Electric resistance heating systems, while efficient and widely used, have several notable disadvantages. These include high operating costs due to the expense of electricity, longer heating times for certain applications like melting metals, and limitations in temperature control. Additionally, they may require consistent professional maintenance, which can add to the overall cost and complexity of operation. These factors make electric resistance heating systems less suitable for large-scale or high-temperature industrial applications, as well as less cost-effective compared to gas or oil-based systems.
Key Points Explained:
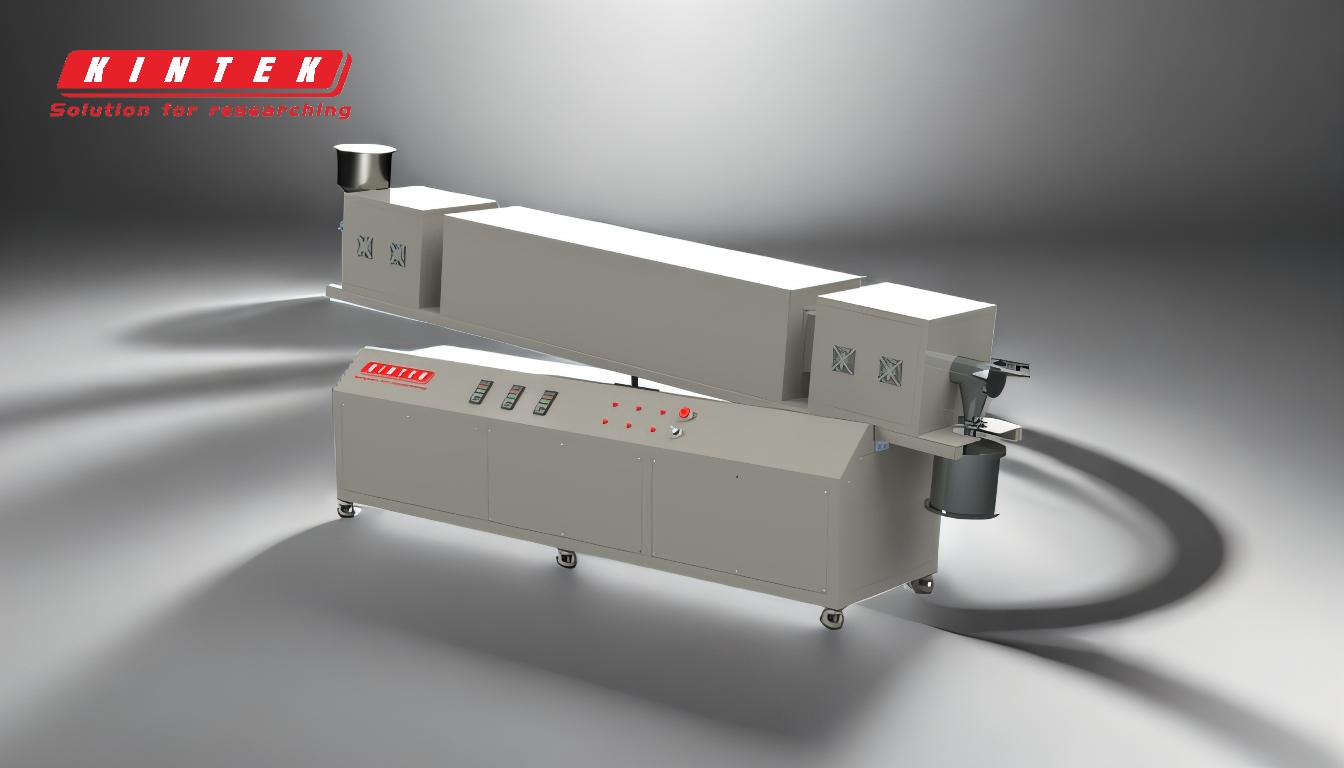
-
High Operating Costs:
- Electricity is generally more expensive than gas or oil, making electric resistance heating systems costly to operate over time.
- This is particularly significant in industrial settings where large amounts of energy are required to maintain high temperatures.
- For homeowners, the higher cost of electricity can lead to increased utility bills, especially during colder months when heating demands are higher.
-
Longer Heating Times:
- Electric resistance furnaces take longer to reach the necessary temperatures for melting metals compared to other types of furnaces.
- This delay can be a significant disadvantage in mining and industrial operations where time efficiency is crucial.
- The slower heating process also limits the suitability of these systems for large-scale operations that require rapid melting of large quantities of metal.
-
Limited Temperature Control:
- In direct resistance heating systems, automatic temperature control is challenging because the current is not easily variable.
- This limitation can lead to inefficiencies in maintaining precise temperatures, which is critical in many industrial processes.
- The lack of fine control over temperature can result in inconsistent heating, affecting the quality of the final product.
-
Maintenance and Repair Requirements:
- While electric furnaces are generally sturdy, they can develop complex issues that are difficult for homeowners to resolve without professional help.
- The need for consistent professional repairs can add to the overall cost and inconvenience of using electric resistance heating systems.
- In industrial settings, downtime for repairs can also impact productivity and increase operational costs.
-
Unsuitability for Large-Scale Operations:
- Electric resistance heating systems are typically used for small to medium-sized operations due to their limitations in reaching high temperatures quickly.
- They are often inadequate for melting large quantities of metal, making them less viable for large-scale industrial applications.
- This limitation can force businesses to invest in additional or alternative heating solutions, further increasing costs.
In summary, while electric resistance heating systems offer certain advantages such as cleanliness and ease of installation, their disadvantages—high operating costs, longer heating times, limited temperature control, maintenance requirements, and unsuitability for large-scale operations—make them less favorable in many scenarios. These factors should be carefully considered when selecting a heating system for industrial or residential use.
Summary Table:
Disadvantage | Key Details |
---|---|
High Operating Costs | Electricity is more expensive than gas or oil, leading to higher utility bills. |
Longer Heating Times | Slower heating process, unsuitable for rapid melting in industrial settings. |
Limited Temperature Control | Difficulty in maintaining precise temperatures, affecting process efficiency. |
Maintenance Requirements | Complex repairs often require professional help, increasing costs and downtime. |
Unsuitability for Large-Scale | Inadequate for high-temperature, large-scale industrial applications. |
Need a more efficient heating solution? Contact us today to explore alternatives tailored to your needs!