Flux plays a critical role in the brazing process, primarily by ensuring the formation of strong and reliable joints. It achieves this by removing oxides from the surfaces of the materials being joined, which allows the braze alloy to wet the surfaces effectively. Additionally, flux prevents the formation of new oxides during the heating process, promotes wetting, and ensures the filler metal flows smoothly over the base metal. In furnace brazing, the atmosphere often replaces the need for flux, but in other brazing methods, flux remains indispensable for achieving high-quality joints.
Key Points Explained:
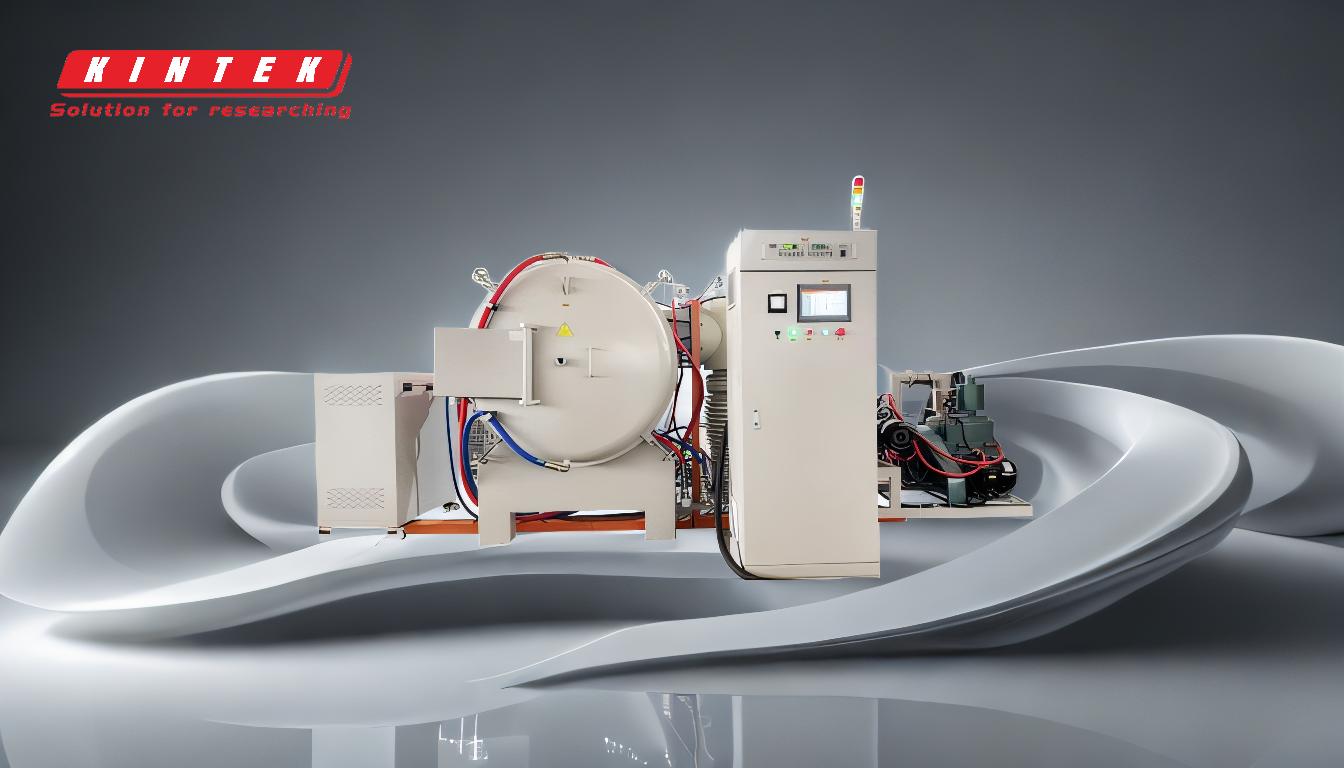
-
Oxide Removal:
- Flux is essential for dissolving and removing oxide layers from the surfaces of the materials being joined. Oxides can form on metal surfaces due to exposure to air, and these oxides prevent the filler metal from wetting the base metal effectively.
- Without flux, the oxide layer acts as a barrier, reducing the strength and integrity of the brazed joint. By dissolving these oxides, flux ensures that the filler metal can bond directly to the base metal, creating a strong and durable joint.
-
Promoting Wetting:
- Wetting refers to the ability of the filler metal to spread evenly over the surface of the base metal. Flux promotes wetting by ensuring that the surfaces are clean and free from contaminants.
- When the flux melts before the filler metal, it wets all surfaces, allowing the filler metal to flow smoothly and uniformly. This capillary action ensures that the filler metal fills all the gaps between the surfaces, forming a solid and continuous joint.
-
Preventing Oxide Formation:
- During the brazing process, the high temperatures can cause new oxides to form on the metal surfaces. Flux acts as a protective barrier, preventing the formation of these oxides.
- By maintaining a clean surface, flux ensures that the filler metal can flow freely and bond effectively with the base metal, resulting in a high-quality joint.
-
Cleaning the Surface:
- Flux not only removes existing oxides but also cleans the surface of any other contaminants, such as dirt, grease, or oil. A clean surface is crucial for achieving a strong and reliable brazed joint.
- The cleaning action of flux ensures that the filler metal can adhere properly to the base metal, enhancing the overall strength and durability of the joint.
-
Facilitating Filler Metal Flow:
- Flux plays a key role in ensuring that the filler metal flows smoothly over the base metal. By reducing surface tension and promoting wetting, flux allows the filler metal to spread evenly and fill all the necessary gaps.
- This uniform flow of the filler metal is essential for creating a strong and continuous joint, free from voids or weak spots.
-
Post-Brazing Residue:
- After the brazing process, the flux often remains as a fine, adhesive layer on the surface. While this residue can sometimes be removed, it generally does not affect the integrity of the joint.
- In some cases, the residue can provide additional protection against corrosion, further enhancing the durability of the brazed joint.
In summary, flux is indispensable in the brazing process for its ability to remove oxides, promote wetting, prevent oxide formation, clean surfaces, and facilitate the smooth flow of filler metal. These functions collectively ensure the creation of strong, reliable, and durable brazed joints.
Summary Table:
Function of Flux | Description |
---|---|
Oxide Removal | Dissolves and removes oxide layers, enabling strong bonding of filler metal. |
Promoting Wetting | Ensures clean surfaces for smooth and uniform filler metal flow. |
Preventing Oxide Formation | Acts as a barrier to prevent new oxides during heating. |
Cleaning the Surface | Removes contaminants like dirt, grease, and oil for better adhesion. |
Facilitating Filler Flow | Reduces surface tension, allowing filler metal to spread evenly. |
Post-Brazing Residue | Protects against corrosion, enhancing joint durability. |
Learn how flux can improve your brazing results—contact our experts today!