Sintering is a critical process in the manufacturing of ceramics, particularly fine ceramics, as it transforms powdered materials into dense, strong, and durable products. This process involves heating the ceramic powder below its melting point, allowing particles to bond through diffusion and mass transfer. Sintering enhances the material's microstructure, reducing porosity and improving mechanical properties such as strength, durability, and uniformity. Advanced techniques like microwave sintering and spark plasma sintering (SPS) further optimize the process by enabling low-temperature, rapid sintering, which minimizes grain growth and residual pores. These methods are essential for producing high-performance ceramics used in various industries, including electronics, aerospace, and biomedical applications.
Key Points Explained:
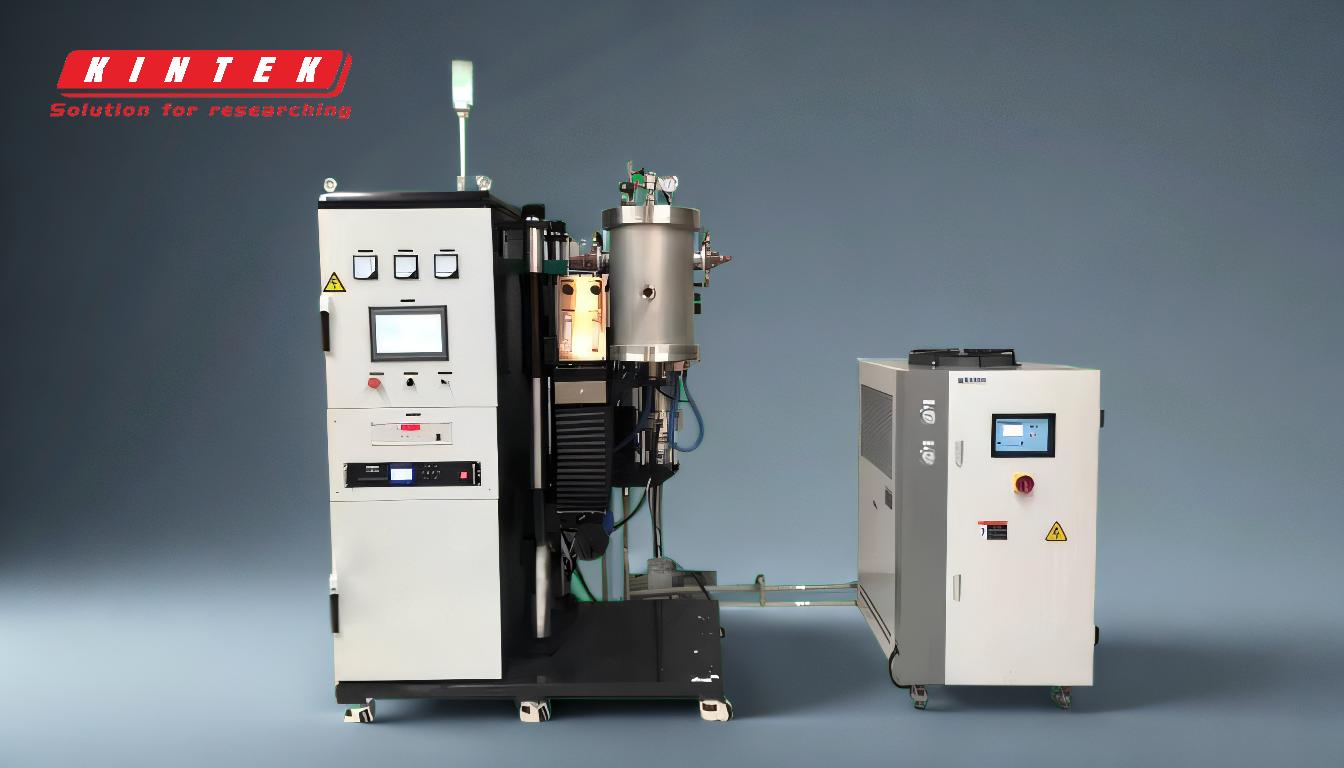
-
Purpose of Sintering in Ceramics:
- Sintering binds ceramic particles into a unified mass without melting them, ensuring cost-effectiveness and efficiency.
- It transforms ceramic powder into polycrystalline materials with specific properties, such as high strength, durability, and uniformity.
- The process is crucial for preparing fine ceramics, which are used in advanced applications due to their excellent mechanical and thermal properties.
-
Mechanisms of Sintering:
- Sintering involves diffusion and mass transfer, leading to densification and the formation of a uniform microstructure.
- Techniques like liquid phase sintering and the use of sintering aids can lower the sintering temperature and improve material properties.
- These mechanisms are essential for controlling the final properties of the ceramic, such as porosity reduction and grain size optimization.
-
Advanced Sintering Techniques:
- Microwave Sintering: Enables low-temperature and rapid sintering, reducing grain growth and residual pores. This results in denser and more uniform microstructures, enhancing the material's strength and durability.
- Spark Plasma Sintering (SPS): Uses large DC pulse heating to rapidly heat powder particles, enabling densification in a very short time. This technique is particularly useful for maintaining the structure and properties of nanomaterials and suppressing grain growth in bioceramics.
-
Benefits of Sintering:
- Improves mechanical properties such as strength, durability, and uniformity.
- Reduces porosity, leading to denser and more reliable materials.
- Allows for greater control over the manufacturing process, resulting in consistent and high-quality products.
-
Applications of Sintered Ceramics:
- Sintered ceramics are used in a wide range of industries, including electronics, aerospace, and biomedical applications.
- Examples include the production of gears, bearings, electrical contacts, and bioceramics for medical implants.
- The versatility of sintering makes it a valuable process for creating complex shapes and components with precise properties.
-
Importance in Advanced Ceramics:
- Sintering is the most important step in preparing advanced ceramics, as it determines the final properties of the material.
- Techniques like microwave sintering and SPS are particularly valuable for producing high-performance ceramics with nanostructured features.
- These advanced methods ensure that the ceramics meet the stringent requirements of modern applications, such as high strength, thermal stability, and biocompatibility.
By understanding the sintering process and employing advanced techniques, manufacturers can produce high-quality ceramics with tailored properties for specific applications. This makes sintering an indispensable step in the production of fine ceramics and other advanced materials.
Summary Table:
Aspect | Details |
---|---|
Purpose | Transforms ceramic powder into dense, strong, and durable materials. |
Mechanisms | Diffusion and mass transfer reduce porosity and improve microstructure. |
Advanced Techniques | Microwave sintering and spark plasma sintering enable low-temperature, rapid sintering. |
Benefits | Enhances strength, durability, and uniformity; reduces porosity. |
Applications | Used in electronics, aerospace, and biomedical industries. |
Learn how sintering can improve your ceramic products—contact our experts today!