Press forging is a preferred method for large forging due to its efficiency, cost-effectiveness, and ability to produce high-quality components with superior mechanical properties. The process involves compressing the grain structure, which enhances the strength of the final piece by aligning the grain flow. This alignment reduces stress concentrations in critical areas like corners and fillets, minimizing the risk of metallurgical defects such as porosity and alloy segregation. Additionally, press forging improves the piece's response to heat treatment and reduces machining time, making it a practical choice for large-scale industrial applications.
Key Points Explained:
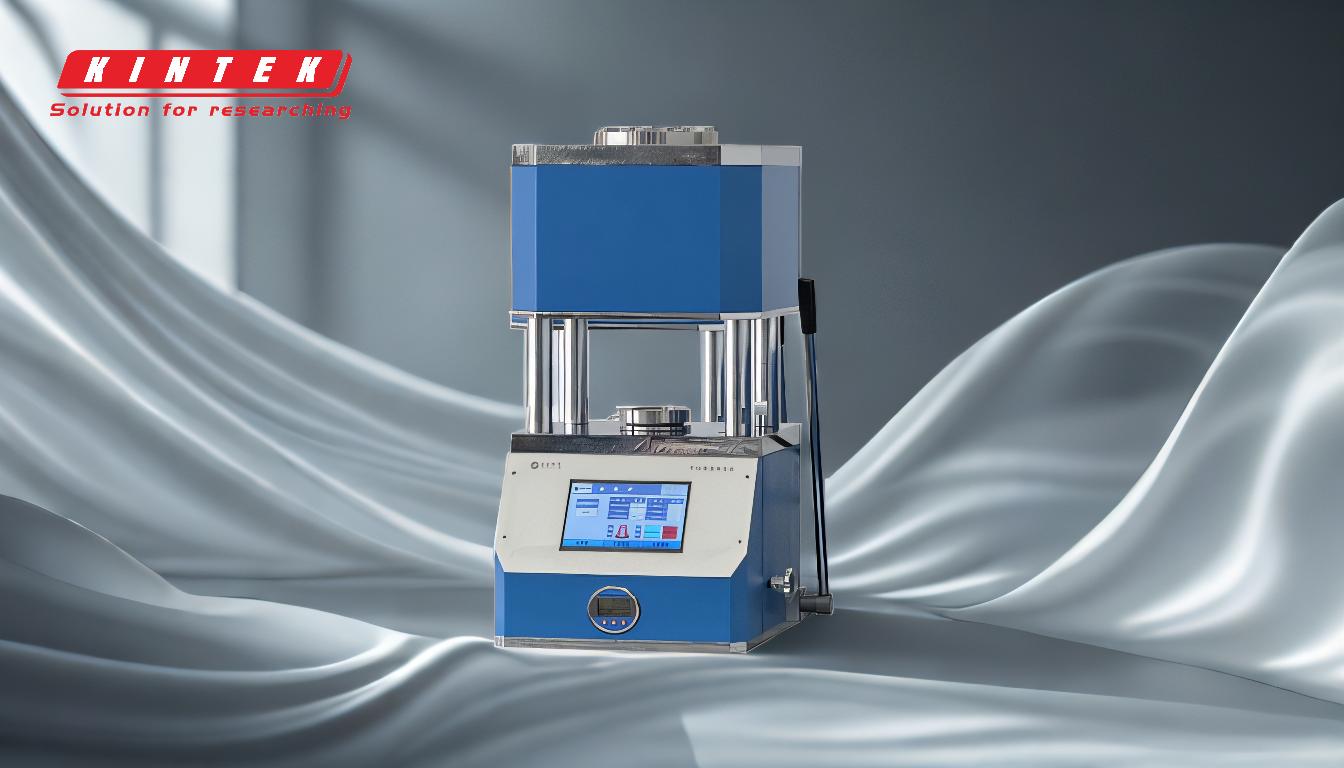
-
Efficiency and Cost-Effectiveness:
- Press forging is quicker and less expensive compared to other forging techniques. This makes it particularly suitable for large-scale production where time and cost are critical factors. The process allows for high-volume manufacturing without compromising on quality.
-
Enhanced Grain Flow and Strength:
- The process compresses the grain structure, aligning it in a way that enhances the mechanical properties of the forged piece. This alignment of grain flow significantly increases the strength and durability of the final product, making it ideal for applications requiring high structural integrity.
-
Reduction of Stress Concentrations:
- Press forging reduces stress on corners and fillets, which are typically areas prone to stress concentrations. By minimizing these stress points, the process enhances the overall reliability and lifespan of the forged components.
-
Minimization of Metallurgical Defects:
- The process minimizes defects such as porosity and alloy segregation. These defects can compromise the quality and performance of the forged piece. By reducing these issues, press forging ensures a higher quality product with better mechanical properties.
-
Improved Response to Heat Treatment:
- Components produced through press forging respond better to heat treatment. This is crucial for applications where specific mechanical properties are required. The improved response to heat treatment ensures that the final product meets the desired specifications and performance standards.
-
Reduction in Machining Time:
- Press forging reduces the need for extensive machining, as the process produces components with closer tolerances and better surface finishes. This not only saves time but also reduces material waste, making the process more efficient and cost-effective.
-
Industrial Applications:
- Press forging is widely used in various industrial applications, including the production of coins, silver articles, and automatic forging. Its versatility and ability to produce high-quality components make it a preferred choice in industries where precision and durability are paramount.
In summary, press forging is used for large forging due to its efficiency, cost-effectiveness, and ability to produce high-quality components with superior mechanical properties. The process enhances grain flow, reduces stress concentrations, minimizes metallurgical defects, improves heat treatment response, and reduces machining time, making it an ideal choice for large-scale industrial applications.
Summary Table:
Key Benefits of Press Forging | Details |
---|---|
Efficiency & Cost-Effectiveness | Quicker and less expensive, ideal for large-scale production. |
Enhanced Grain Flow & Strength | Aligns grain structure for increased strength and durability. |
Reduced Stress Concentrations | Minimizes stress in critical areas like corners and fillets. |
Minimized Metallurgical Defects | Reduces porosity and alloy segregation for higher quality components. |
Improved Heat Treatment Response | Ensures better mechanical properties post-treatment. |
Reduced Machining Time | Produces components with closer tolerances, saving time and material waste. |
Wide Industrial Applications | Used in coin production, silver articles, and automatic forging. |
Interested in leveraging press forging for your industrial needs? Contact us today to learn more!