A vacuum environment is essential for the deposition of thin films to ensure high-quality, pure, and adherent coatings. The primary reasons for using a vacuum include reducing the density of gas molecules, which allows vaporized atoms to travel longer distances without collisions (long mean-free path), and minimizing contamination from unwanted substances like oxygen, nitrogen, and carbon dioxide. These contaminants can interfere with the deposition process, weaken film adhesion, or introduce impurities. Additionally, a vacuum enables precise control over gas and vapor composition, facilitates a low-pressure plasma environment, and ensures efficient mass flow control, all of which are critical for achieving uniform and high-performance thin films.
Key Points Explained:
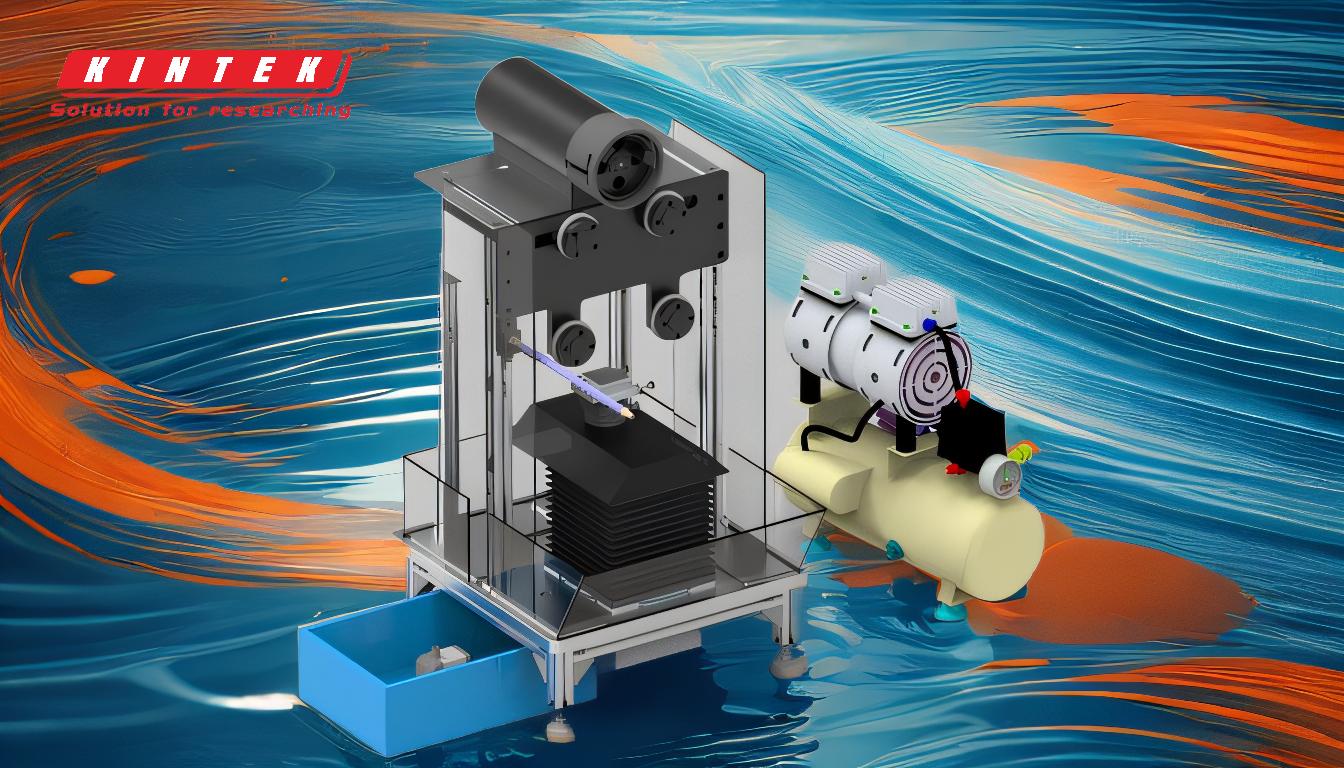
-
Long Mean-Free Path for Vaporized Atoms:
- In a vacuum, the gas pressure is significantly reduced, which decreases the density of gas molecules in the chamber.
