A controlled atmosphere box furnace is used for heat treating because it provides a tightly sealed environment with precise temperature and atmospheric control, which is essential for achieving desired material properties. This type of furnace prevents oxidation, decarburization, and contamination, ensuring consistent and high-quality outcomes. It is particularly useful for processes like annealing, brazing, carburizing, and sintering, where maintaining a specific atmosphere (inert or reactive) is critical. Additionally, controlled atmosphere furnaces offer advantages such as energy efficiency, reduced operating costs, and improved production throughput, making them a preferred choice for industrial and laboratory applications.
Key Points Explained:
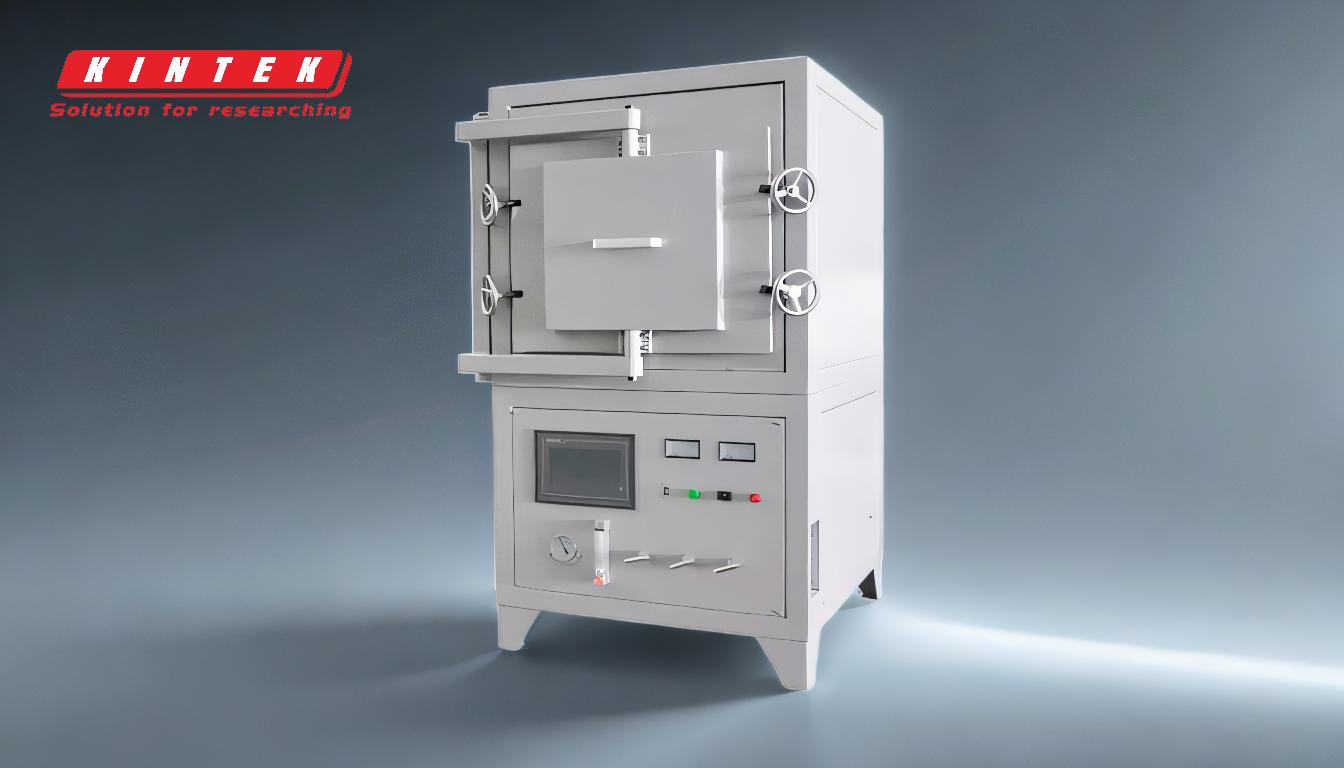
-
Precise Temperature and Atmospheric Control:
- A controlled atmosphere furnace allows for exact temperature regulation and the maintenance of a specific atmosphere (inert or reactive). This is crucial for heat treatment processes where even minor deviations can affect the material's properties.
- The tightly sealed environment ensures that the material is protected from external contaminants, which could otherwise lead to defects or inconsistencies.
-
Prevention of Oxidation and Decarburization:
- During heat treatment, materials are often exposed to high temperatures, which can cause oxidation (reaction with oxygen) or decarburization (loss of carbon from the surface). A controlled atmosphere furnace minimizes these reactions by replacing the ambient air with a protective gas, such as nitrogen or argon.
- This is particularly important for processes like annealing and tempering, where surface integrity is critical.
-
Support for Reactive Atmospheres:
- In some heat treatment processes, a reactive atmosphere is required to achieve specific material properties. For example, carburizing involves introducing a carbon-rich atmosphere to increase the surface hardness of steel.
- The controlled environment ensures that these reactions occur uniformly and predictably, leading to consistent results.
-
Versatility in Heat Treatment Processes:
- Controlled atmosphere furnaces are used for a wide range of heat treatment processes, including:
- Annealing: Softening materials to improve machinability or reduce internal stresses.
- Brazing: Joining metals using a filler material.
- Carburizing: Increasing surface hardness by adding carbon.
- Sintering: Bonding powdered materials to form solid components.
- Each of these processes benefits from the precise control over temperature and atmosphere provided by the furnace.
- Controlled atmosphere furnaces are used for a wide range of heat treatment processes, including:
-
Improved Product Quality and Consistency:
- By maintaining a controlled environment, these furnaces ensure that every batch of material undergoes the same conditions, leading to consistent results. This is particularly important in industrial applications where uniformity is critical.
- The ability to prevent contamination and surface reactions also contributes to the overall quality of the finished product.
-
Energy Efficiency and Cost Savings:
- Controlled atmosphere furnaces are designed to be energy-efficient, reducing operating costs over time. Features like thermal homogeneity and accurate controls minimize energy waste.
- The reduced need for manual labor and the ability to process parts of all shapes and sizes further enhance their cost-effectiveness.
-
Safety and Performance:
- These furnaces are equipped with advanced safety devices to prevent accidents, such as gas leaks or overheating. This ensures a safe working environment for operators.
- The high performance and low energy consumption of controlled atmosphere furnaces make them a reliable choice for both laboratory and industrial settings.
In summary, a controlled atmosphere box furnace is indispensable for heat treating because it provides the precise conditions needed to achieve specific material properties, ensures consistency and quality, and offers significant operational advantages. Its ability to create protective or reactive atmospheres makes it a versatile tool for a wide range of heat treatment processes.
Summary Table:
Key Benefits | Details |
---|---|
Precise Temperature Control | Ensures exact regulation for consistent material properties. |
Oxidation & Decarburization Prevention | Protects materials from surface damage using inert gases like nitrogen. |
Versatile Heat Treatment Processes | Supports annealing, brazing, carburizing, and sintering. |
Improved Product Quality & Consistency | Maintains uniform conditions for high-quality outcomes. |
Energy Efficiency & Cost Savings | Reduces operating costs and energy waste. |
Safety & Performance | Advanced safety features ensure reliable operation. |
Ready to enhance your heat treatment processes? Contact us today to learn more about controlled atmosphere box furnaces!