Vacuum heat treatment is a critical process in modern manufacturing, particularly for industries requiring high precision and quality. The use of a vacuum cleaning furnace ensures a clean, controlled environment that eliminates oxidation, decarburization, and contamination. This results in superior mechanical properties, consistent repeatability, and high-quality components. The vacuum environment allows for precise temperature control, uniform heating, and rapid cooling, making it ideal for processes like annealing, brazing, sintering, and hardening. Additionally, vacuum heat treatment improves surface quality by preventing oxidation and removing impurities, ensuring bright, clean, and transmutation-free surfaces.
Key Points Explained:
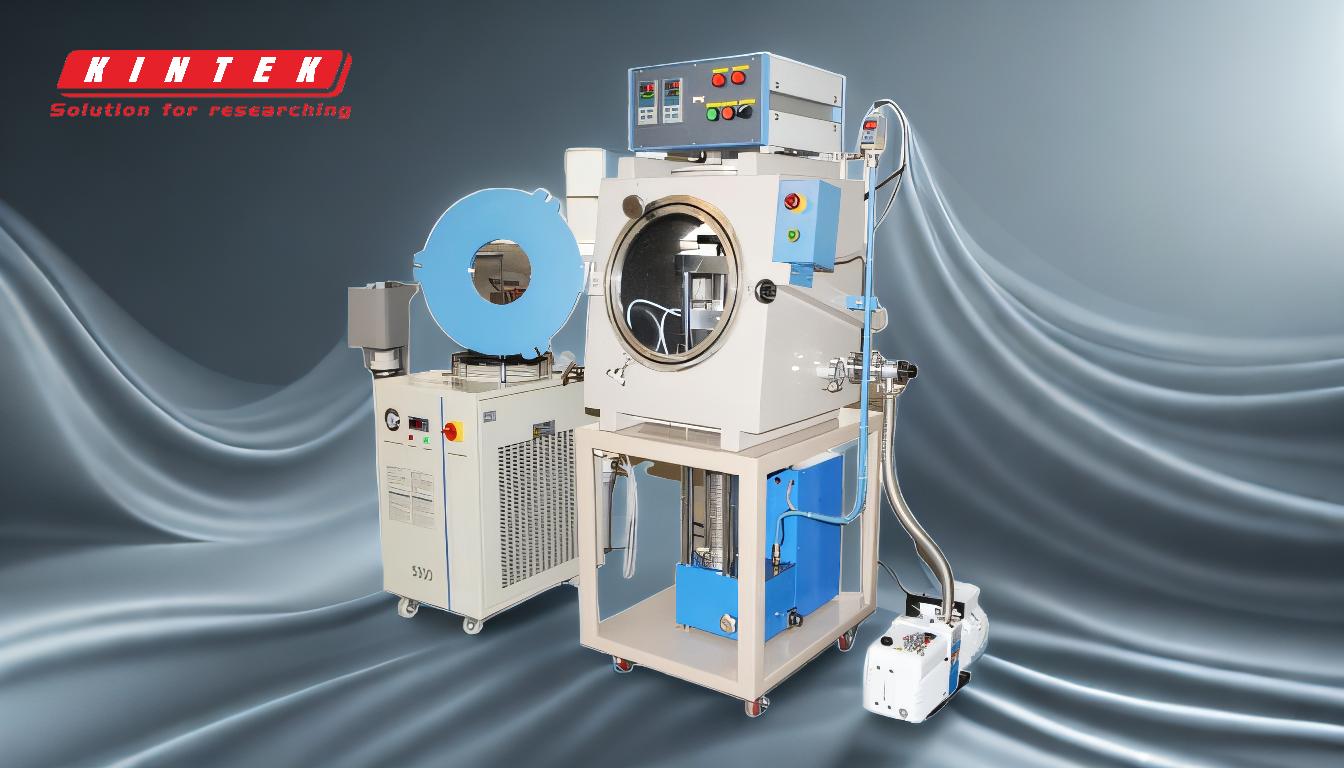
-
Elimination of Contamination and Oxidation
- A vacuum furnace creates an environment free from reactive gases like oxygen and carbon, which can cause oxidation, decarburization, and contamination.
- This ensures the production of ultra-clean components with no surface impurities, resulting in improved mechanical properties such as hardness, strength, and wear resistance.
- The absence of reactive gases also prevents surface defects like carburization and decarburization, preserving the dimensional stability of the treated materials.
-
Precise Temperature Control and Uniform Heating
- Vacuum furnaces provide excellent temperature uniformity and stability, with precise control within a small area.
- This allows for consistent and repeatable results, which are critical for industries with stringent quality assurance standards.
- The ability to maintain uniform temperatures in the range of 1100–1500°C (2000–2800°F) ensures that components meet specified performance criteria with each treatment cycle.
-
Improved Surface Quality
- Vacuum heat treatment prevents oxidation and removes impurities like phosphorus chips from the surface of workpieces.
- It also has degreasing and degassing effects, resulting in a bright, purified, and transmutation-free surface.
- This is particularly beneficial for applications requiring high surface quality, such as aerospace, medical devices, and precision engineering.
-
Versatility in Heat Treatment Processes
- Vacuum furnaces support a wide range of heat treatment processes, including annealing, brazing, sintering, tempering, and hardening.
- This versatility makes them suitable for various industries, from automotive to electronics, where different materials and components require specific treatments.
- The ability to computer-control the process ensures metallurgical repeatability, further enhancing the reliability of the treatment.
-
Energy Efficiency and Advanced Control Systems
- Vacuum furnaces are designed with advanced insulation materials and control systems that minimize heat loss and optimize energy consumption.
- This not only reduces operational costs but also aligns with sustainability goals by lowering energy usage.
- The integration of computer-controlled systems ensures precise monitoring and adjustment of parameters, enhancing overall process efficiency.
-
Quick Cooling (Quenching) Capabilities
- Vacuum furnaces enable rapid cooling of products, which is essential for processes like quenching.
- This quick cooling helps achieve the desired material properties, such as increased hardness and strength, without compromising the quality of the treated components.
- The controlled quenching process also minimizes the risk of thermal distortion or cracking.
-
Repeatability and Consistency
- The controlled environment of a vacuum furnace ensures repeatable results, which is critical for industries requiring high precision and reliability.
- Each treatment cycle produces components with consistent mechanical properties, meeting stringent quality assurance standards.
- This predictability is especially important for industries like aerospace, automotive, and medical devices, where component performance is non-negotiable.
By leveraging the advantages of vacuum heat treatment, manufacturers can achieve superior product quality, enhanced mechanical properties, and consistent performance, making it an indispensable process in modern industrial applications.
Summary Table:
Key Benefits | Details |
---|---|
Contamination-Free Environment | Eliminates oxidation, decarburization, and surface impurities. |
Precise Temperature Control | Uniform heating and stability within 1100–1500°C (2000–2800°F). |
Improved Surface Quality | Prevents oxidation, removes impurities, and ensures bright, clean surfaces. |
Versatility | Supports annealing, brazing, sintering, tempering, and hardening. |
Energy Efficiency | Advanced insulation and control systems reduce energy consumption. |
Quick Cooling (Quenching) | Rapid cooling ensures desired material properties without defects. |
Repeatability & Consistency | Ensures consistent results for high-precision industries. |
Unlock the benefits of vacuum heat treatment for your manufacturing process—contact our experts today!