Argon is widely used in heat treatment processes due to its inert nature, which prevents chemical reactions with metals and alloys. This property makes it ideal for creating a non-reactive atmosphere, especially in industries like aerospace, where maintaining the integrity of metal surfaces is critical. Argon is particularly effective in processes such as bright annealing, quenching, and aging of metals like titanium, zirconium, nickel-based alloys, and high-strength stainless steels. While its cost is a drawback, its ability to preserve material purity and prevent oxidation or contamination during high-temperature treatments justifies its use. Additionally, argon is employed in physical vapor deposition (PVD) processes to ensure the purity of coatings.
Key Points Explained:
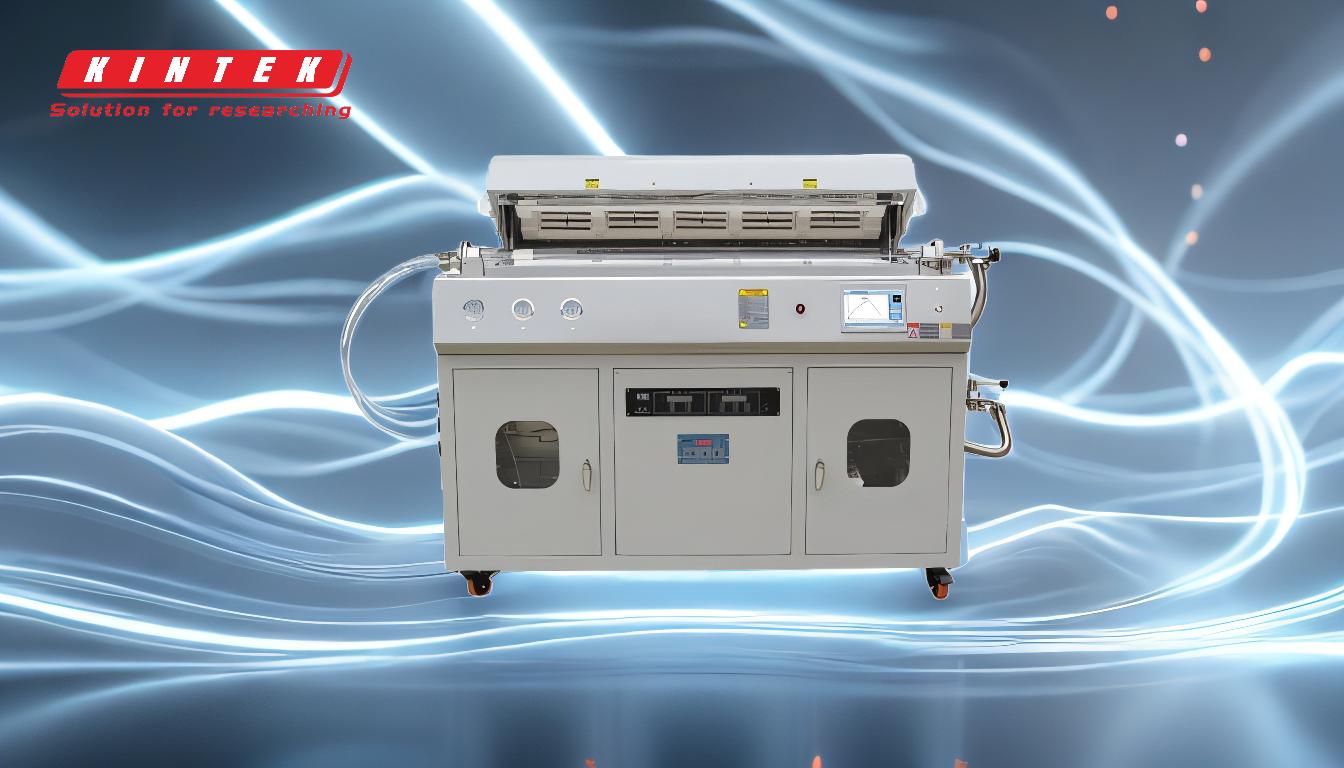
-
Inert Nature of Argon:
- Argon is an inert gas, meaning it does not chemically react with metals or other materials. This property is crucial in heat treatment processes, where maintaining the integrity of the metal surface is essential.
- Its inertness ensures that metals do not oxidize or undergo unwanted chemical reactions during high-temperature treatments, preserving their mechanical and chemical properties.
-
Applications in Heat Treatment:
- Bright Annealing: Argon is used to prevent oxidation and discoloration of metals during annealing, ensuring a bright, clean surface.
- Quenching: It provides a controlled atmosphere to cool metals rapidly without introducing impurities or causing surface reactions.
- Aging of Alloys: Argon is employed in the aging process of materials like titanium and nickel-based alloys to maintain their structural integrity and performance.
- High-Strength Stainless Steels: It is used in heat treatment processes to prevent contamination and ensure consistent material properties.
-
Role in Aerospace and High-Performance Alloys:
- In the aerospace industry, argon is critical for heat-treating components made from titanium, zirconium, and other high-performance alloys. These materials are prone to gas absorption and reactivity, making argon's inertness essential for maintaining their strength and durability.
-
Use in PVD Processes:
- Argon is also utilized in physical vapor deposition (PVD) to create a pure vapor phase of coating materials. Its inert nature ensures that the coating material remains uncontaminated before deposition on the substrate, resulting in high-quality, durable coatings.
-
Cost Considerations:
- While argon is effective, its high cost can be a limiting factor. However, the benefits of preventing oxidation, contamination, and ensuring material purity often outweigh the expense, especially in critical applications like aerospace and advanced manufacturing.
-
Advantages Over Other Gases:
- Compared to other inert gases like helium, argon is more cost-effective and readily available, making it a preferred choice for many heat treatment applications. Its density also provides better coverage and protection in certain processes.
By understanding these key points, it becomes clear why argon is a preferred choice in heat treatment processes, despite its cost. Its ability to create a stable, non-reactive environment ensures the quality and performance of treated materials, making it indispensable in industries where precision and reliability are paramount.
Summary Table:
Key Aspect | Details |
---|---|
Inert Nature | Prevents chemical reactions, oxidation, and contamination during treatment. |
Applications | Bright annealing, quenching, aging of alloys, and PVD processes. |
Industries | Aerospace, high-performance alloys, and advanced manufacturing. |
Advantages | Ensures material purity, stability, and performance. |
Cost Considerations | High cost justified by critical benefits in precision applications. |
Interested in optimizing your heat treatment processes with argon? Contact our experts today to learn more!