- This reduction allows vaporized atoms or molecules to travel longer distances without colliding with other particles, ensuring they reach the substrate uniformly.
- Without a vacuum, frequent collisions would cause the atoms to scatter, leading to uneven deposition and potential nucleation of particles in the vapor, forming soot or other defects.
-
Minimization of Contamination:
- A vacuum environment reduces the presence of unwanted substances such as oxygen, nitrogen, carbon dioxide, and water vapor.
- These contaminants can react with the film material, leading to impurities, oxidation, or other chemical reactions that degrade the film's quality.
- By maintaining a high vacuum, the purity of the deposited film is preserved, ensuring strong adhesion and desired material properties.
-
Control Over Gas and Vapor Composition:
- In a vacuum, the composition of gases and vapors in the chamber can be precisely controlled.
- This control is crucial for processes like sputtering or chemical vapor deposition (CVD), where specific gases are introduced to facilitate the deposition process.
- A vacuum ensures that only the desired gases are present, eliminating interference from atmospheric gases.
-
Low-Pressure Plasma Environment:
- Many thin film deposition techniques, such as plasma-enhanced chemical vapor deposition (PECVD), require a low-pressure plasma environment.
- A vacuum enables the creation of this plasma, which is essential for activating chemical reactions or ionizing gases to deposit films at lower temperatures.
- The absence of atmospheric gases ensures stable plasma formation and efficient deposition.
-
Efficient Mass Flow Control:
- A vacuum allows for precise control of the flow of gases and vapors into the processing chamber.
- This control is critical for achieving uniform film thickness and composition across the substrate.
- Without a vacuum, uncontrolled gas flow could lead to inconsistent deposition and poor film quality.
-
High Thermal Evaporation Rate:
- In physical vapor deposition (PVD) techniques like thermal evaporation, a vacuum is necessary to achieve high evaporation rates.
- The reduced pressure prevents heat loss and ensures that the material evaporates efficiently, depositing evenly on the substrate.
- Atmospheric pressure would hinder evaporation and lead to incomplete or uneven film formation.
-
Prevention of Film Oxidation and Other Reactions:
- Many materials used in thin film deposition are highly reactive with oxygen or moisture in the air.
- A vacuum eliminates these reactive gases, preventing oxidation or other undesirable chemical reactions during deposition.
- This is particularly important for metals and semiconductors, where even trace amounts of oxygen can alter electrical or optical properties.
-
Enhanced Film Adhesion and Purity:
- By reducing contamination and ensuring uniform deposition, a vacuum environment enhances the adhesion of the film to the substrate.
- Strong adhesion is critical for the durability and performance of the thin film in applications such as electronics, optics, and coatings.
- High purity ensures that the film exhibits the desired mechanical, electrical, or optical properties without interference from impurities.
In summary, the use of a vacuum in thin film deposition is indispensable for achieving high-quality, uniform, and pure films. It addresses key challenges such as contamination control, particle scattering, and precise process management, making it a fundamental requirement in modern deposition techniques.
Summary Table:
Key Benefit | Explanation |
---|---|
Long Mean-Free Path for Vaporized Atoms | Reduces gas density, allowing atoms to travel longer distances without collisions. |
Minimization of Contamination | Eliminates unwanted substances like oxygen, nitrogen, and carbon dioxide. |
Control Over Gas and Vapor Composition | Enables precise control of gases for processes like sputtering or CVD. |
Low-Pressure Plasma Environment | Facilitates stable plasma formation for techniques like PECVD. |
Efficient Mass Flow Control | Ensures uniform film thickness and composition across the substrate. |
High Thermal Evaporation Rate | Achieves efficient evaporation for PVD techniques like thermal evaporation. |
Prevention of Film Oxidation | Eliminates reactive gases, preventing oxidation or undesirable chemical reactions. |
Enhanced Film Adhesion and Purity | Ensures strong adhesion and high purity for durable, high-performance films. |
Learn how a vacuum environment can optimize your thin film deposition process—contact our experts today!