Sintering is a critical process in manufacturing, particularly for ceramics and metals, as it transforms powdered materials into dense, durable, and functional components. It enables the production of intricate shapes, enhances mechanical properties like strength and hardness, and improves thermal and electrical conductivity. Sintering also allows for cost-effective mass production, precise control over material composition, and the ability to work with high-melting-point materials without requiring a liquid phase. This process is essential for creating components with tailored properties, reducing porosity, and ensuring repeatability in manufacturing.
Key Points Explained:
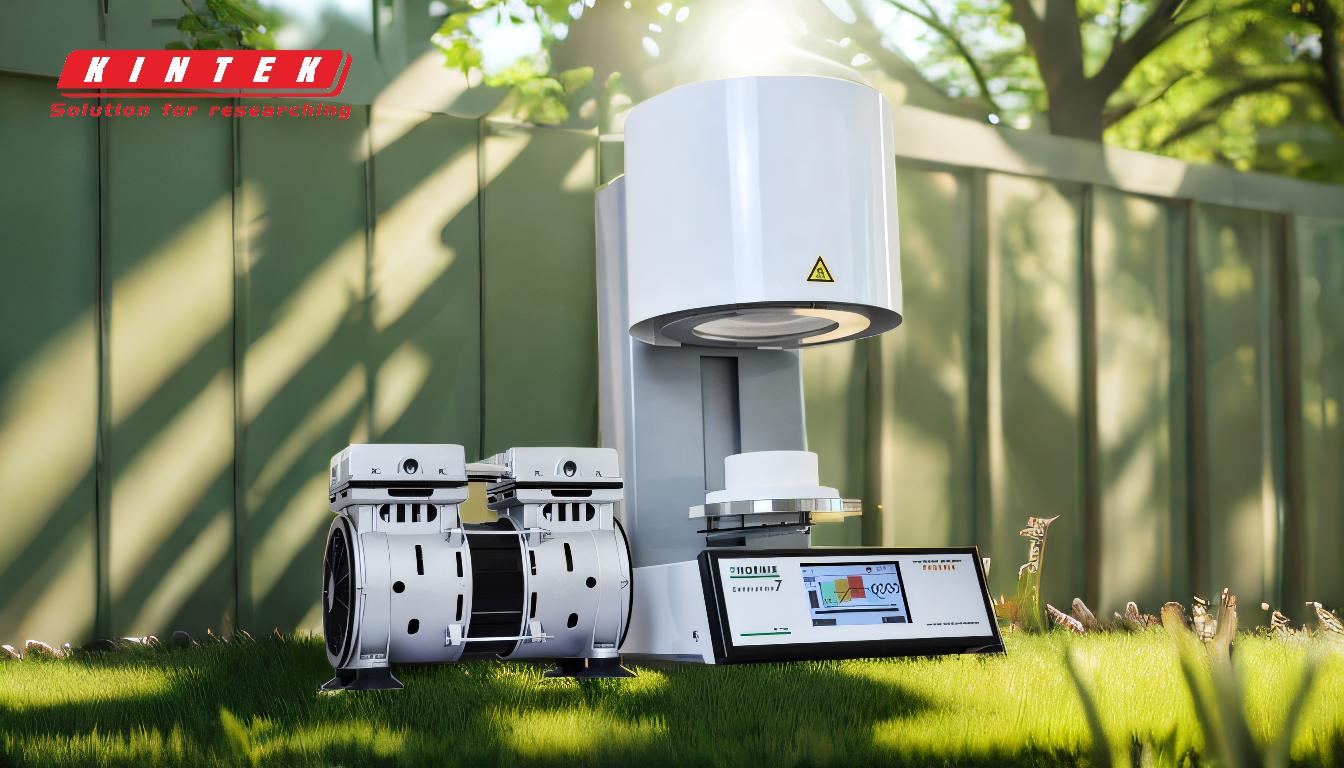
-
Production of Fully Dense Parts
- Sintering compacts powdered materials into dense components, eliminating porosity and enhancing structural integrity.
- Fully dense parts exhibit improved mechanical properties, such as strength, durability, and wear resistance, which are critical for demanding applications in industries like aerospace, automotive, and medical devices.
-
Enhanced Mechanical Properties
- The sintering process improves hardness, toughness, and abrasion resistance by bonding particles at high temperatures.
- This results in components that can withstand harsh environments and mechanical stress, making them suitable for high-performance applications.
-
Creation of Complex Shapes and Intricate Designs
- Sintering allows for the production of intricate geometries that are difficult or impossible to achieve with traditional manufacturing methods like casting or forging.
- This capability is particularly valuable for industries requiring precision components, such as electronics and medical implants.
-
Cost-Effectiveness and Mass Production
- Sintering reduces tooling costs and enables rapid, repeatable production of complex parts.
- It is a scalable process, making it ideal for high-volume manufacturing while maintaining precision and consistency.
-
Tailored Material Compositions
- Sintering allows for the combination of multiple materials, enabling the creation of components with customized properties, such as toughness paired with abrasion resistance.
- This flexibility is crucial for developing advanced materials with specific performance requirements.
-
Versatility in Material Selection
- Sintering can be used with a wide range of materials, including ceramics, metals, and composites.
- It is particularly advantageous for working with high-melting-point materials, as it does not require melting, thus avoiding decomposition or distortion.
-
Improved Functional Properties
- Sintering enhances properties like electrical conductivity, thermal conductivity, and translucency, making it suitable for applications in electronics, energy, and optics.
- These improvements are achieved by reducing porosity and creating a uniform microstructure.
-
Flexibility Compared to Traditional Methods
- Unlike casting or forging, sintering does not involve solid-liquid phase changes, which reduces the risk of defects and allows for greater design freedom.
- This makes sintering a more adaptable and reliable manufacturing technique for complex and high-performance components.
-
Key Role in Powder Metallurgy
- Sintering is the final step in powder metallurgy, where pressed billets are transformed into components with the desired physical and mechanical properties.
- It is essential for achieving the final product's performance characteristics, such as density, strength, and dimensional accuracy.
In summary, sintering is indispensable in modern manufacturing due to its ability to produce high-quality, complex, and durable components efficiently and cost-effectively. Its versatility and precision make it a cornerstone of industries requiring advanced materials and intricate designs.
Summary Table:
Key Benefit | Description |
---|---|
Fully Dense Parts | Eliminates porosity, improving strength and durability. |
Enhanced Mechanical Properties | Increases hardness, toughness, and abrasion resistance. |
Complex Shapes | Enables intricate designs for precision industries like electronics and medical. |
Cost-Effective Mass Production | Reduces tooling costs and supports high-volume manufacturing. |
Tailored Material Compositions | Combines materials for customized properties like toughness and conductivity. |
Versatility in Materials | Works with ceramics, metals, and high-melting-point materials. |
Improved Functional Properties | Enhances electrical, thermal conductivity, and translucency. |
Flexibility Over Traditional Methods | Avoids defects and offers greater design freedom. |
Key Role in Powder Metallurgy | Final step to achieve density, strength, and dimensional accuracy. |
Ready to optimize your manufacturing process with sintering? Contact our experts today!