Some furnaces are equipped with a second high-temperature chamber to enhance their functionality, improve operational efficiency, and meet specific process requirements. This design allows for more precise temperature control, faster heating and cooling rates, and the ability to perform multiple processes simultaneously or sequentially without interrupting the workflow. The secondary chamber can also serve as a preheating or cooling zone, reducing energy consumption and improving overall productivity. Additionally, it enables specialized applications such as annealing, sintering, or heat treatment, where controlled temperature gradients or multi-step processes are essential.
Key Points Explained:
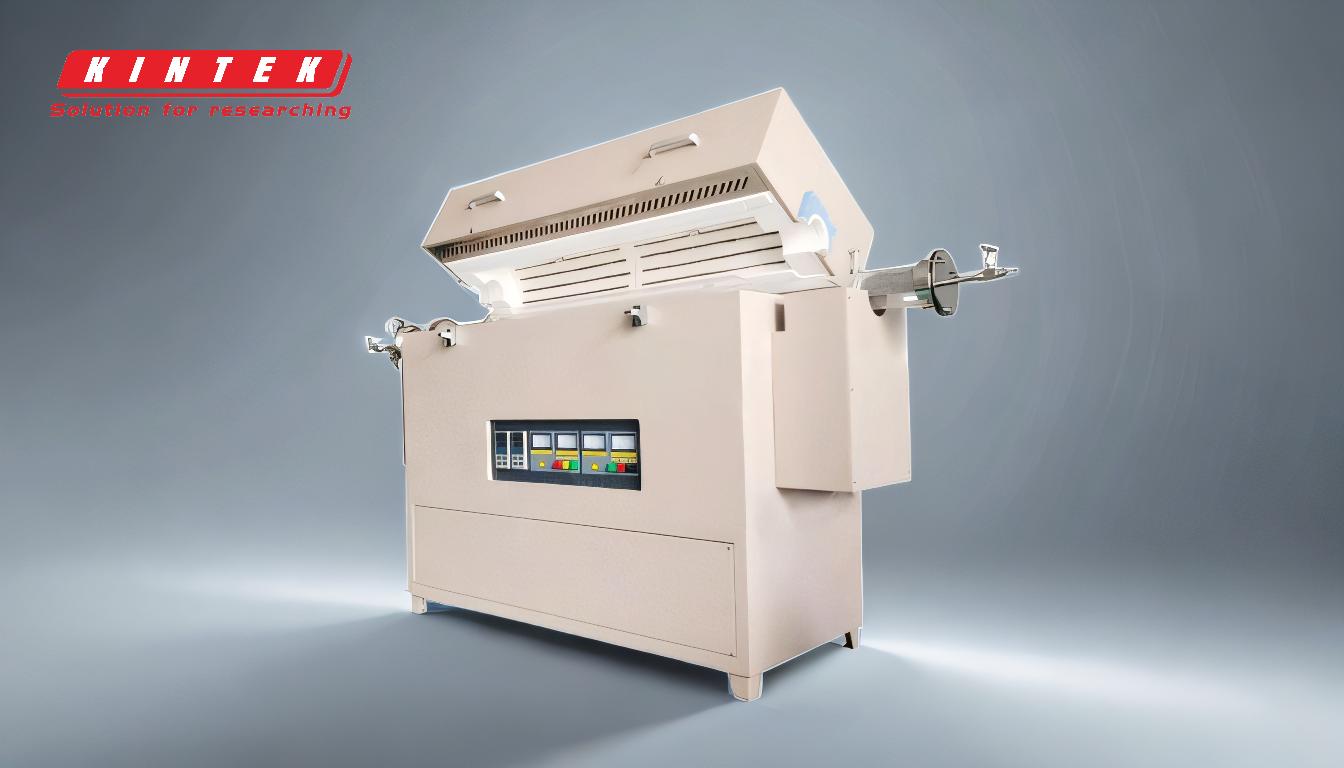
-
Enhanced Functionality and Versatility
- A second high-temperature chamber allows the furnace to perform multiple tasks simultaneously or sequentially. For example, one chamber can be used for preheating while the other is used for high-temperature processing. This dual-chamber setup is particularly useful in industries like metallurgy, ceramics, and materials science, where complex thermal processes are required.
- It also enables the furnace to handle specialized applications, such as annealing, sintering, or heat treatment, which often require precise temperature control and multi-step processes.
-
Improved Temperature Control and Uniformity
- The secondary chamber can act as a buffer zone, ensuring more uniform temperature distribution and reducing thermal shock. This is critical for processes where temperature gradients must be minimized to maintain material integrity.
- By isolating the high-temperature process in one chamber, the secondary chamber can maintain a different temperature profile, allowing for better control over the heating and cooling rates.
-
Energy Efficiency
- The second chamber can be used as a preheating or cooling zone, reducing the energy required to achieve the desired temperature in the primary chamber. This not only lowers operational costs but also minimizes thermal stress on the furnace components, extending their lifespan.
- In some cases, waste heat from the primary chamber can be utilized in the secondary chamber, further improving energy efficiency.
-
Increased Productivity
- With two chambers, the furnace can operate continuously, as one chamber can be loaded or unloaded while the other is processing materials. This reduces downtime and increases throughput, making the furnace more efficient for high-volume production environments.
- The ability to perform multiple processes in parallel also saves time and resources, making the furnace more cost-effective in the long run.
-
Specialized Applications
- Certain industrial processes, such as sintering or heat treatment, require precise control over temperature gradients and multi-step heating cycles. A dual-chamber furnace can accommodate these requirements by allowing independent temperature control in each chamber.
- For example, in sintering applications, the secondary chamber can be used to gradually cool the material, preventing cracks or deformations that might occur with rapid cooling.
-
Reduced Contamination Risk
- In processes where contamination must be minimized, such as in the production of semiconductors or advanced ceramics, the secondary chamber can serve as a clean zone. This ensures that materials are not exposed to contaminants during loading or unloading.
- The separation of chambers also allows for different atmospheres (e.g., inert gas, vacuum) to be maintained in each chamber, further reducing the risk of contamination.
By incorporating a second high-temperature chamber, furnaces can achieve greater flexibility, efficiency, and precision, making them suitable for a wide range of industrial and scientific applications.
Summary Table:
Key Benefit | Description |
---|---|
Enhanced Functionality | Perform multiple tasks simultaneously or sequentially, ideal for complex processes. |
Improved Temperature Control | Achieve uniform heating and cooling, reducing thermal shock and material stress. |
Energy Efficiency | Use secondary chamber for preheating or cooling, lowering energy consumption. |
Increased Productivity | Operate continuously with reduced downtime, boosting throughput. |
Specialized Applications | Enable precise control for annealing, sintering, and heat treatment processes. |
Reduced Contamination Risk | Maintain clean zones and separate atmospheres for contamination-sensitive tasks. |
Ready to enhance your processes with a dual-chamber furnace? Contact our experts today to find the perfect solution for your needs!