Contact our experts today for tailored solutions!