Spark plasma sintering (SPS) is a cutting-edge sintering technology used to produce dense and homogeneous materials from powders. It employs pulsed direct current (DC) and uniaxial pressure to rapidly heat and sinter powders, enabling the creation of high-quality materials at lower temperatures and shorter times compared to conventional methods. Several manufacturers produce SPS equipment, with Kintek Solution being a notable example. Kintek prioritizes innovation and high-quality system performance, making it a leading supplier in the field. SPS is widely used in both research and commercial applications, including the production of advanced materials like body armor, rocket nozzles, and carbon fiber composites.
Key Points Explained:
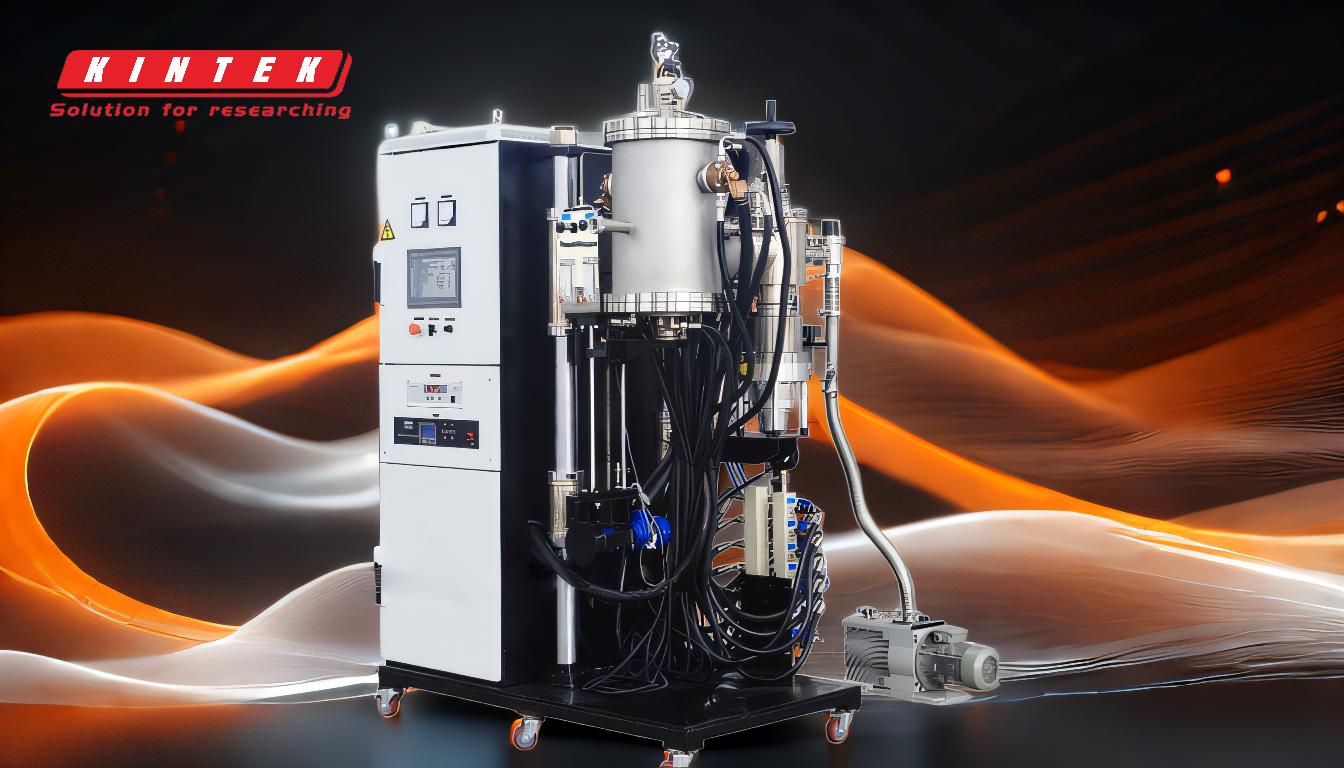
-
What is Spark Plasma Sintering (SPS)?
- SPS is an advanced sintering technique that uses pulsed direct current (DC) and uniaxial pressure to consolidate powders into dense, high-quality materials.
- It operates at lower temperatures and shorter times compared to traditional sintering methods, making it highly efficient.
- The process involves heating the powder internally and externally through a conducting die, often made of graphite, which allows for rapid heating and cooling.
-
Key Features of SPS Technology:
- Rapid Heating and Cooling: SPS enables very fast heating and cooling rates, significantly reducing processing time.
- Lower Sintering Temperatures: Materials can be sintered at temperatures several hundred degrees lower than conventional methods.
- High-Density Products: The process results in materials with high density and homogeneity, suitable for demanding applications.
- Versatility: SPS can be used to sinter a wide range of materials, including metals, ceramics, and composites.
-
Manufacturers of SPS Equipment:
- Kintek Solution: A leading manufacturer of SPS equipment, Kintek emphasizes innovation and high-quality system performance. Their systems are designed to meet the needs of both research and industrial applications.
- Other Manufacturers: While Kintek is a prominent name, other companies also produce SPS equipment, catering to various industrial and research needs.
-
Applications of SPS:
- Commercial Production: SPS is used to manufacture products like body armor, rocket nozzles, and carbon fiber composites on a commercial scale.
- Research and Development: The technology is widely used in laboratories to develop new materials and improve existing ones.
- Hybrid Materials: SPS is particularly useful for creating hybrid materials that combine the properties of different substances, such as ceramics and metals.
-
Alternative Names and Misconceptions:
- SPS is also known by other names, such as Field Assisted Sintering Technique (FAST), Electric Field Assisted Sintering (EFAS), and Direct Current Sintering (DCS).
- Despite the name "spark plasma sintering," research has shown that no plasma is actually used in the process. The name is a misnomer, but the technology remains highly effective.
-
Advantages Over Conventional Sintering:
- Energy Efficiency: Lower sintering temperatures and shorter processing times result in significant energy savings.
- Material Quality: The rapid heating and cooling rates help preserve the microstructure of the material, leading to superior mechanical properties.
- Process Control: The ability to precisely control the electrical current and pressure allows for fine-tuning of the sintering process, ensuring consistent results.
-
Future Prospects:
- As materials science continues to advance, the demand for SPS technology is expected to grow. Its ability to produce high-quality materials efficiently makes it a valuable tool for both research and industry.
- Ongoing improvements in SPS equipment, such as enhanced control systems and larger-scale production capabilities, will likely expand its applications further.
In summary, spark plasma sintering is a highly efficient and versatile sintering technology that offers significant advantages over traditional methods. Kintek Solution is a leading manufacturer of SPS equipment, known for its innovative approach and high-quality systems. The technology is widely used in both research and commercial applications, with a promising future as materials science continues to evolve.
Summary Table:
Aspect | Details |
---|---|
Process | Uses pulsed DC and uniaxial pressure to sinter powders rapidly. |
Key Features | Rapid heating/cooling, lower sintering temperatures, high-density products. |
Applications | Body armor, rocket nozzles, carbon fiber composites, and hybrid materials. |
Advantages | Energy-efficient, superior material quality, precise process control. |
Leading Manufacturer | Kintek Solution, known for innovative and high-quality SPS systems. |
Ready to explore how SPS can revolutionize your material production? Contact us today to learn more!