Sintering is a critical step in ceramic processing because it transforms ceramic powder into a fully dense, strong, and durable material with specific mechanical and physical properties. By subjecting the green body to high temperatures, sintering reduces porosity, increases density, and enhances strength, resulting in a material that meets the desired performance requirements. This process is essential for creating intricate shapes, combining material properties, and enabling cost-effective mass production. Additionally, sintering ensures the formation of a uniform microstructure, which is vital for achieving precision, hardness, and toughness in advanced ceramics. Overall, sintering is indispensable for producing high-quality ceramic components with consistent and reliable properties.
Key Points Explained:
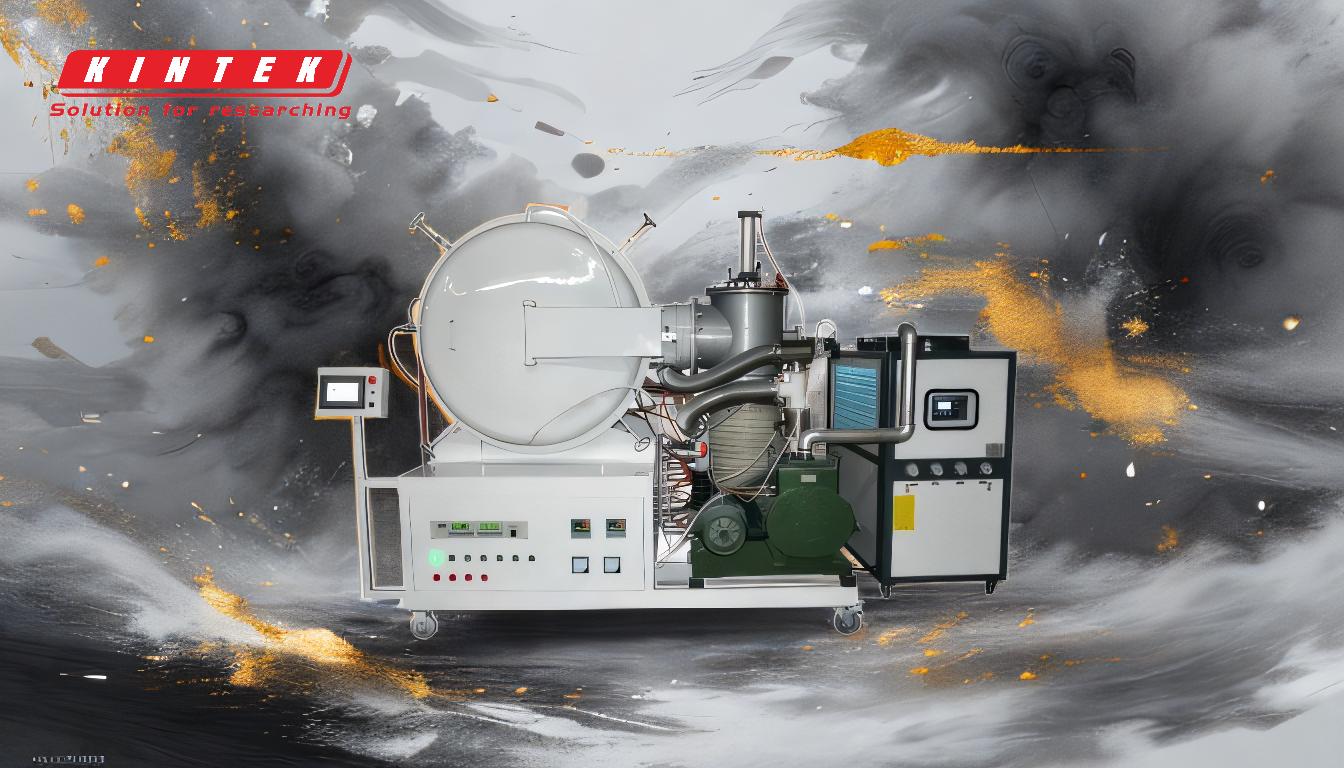
-
Transformation of Ceramic Powder into Dense Material
- Sintering converts ceramic powder into polycrystalline ceramic materials with specific properties.
- This process involves diffusion and mass transfer, leading to densification and the formation of a uniform microstructure.
- The result is a stable shape and excellent mechanical properties, such as hardness and toughness, which are essential for advanced ceramic applications.
-
Reduction of Porosity and Increase in Density
- During sintering, the green body is fired at high temperatures, causing particles to bond and reducing porosity.
- This densification process enhances the material's strength and durability, making it suitable for demanding applications.
- A fully dense part exhibits the desired material properties, such as resistance to wear and abrasion.
-
Achievement of Desired Physical and Mechanical Properties
- Sintering ensures that the final ceramic product meets specific performance requirements, such as strength, toughness, and precision.
- The process optimizes the microstructure, resulting in consistent and reliable properties across multiple production batches.
- This is particularly important for advanced ceramics used in industries like aerospace, electronics, and medical devices.
-
Creation of Intricate Shapes and Geometries
- Sintering enables the production of complex shapes and geometries that are difficult to achieve with traditional manufacturing methods.
- This capability is crucial for applications requiring precision and intricate designs, such as microelectronic components or biomedical implants.
- The process also allows for lower-cost tooling, making it economically viable for mass production.
-
Combination of Material Properties
- Sintering can merge the properties of multiple materials, such as combining toughness with abrasion resistance.
- This versatility allows for the creation of customized ceramic composites tailored to specific applications.
- For example, sintering can produce materials that are both lightweight and highly durable, ideal for automotive or aerospace components.
-
Cost-Effective Mass Production
- Sintering enables rapid mass production while maintaining precision and repeatability.
- The process is scalable and can produce large quantities of ceramic components with consistent quality.
- This efficiency reduces manufacturing costs and makes sintering an attractive option for industrial applications.
-
Role in Advanced Ceramics
- Sintering is the most important step in preparing advanced ceramics, as it determines the final material properties.
- The process ensures the formation of a uniform microstructure, which is critical for achieving high-performance ceramics.
- Advanced ceramics produced through sintering are used in cutting-edge technologies, such as semiconductors, energy storage systems, and high-temperature applications.
-
Comparison to Other Manufacturing Processes
- Unlike traditional methods, sintering allows for the production of complex parts with minimal material waste.
- The process is more energy-efficient and environmentally friendly compared to machining or casting.
- Sintering also offers greater flexibility in material selection and property customization.
By understanding the importance of sintering in ceramic processing, manufacturers can optimize the process to produce high-quality components that meet the demands of modern industries. This step-by-step approach ensures that every aspect of the sintering process is carefully controlled, resulting in materials with superior performance and reliability.
Summary Table:
Key Benefit | Description |
---|---|
Dense Material Formation | Converts ceramic powder into polycrystalline materials with uniform microstructure. |
Porosity Reduction | High temperatures bond particles, reducing porosity and increasing density. |
Enhanced Mechanical Properties | Achieves strength, toughness, and precision for advanced applications. |
Complex Shape Creation | Enables intricate designs for microelectronics and biomedical implants. |
Custom Material Properties | Combines properties like toughness and abrasion resistance for tailored solutions. |
Cost-Effective Mass Production | Scalable process for consistent, high-quality ceramic components. |
Advanced Ceramics | Essential for semiconductors, energy storage, and high-temperature applications. |
Eco-Friendly Manufacturing | Minimal waste, energy-efficient, and flexible material customization. |
Ready to optimize your ceramic processing? Contact our experts today to learn more about sintering solutions!