Atomic Layer Deposition (ALD) is often considered superior to Chemical Vapor Deposition (CVD) for specific applications, particularly when high precision, uniformity, and conformality are required. ALD separates individual chemical reactions, allowing for atomic-level control over film thickness and composition. This makes it ideal for depositing ultra-thin films (10-50 nm) and coating high-aspect ratio structures with exceptional uniformity. In contrast, CVD is better suited for thicker films and higher deposition rates, making it more efficient for bulk material deposition. ALD's self-limiting nature ensures high reproducibility and low-temperature processing, which are critical for advanced applications in semiconductors, nanotechnology, and other high-precision industries.
Key Points Explained:
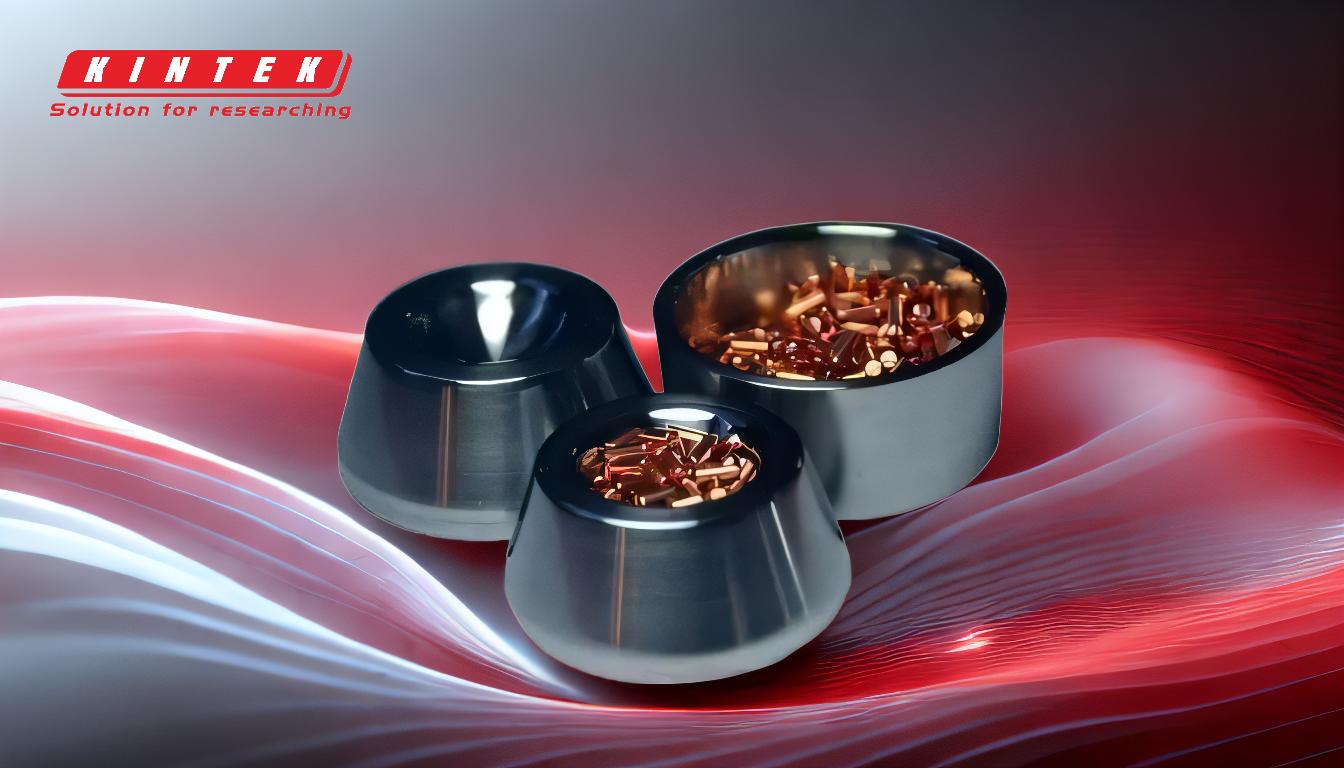
-
Precision and Control in Film Thickness
- ALD separates individual chemical reactions, enabling atomic-level control over film thickness. This precision is critical for applications requiring ultra-thin films (10-50 nm).
- CVD, while faster, lacks the same level of control, making it less suitable for applications where exact thickness is crucial.
-
Uniformity and Conformality
- ALD excels in producing highly uniform and conformal films, even on complex geometries and high-aspect ratio structures. This is due to its self-limiting nature, where each reaction cycle deposits a single atomic layer.
- CVD, although capable of conformal coatings, struggles to match ALD's uniformity, especially on intricate or high-aspect ratio surfaces.
-
Low-Temperature Processing
- ALD can operate at lower temperatures compared to CVD, making it compatible with temperature-sensitive substrates and materials.
- CVD often requires higher temperatures, which can limit its use in certain applications, such as flexible electronics or organic materials.
-
Reproducibility and Film Quality
- ALD's self-limiting and self-assembled nature ensures high reproducibility and consistent film quality, which is critical for advanced manufacturing processes.
- CVD, while versatile, may produce films with varying quality due to its reliance on continuous chemical reactions.
-
Applications in High-Precision Industries
- ALD is widely used in semiconductor manufacturing, nanotechnology, and other industries where ultra-thin, uniform films are essential.
- CVD is better suited for applications requiring thicker films and faster deposition rates, such as protective coatings or bulk material synthesis.
-
Flexibility with Substrates
- ALD can deposit films onto curved and complex substrates with ease, thanks to its excellent step coverage and conformality.
- CVD, while versatile, may struggle with non-planar or highly irregular surfaces.
In summary, ALD's superior precision, uniformity, and low-temperature processing make it the preferred choice for applications requiring ultra-thin, high-quality films and complex geometries. CVD, on the other hand, is better suited for thicker films and higher throughput applications. The choice between ALD and CVD ultimately depends on the specific requirements of the application, including film thickness, deposition rate, and substrate compatibility.
Summary Table:
Feature | ALD (Atomic Layer Deposition) | CVD (Chemical Vapor Deposition) |
---|---|---|
Film Thickness | Ultra-thin (10-50 nm) | Thicker films |
Precision | Atomic-level control | Less precise |
Uniformity | Highly uniform | Less uniform |
Conformality | Excellent on complex surfaces | Good, but less consistent |
Temperature | Low-temperature processing | Higher temperatures required |
Reproducibility | High | Variable |
Applications | Semiconductors, Nanotechnology | Protective coatings, Bulk materials |
Need help choosing between ALD and CVD for your project? Contact our experts today for tailored solutions!