Annealing furnaces are specialized equipment designed to heat materials above their recrystallization temperature to improve ductility, relieve internal stresses, and enhance mechanical properties. These furnaces are essential in industries where material properties need to be optimized for further processing. The most common types of furnaces used in annealing include roller hearth furnaces, pusher furnaces, box furnaces, pot/pit furnaces, conveyor belt furnaces, and integral-quench furnaces. Each type is chosen based on the specific requirements of the material being treated and the desired outcome of the annealing process.
Key Points Explained:
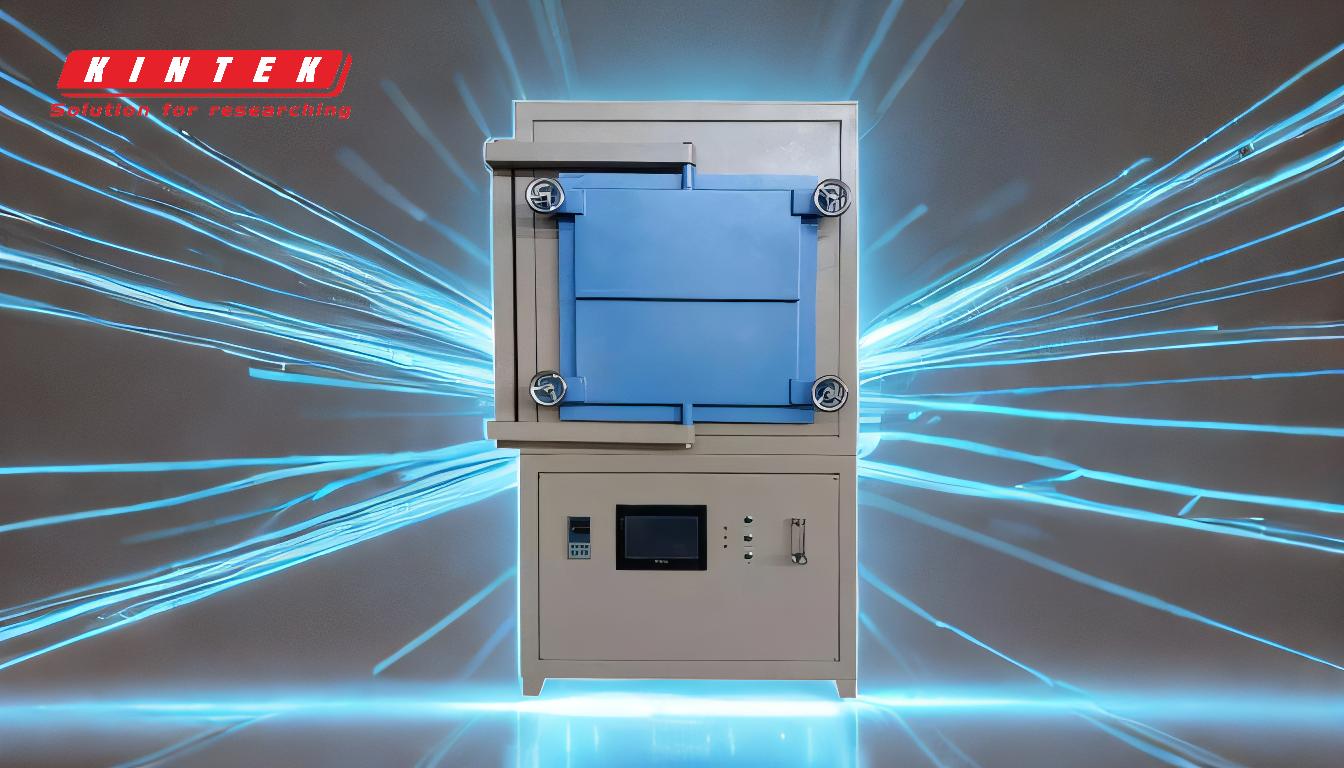
-
Purpose of Annealing Furnaces:
- Annealing furnaces are used to heat materials above their recrystallization temperature, making them more ductile and easier to work with. This process helps in relieving internal stresses, improving mechanical properties, and preparing the material for further machining or cold working.
-
Types of Annealing Furnaces:
- Roller Hearth Furnaces: These furnaces are ideal for continuous processing of materials. They use rollers to move the material through the furnace, ensuring uniform heating and cooling.
- Pusher Furnaces: These are used for batch processing and are suitable for materials that require a longer heating cycle. They push the material through the furnace in a controlled manner.
- Box Furnaces: These are versatile and can handle a variety of materials and shapes. They are often used for small to medium-sized batches.
- Pot/Pit Furnaces: These are used for annealing large or heavy components. They are typically used in industries like aerospace and automotive.
- Conveyor Belt Furnaces: These are designed for high-volume production and are ideal for materials that require consistent and rapid heating and cooling.
- Integral-Quench Furnaces: These furnaces combine heating and quenching in a single unit, making them efficient for processes that require rapid cooling after heating.
-
Features of Annealing Furnaces:
- Temperature Control: Annealing furnaces can reach temperatures up to 1800°C and maintain high uniformity, typically within +/-5°C.
- Programmable Controllers: They are equipped with multisegment microprocessor-based programmable temperature controllers for precise control over the heating process.
- Safety Features: These include individual burner flame safety, over-temperature protection, and gas/vacuum purging applications to ensure safe operation.
- Heating Elements: High-quality heating elements are used to ensure efficient and uniform heating.
- Data Logging: Programmable PID controllers with data logging software allow for detailed monitoring and analysis of the annealing process.
-
Atmosphere Control:
- The furnace atmosphere plays a crucial role in the annealing process. It can be either chemically inert to protect the material from oxidation or chemically active to allow surface changes, such as carburizing or nitriding.
-
Applications:
- Annealing furnaces are used in various industries, including metalworking, automotive, aerospace, and electronics. They are essential for processes that require precise control over material properties, such as hardening, tempering, and stress relief.
In conclusion, the choice of annealing furnace depends on the specific requirements of the material and the desired outcome of the annealing process. Each type of furnace offers unique features and benefits, making them suitable for different applications and industries.
Summary Table:
Type of Furnace | Key Features | Applications |
---|---|---|
Roller Hearth Furnaces | Continuous processing, uniform heating and cooling | Ideal for materials requiring consistent processing |
Pusher Furnaces | Batch processing, longer heating cycles | Suitable for materials needing controlled heating |
Box Furnaces | Versatile, handles various materials and shapes | Small to medium-sized batches |
Pot/Pit Furnaces | Designed for large or heavy components | Aerospace, automotive industries |
Conveyor Belt Furnaces | High-volume production, rapid heating and cooling | Materials requiring consistent and rapid processing |
Integral-Quench Furnaces | Combines heating and quenching in one unit | Processes requiring rapid cooling after heating |
Need help selecting the right annealing furnace for your application? Contact our experts today for personalized advice!