CVD (Chemical Vapor Deposition) is often preferred over PVD (Physical Vapor Deposition) due to its superior ability to produce uniform coatings on complex geometries, higher deposition rates, and cost-effectiveness. CVD allows for multidirectional deposition, enabling coatings to reach deep holes and shaded areas, which PVD cannot achieve due to its line-of-sight limitation. Additionally, CVD coatings exhibit high purity, fine-grained structures, and hardness, making them suitable for demanding applications. While CVD requires higher temperatures and specialized precursor materials, its ability to minimize waste and provide versatile, high-quality coatings makes it a preferred choice for many industrial applications.
Key Points Explained:
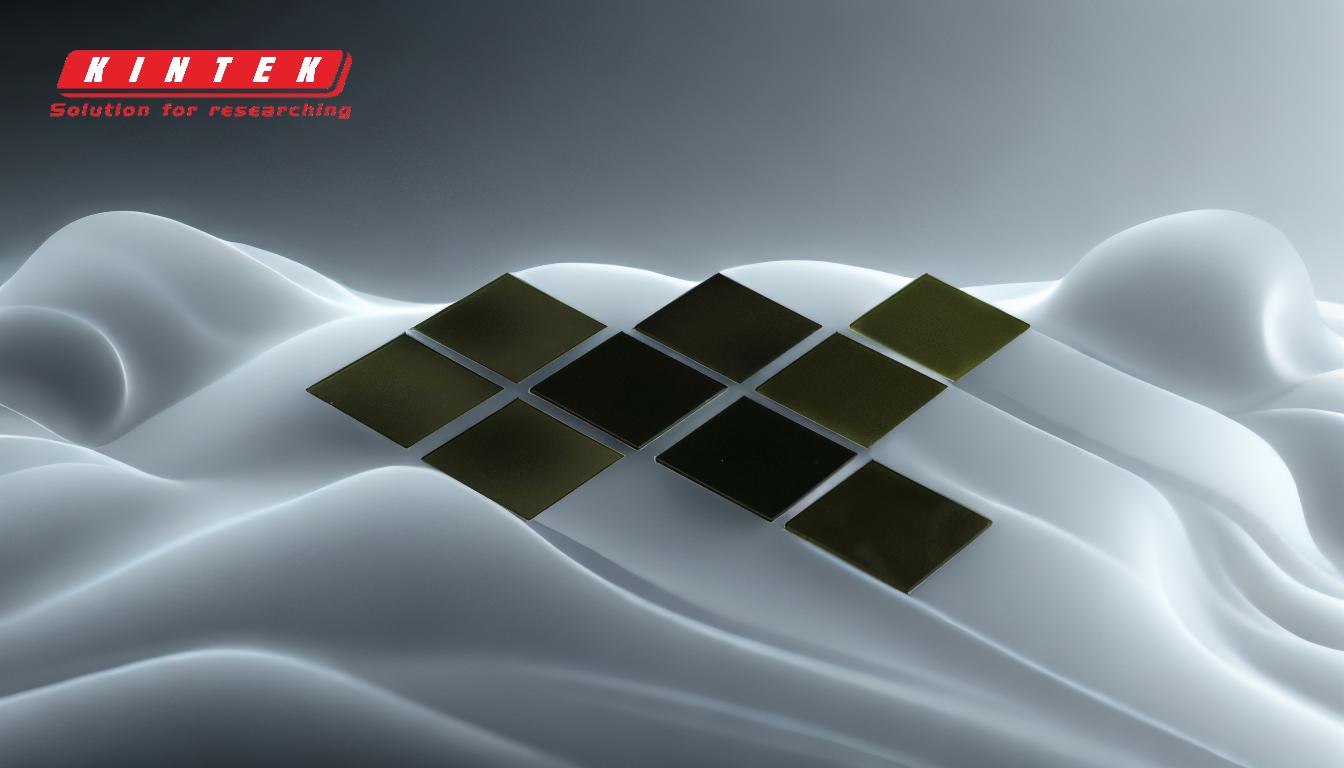
-
Uniform Coating on Complex Geometries:
- CVD is a conformal deposition process, meaning it can evenly coat substrates regardless of their shape. This is particularly advantageous for complex geometries, such as deep holes or shaded areas, where PVD's line-of-sight deposition fails.
- Example: CVD is ideal for coating intricate components in the aerospace or medical device industries, where uniformity is critical.
-
High Purity and Fine-Grained Coatings:
- CVD produces coatings with high purity and fine-grained structures, which are harder and more durable than those produced by traditional methods.
- This makes CVD suitable for applications requiring high-performance materials, such as semiconductor manufacturing or wear-resistant coatings.
-
Cost-Effectiveness:
- CVD systems are generally more cost-efficient than PVD systems, offering an economical solution for surface coating requirements.
- The ability to minimize material waste and achieve high deposition rates further enhances its cost-effectiveness.
-
Versatility in Coating Materials:
- CVD can deposit coatings from elements that are difficult to evaporate but are available as volatile chemical compounds.
- This versatility allows CVD to be used in a wide range of applications, from creating thin films for electronics to producing protective coatings for industrial tools.
-
High Deposition Rates and Controlled Thickness:
- CVD offers high deposition rates, and the thickness of the coatings can be precisely controlled by adjusting temperature and duration.
- This makes CVD suitable for applications requiring specific coating thicknesses, such as optical coatings or barrier layers.
-
Atmospheric Pressure Operation:
- Unlike PVD, CVD can be performed at atmospheric pressure, simplifying the process and reducing equipment complexity.
- This feature is particularly beneficial for large-scale industrial applications.
-
Less Waste Deposition:
- CVD minimizes material waste by selectively coating only the heated areas of the substrate.
- Advanced techniques, such as computer-controlled lasers, can further enhance this capability by precisely targeting specific areas for coating.
-
Challenges and Limitations:
- CVD requires higher temperatures (400-1000°C) and specialized precursor materials, making it unsuitable for temperature-sensitive substrates.
- PVD is preferred in such cases, as it operates at lower temperatures and does not require chemical precursors.
In summary, CVD is preferred over PVD for its ability to produce uniform, high-quality coatings on complex geometries, its cost-effectiveness, and its versatility in material deposition. However, the choice between CVD and PVD ultimately depends on the specific requirements of the application, including substrate material, temperature sensitivity, and desired coating properties.
Summary Table:
Feature | CVD | PVD |
---|---|---|
Coating Uniformity | Conformal, suitable for complex geometries | Line-of-sight, limited for deep holes/shaded areas |
Coating Quality | High purity, fine-grained, and hard | Less uniform, lower purity |
Cost-Effectiveness | Economical, minimizes waste, high deposition rates | Higher costs, lower deposition rates |
Versatility | Deposits a wide range of materials | Limited to materials that can be evaporated |
Deposition Rate | High, with precise thickness control | Lower, less precise |
Operating Pressure | Can operate at atmospheric pressure | Requires vacuum conditions |
Temperature Requirements | Higher temperatures (400-1000°C) | Lower temperatures |
Applications | Aerospace, medical devices, semiconductors, wear-resistant coatings | Temperature-sensitive substrates, simpler geometries |
Ready to explore how CVD can enhance your industrial applications? Contact our experts today for tailored solutions!