Hot forging is a manufacturing process that involves shaping metal using localized compressive forces at high temperatures. The materials used in hot forging are typically metals that can withstand high temperatures and deformation without cracking or losing their structural integrity. Commonly used materials include carbon steels, alloy steels, stainless steels, aluminum, copper, and titanium. Each material is chosen based on its mechanical properties, such as strength, ductility, and resistance to wear, as well as the specific application requirements. The selection of material is crucial to ensure the final forged product meets the desired performance standards.
Key Points Explained:
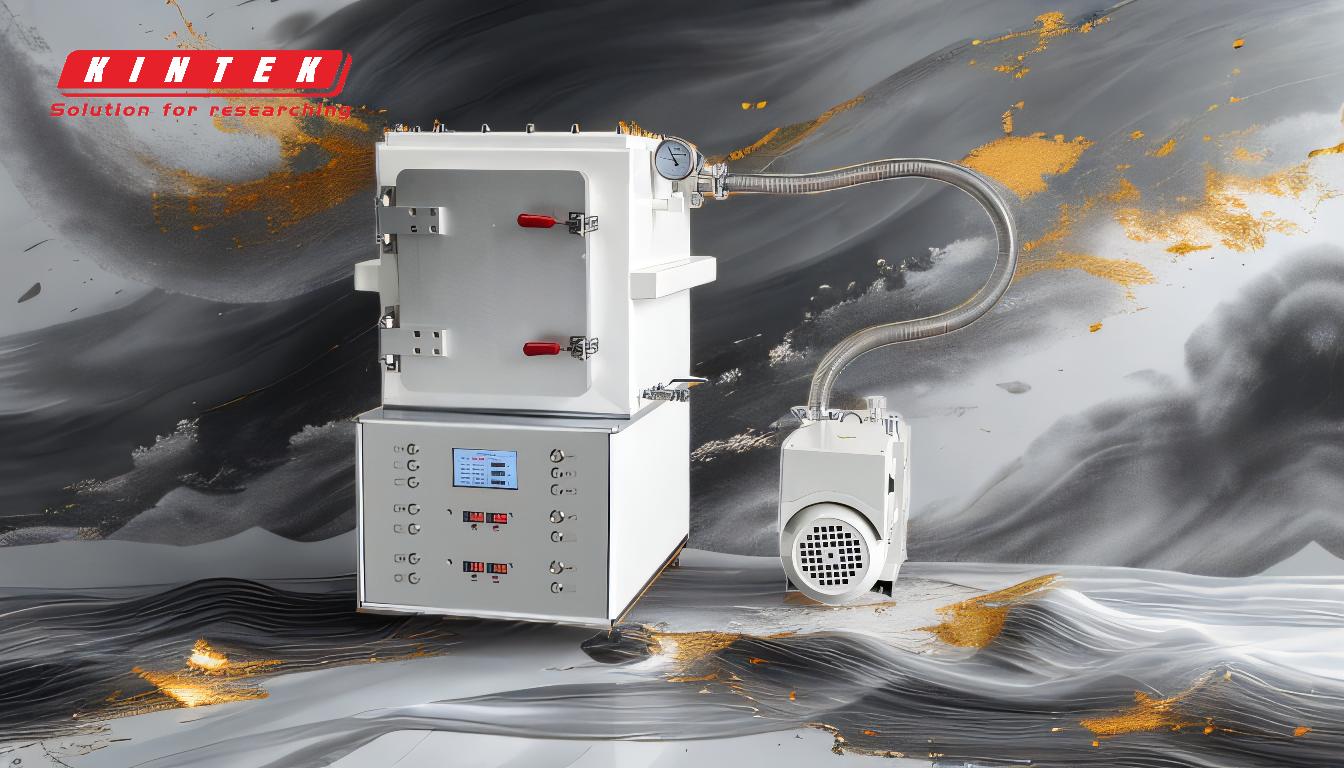
-
Carbon Steels:
- Carbon steels are widely used in hot forging due to their excellent strength and durability. They contain varying amounts of carbon, which influences their hardness and tensile strength.
- Low-carbon steels (up to 0.3% carbon) are more ductile and easier to forge, making them suitable for applications requiring good formability.
- Medium and high-carbon steels (0.3% to 1.5% carbon) are stronger and harder, making them ideal for components that require high wear resistance and strength, such as gears and shafts.
-
Alloy Steels:
- Alloy steels are carbon steels with additional alloying elements like chromium, nickel, molybdenum, and vanadium. These elements enhance the material's properties, such as toughness, hardness, and resistance to corrosion and wear.
- Alloy steels are often used in hot forging for applications that demand high strength and durability, such as automotive parts, aerospace components, and heavy machinery.
-
Stainless Steels:
- Stainless steels contain a significant amount of chromium (at least 10.5%), which provides excellent corrosion resistance. They are also known for their high strength and ability to withstand extreme temperatures.
- Austenitic stainless steels (e.g., 304, 316) are commonly used in hot forging for applications requiring corrosion resistance and good mechanical properties, such as in the food processing and chemical industries.
-
Aluminum:
- Aluminum is a lightweight material with excellent thermal and electrical conductivity. It is relatively easy to forge and offers good corrosion resistance.
- Aluminum alloys, such as 6061 and 7075, are often used in hot forging for applications where weight reduction is critical, such as in the aerospace and automotive industries.
-
Copper:
- Copper is known for its excellent electrical and thermal conductivity, as well as its corrosion resistance. It is relatively soft and easy to forge, making it suitable for electrical components, plumbing fittings, and decorative items.
- Copper alloys, such as brass (copper-zinc) and bronze (copper-tin), are also used in hot forging for applications requiring enhanced strength and wear resistance.
-
Titanium:
- Titanium is a strong, lightweight material with excellent corrosion resistance and the ability to withstand high temperatures. It is more challenging to forge due to its high strength and low thermal conductivity.
- Titanium alloys, such as Ti-6Al-4V, are commonly used in hot forging for high-performance applications in the aerospace, medical, and automotive industries.
-
Material Selection Considerations:
- Temperature Resistance: The material must withstand the high temperatures used in hot forging without losing its structural integrity.
- Ductility: The material should be able to deform without cracking during the forging process.
- Strength and Hardness: The final forged product must meet the required mechanical properties for its intended application.
- Cost and Availability: The material should be cost-effective and readily available for production.
In summary, the choice of material in hot forging depends on the specific requirements of the application, including mechanical properties, temperature resistance, and cost considerations. Each material offers unique advantages, making it suitable for different types of forged products.
Summary Table:
Material | Key Properties | Common Applications |
---|---|---|
Carbon Steels | Strength, durability, hardness, tensile strength | Gears, shafts, structural components |
Alloy Steels | Enhanced toughness, hardness, corrosion resistance | Automotive, aerospace, heavy machinery |
Stainless Steels | Corrosion resistance, high strength, extreme temperature resistance | Food processing, chemical industries |
Aluminum | Lightweight, thermal/electrical conductivity, corrosion resistance | Aerospace, automotive |
Copper | Electrical/thermal conductivity, corrosion resistance | Electrical components, plumbing fittings |
Titanium | High strength, lightweight, corrosion resistance, high-temperature resistance | Aerospace, medical, automotive |
Need help selecting the right material for your hot forging project? Contact our experts today for tailored advice!