Ceramic sintering is a critical process in the manufacturing of ceramic materials, used to transform powdered ceramics into dense, strong, and durable objects. This process is particularly valuable for materials with extremely high melting points, as it allows consolidation without reaching the melting temperature. Sintering reduces porosity, enhances mechanical strength, and improves thermal and electrical properties, making it indispensable in industries such as construction, electronics, and tool manufacturing. The process involves high temperatures and sometimes additional forces like pressure or electrical currents, enabling the creation of advanced ceramics with tailored properties for specific applications.
Key Points Explained:
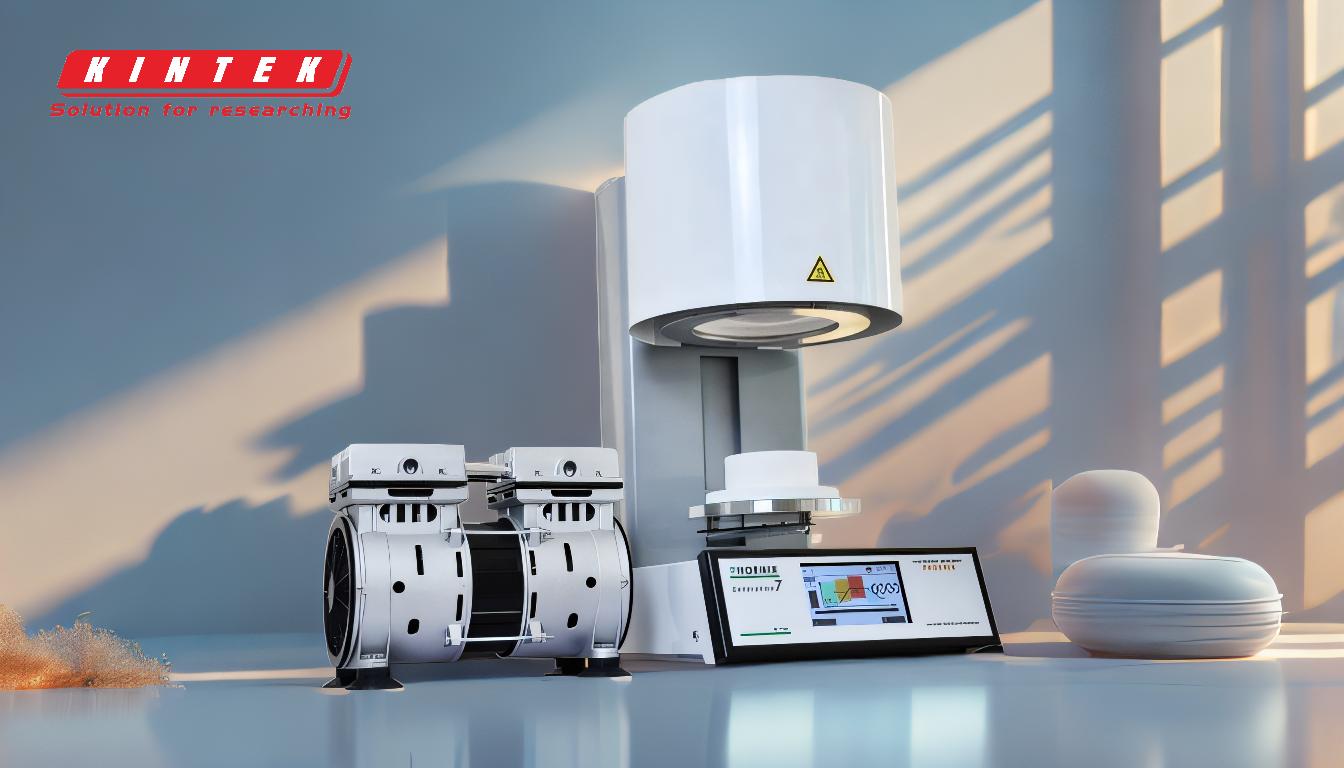
-
Consolidation Without Melting
- Sintering is ideal for materials with extremely high melting points, such as Alumina, Boron Carbide, and Tungsten.
- The process consolidates ceramic powders at temperatures below their melting points, making it energy-efficient and practical for these materials.
- This avoids the challenges of handling molten ceramics, which can be highly reactive or difficult to shape.
-
Reduction of Porosity and Shrinkage
- During sintering, the glass phases within the ceramic powder flow, filling voids and reducing porosity.
- This consolidation leads to shrinkage, resulting in a denser and more uniform microstructure.
- Reduced porosity enhances the material's mechanical strength, hardness, and resistance to wear and corrosion.
-
Improved Mechanical and Thermal Properties
- Sintered ceramics exhibit superior mechanical strength, hardness, and thermal stability compared to unsintered materials.
- These properties make sintered ceramics suitable for demanding applications, such as cutting tools, refractory materials, and electrical insulators.
- The process also improves thermal conductivity and resistance to thermal shock, which are critical for high-temperature applications.
-
Versatility in Applications
- Sintering is used to produce a wide range of ceramic products, including tiles, sanitaryware, pottery, and advanced ceramics for industrial use.
- It is also employed in powder metallurgy and 3D printing to create custom metal and ceramic shapes with precise geometries.
- The ability to tailor the sintering process allows for the production of materials with specific properties, such as porosity, density, and electrical conductivity.
-
Energy Efficiency and Cost-Effectiveness
- Sintering is more energy-efficient than melting, especially for high-melting-point materials, as it operates at lower temperatures.
- The process reduces material waste by consolidating powders into near-net-shape components, minimizing the need for additional machining.
- This makes sintering a cost-effective method for producing high-performance ceramics and metals.
-
Role in Advanced Ceramics
- Sintering is the most critical step in preparing advanced ceramics, as it transforms raw ceramic powders into polycrystalline materials with tailored properties.
- The process involves diffusion and mass transfer, resulting in a uniform microstructure and stable shape.
- Advanced ceramics produced through sintering are used in cutting-edge applications, such as aerospace components, biomedical implants, and electronic devices.
-
Enhanced Surface Properties
- Sintering decreases surface porosity, improving the material's resistance to wear, corrosion, and environmental degradation.
- This is particularly important for components exposed to harsh conditions, such as industrial machinery or medical devices.
- The improved surface properties also enhance the material's aesthetic appeal, making it suitable for decorative applications.
By leveraging the sintering process, manufacturers can produce ceramics with exceptional properties, tailored to meet the demands of specific applications. This makes sintering a cornerstone of modern materials science and industrial manufacturing.
Summary Table:
Key Benefits of Ceramic Sintering | Details |
---|---|
Consolidation Without Melting | Ideal for high-melting-point materials like Alumina and Tungsten. Energy-efficient and avoids handling molten ceramics. |
Reduction of Porosity | Reduces voids, enhances mechanical strength, and improves wear and corrosion resistance. |
Improved Mechanical & Thermal Properties | Superior strength, hardness, and thermal stability for demanding applications. |
Versatility in Applications | Used in tiles, advanced ceramics, powder metallurgy, and 3D printing. |
Energy Efficiency | Operates at lower temperatures, reducing energy consumption and material waste. |
Advanced Ceramics Production | Critical for aerospace, biomedical, and electronic applications. |
Enhanced Surface Properties | Improves wear resistance, corrosion resistance, and aesthetic appeal. |
Unlock the potential of ceramic sintering for your projects—contact our experts today to learn more!