Physical Vapor Deposition (PVD) is a widely used technique for depositing thin films of material onto a substrate. The process is typically conducted in a vacuum environment for several critical reasons. A vacuum reduces the density of atoms in the chamber, which increases the mean free path of the atoms, allowing them to travel longer distances without collisions. This environment also minimizes gaseous contamination, ensuring high-quality, pure films. Additionally, a vacuum facilitates high thermal evaporation rates and prevents unwanted chemical reactions between the material and atmospheric gases, which could compromise the film's properties. The controlled vacuum environment is essential for applications like microchip manufacturing, where even minor contamination can lead to significant defects.
Key Points Explained:
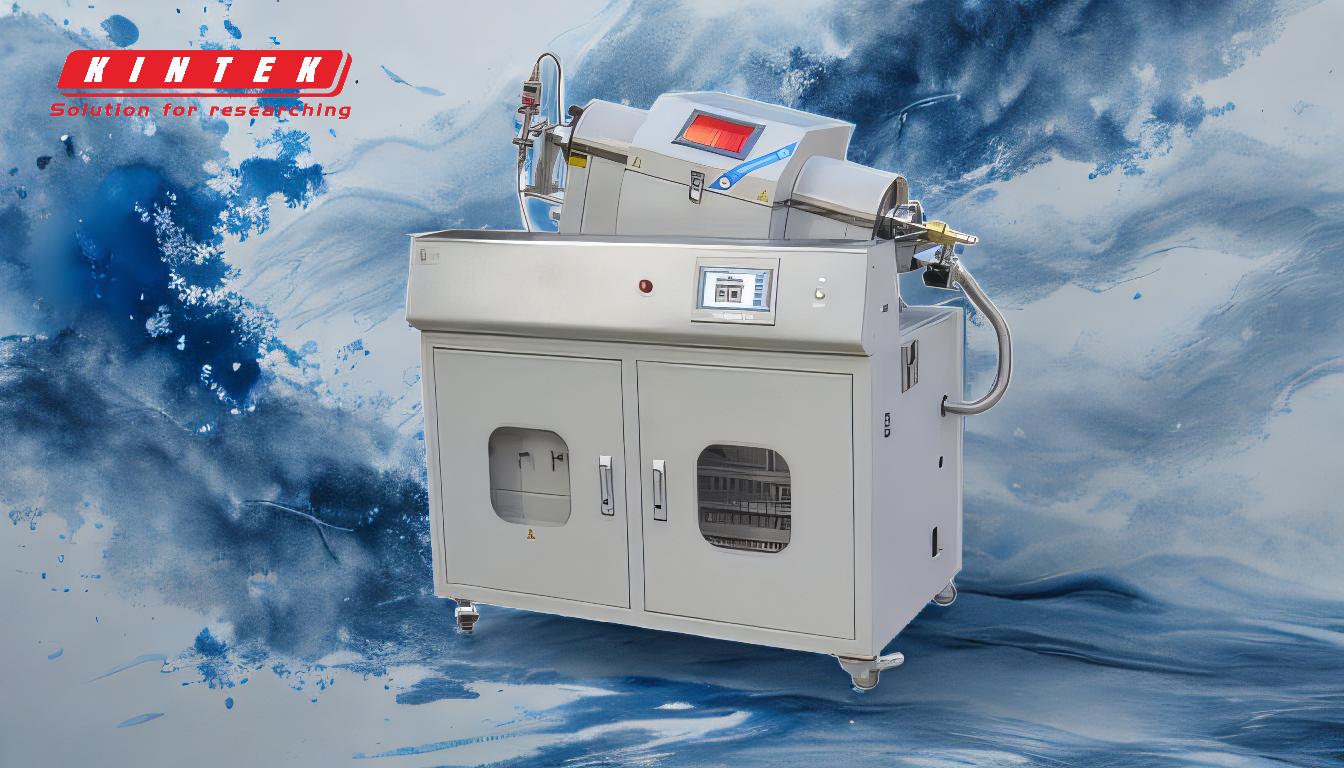
-
Increased Mean Free Path of Atoms:
- In a vacuum, the density of atoms is significantly reduced, which increases the mean free path—the average distance an atom can travel before colliding with another atom or molecule. This is crucial in PVD because it allows the vaporized material to travel unimpeded from the source to the substrate, ensuring uniform deposition and high-quality thin films.
-
Minimization of Gaseous Contamination:
- A vacuum environment drastically reduces the presence of undesirable atoms and molecules, such as oxygen, moisture, and other reactive gases. These contaminants can react with the vaporized material, altering its properties or creating defects in the deposited film. By maintaining a high vacuum, PVD ensures a clean and controlled environment, which is particularly important for applications like microchip manufacturing, where even trace contaminants can cause significant issues.
-
High Thermal Evaporation Rate:
- The vacuum environment facilitates a high thermal evaporation rate by reducing the pressure within the chamber. This allows the material to vaporize at lower temperatures, which is beneficial for depositing materials with high melting points. The absence of air or other gases also ensures that the vaporized material reaches the substrate with minimal energy loss, resulting in a more efficient and effective deposition process.
-
Prevention of Unwanted Chemical Reactions:
- In a vacuum, the reactive elements present in air, such as oxygen, carbon dioxide, and hydrogen, are removed. This prevents unwanted chemical reactions between the vaporized material and these elements, which could otherwise alter the surface properties of the deposited film. For example, reactions with oxygen could lead to the formation of oxides, which might be undesirable in certain applications.
-
Controlled and Repeatable Deposition Process:
- A vacuum provides a controlled environment that is essential for achieving consistent and repeatable results in PVD. By maintaining a specific vacuum level, the process parameters can be precisely controlled, ensuring that the same conditions are replicated in each deposition cycle. This is critical for industrial applications where consistency and reliability are paramount.
-
Enhanced Adhesion and Film Quality:
- The absence of air or other fluids in a vacuum ensures that the vaporized material reaches the substrate with more energy, leading to better adhesion and a more uniform film. This is particularly important for applications requiring strong, durable coatings, such as in the production of CDs, DVDs, and other optical media.
-
Flexibility in Coating Types:
- While PVD is typically used to deposit metals and alloys without chemical reactions, the vacuum environment also allows for the introduction of reactive gases if desired. For example, oxygen can be introduced to create oxide coatings, providing flexibility in the types of coatings that can be produced using PVD.
In summary, performing PVD in a vacuum is essential for achieving high-quality, contamination-free thin films with precise control over the deposition process. The vacuum environment not only enhances the efficiency and effectiveness of the process but also ensures that the final product meets the stringent requirements of various industrial applications. For more information on related processes, you can explore microwave plasma chemical vapor deposition.
Summary Table:
Key Reason | Explanation |
---|---|
Increased Mean Free Path | Allows atoms to travel unimpeded, ensuring uniform deposition and high-quality films. |
Minimization of Gaseous Contamination | Reduces reactive gases like oxygen and moisture, preventing defects in the film. |
High Thermal Evaporation Rate | Enables vaporization at lower temperatures, improving efficiency and effectiveness. |
Prevention of Chemical Reactions | Eliminates unwanted reactions with atmospheric gases, preserving film properties. |
Controlled and Repeatable Process | Ensures consistent results by maintaining specific vacuum levels. |
Enhanced Adhesion and Film Quality | Improves energy transfer, leading to better adhesion and uniform coatings. |
Flexibility in Coating Types | Allows introduction of reactive gases for diverse coating options. |
Learn more about how PVD in a vacuum can enhance your processes—contact our experts today!