Heat treatment is a widely used process to enhance the mechanical properties of metals, particularly their hardness. However, not all metals respond to heat treatment in the same way. Some metals, due to their inherent properties or crystal structures, cannot be hardened through heat treatment. Understanding which metals fall into this category is crucial for material selection in engineering and manufacturing applications. Below, we explore the key reasons why certain metals cannot be hardened by heat treatment and provide examples of such metals.
Key Points Explained:
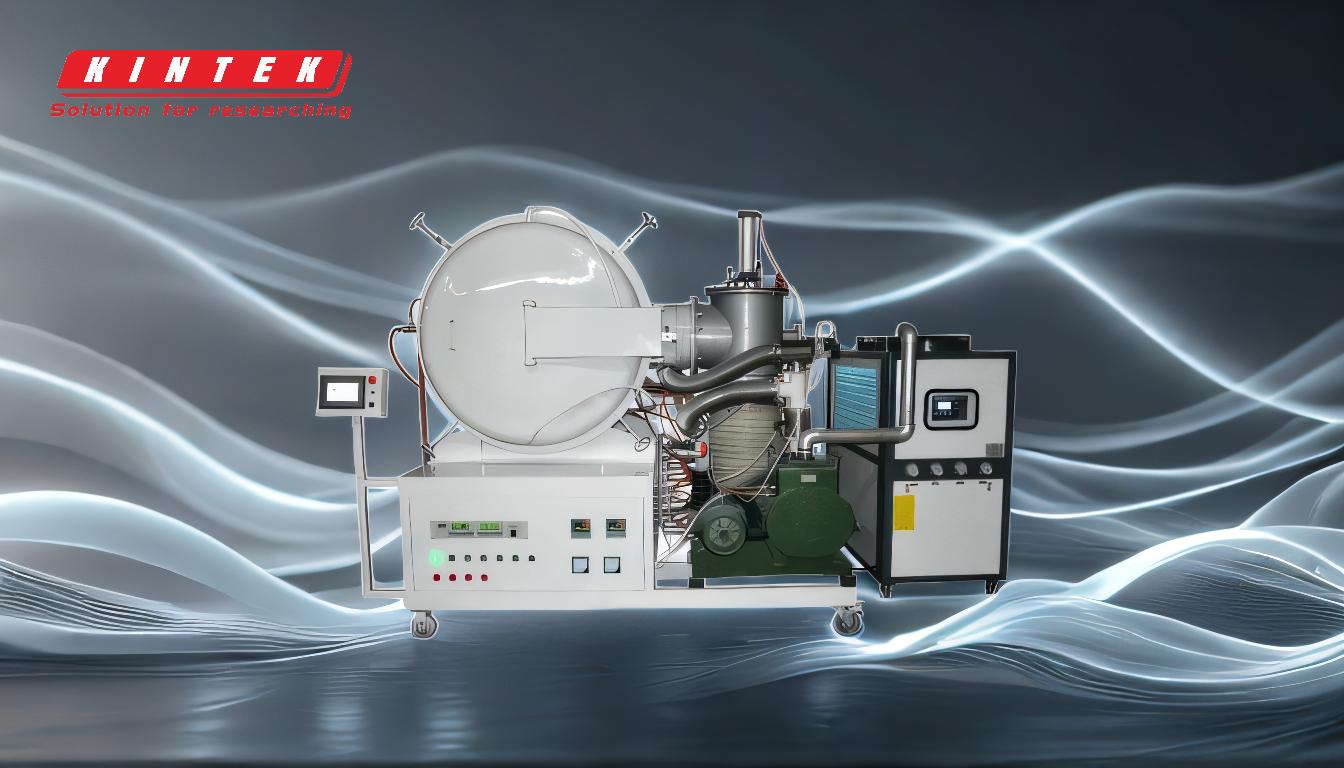
-
Definition of Heat Treatment and Hardening
Heat treatment involves heating and cooling metals to alter their physical and mechanical properties. Hardening, a subset of heat treatment, typically involves heating the metal to a specific temperature (austenitizing) and then rapidly cooling it (quenching) to increase hardness. However, this process relies on the metal's ability to undergo phase transformations, which is not universal across all metals. -
Metals That Cannot Be Hardened by Heat Treatment
- Pure Metals: Pure metals, such as pure iron, aluminum, and copper, lack the necessary alloying elements to form hard phases like martensite. Without these alloying elements, heat treatment cannot induce significant hardening.
- Non-Ferrous Metals: Many non-ferrous metals, such as aluminum and copper alloys, do not undergo the same phase transformations as ferrous metals (e.g., steel). For example, aluminum alloys rely on precipitation hardening rather than traditional heat treatment for strengthening.
- Austenitic Stainless Steels: These steels, such as 304 and 316 grades, have a stable austenitic structure that does not transform into martensite upon quenching, making them resistant to hardening through heat treatment.
- Lead and Tin: These low-melting-point metals do not respond to heat treatment due to their soft and malleable nature.
-
Reasons Why Certain Metals Cannot Be Hardened
- Lack of Phase Transformation: Metals that cannot undergo phase transformations (e.g., austenite to martensite) cannot be hardened through heat treatment. This is common in non-ferrous metals and some stainless steels.
- Stable Crystal Structures: Metals with stable crystal structures, such as austenitic stainless steels, do not change their structure significantly when heated and cooled.
- Absence of Alloying Elements: Alloying elements like carbon are critical for hardening in ferrous metals. Pure metals and some alloys lack these elements, limiting their response to heat treatment.
-
Alternative Methods for Hardening
- Precipitation Hardening: Used for aluminum and some stainless steels, this process involves forming fine particles within the metal to increase strength.
- Cold Working: Processes like rolling, drawing, or hammering can increase hardness by introducing dislocations in the metal's crystal structure.
- Surface Hardening: Techniques like carburizing or nitriding can harden the surface of metals without altering their core properties.
-
Practical Implications for Material Selection
- Engineers and manufacturers must consider the limitations of heat treatment when selecting materials for specific applications. For example, austenitic stainless steels are chosen for their corrosion resistance rather than hardness, while aluminum alloys are selected for their lightweight and strength-to-weight ratio.
- Understanding these limitations helps avoid costly mistakes and ensures the right material is chosen for the intended application.
In summary, while heat treatment is a powerful tool for enhancing the hardness of many metals, it is not universally applicable. Pure metals, certain non-ferrous metals, and austenitic stainless steels are examples of materials that cannot be hardened through traditional heat treatment processes. Instead, alternative methods like precipitation hardening, cold working, or surface hardening may be employed to achieve the desired mechanical properties.
Summary Table:
Category | Examples | Reasons |
---|---|---|
Pure Metals | Pure iron, aluminum, copper | Lack alloying elements for phase transformation (e.g., martensite formation) |
Non-Ferrous Metals | Aluminum alloys, copper alloys | Do not undergo phase transformations like ferrous metals |
Austenitic Stainless Steels | 304, 316 grades | Stable austenitic structure resists martensite transformation |
Low-Melting-Point Metals | Lead, tin | Soft and malleable nature prevents hardening |
Need help selecting the right material for your application? Contact our experts today for personalized advice!