Sintering is a critical process in ceramic manufacturing, primarily used to enhance the material's density, strength, and durability while reducing porosity. By heating ceramic powders or green bodies at high temperatures below their melting point in a sintering furnace, sintering facilitates atomic diffusion, leading to particle bonding and grain growth. This results in a denser, stronger, and more durable ceramic product. The process also optimizes material properties by reducing voids and improving microstructure uniformity. Advanced techniques like spark plasma sintering further enhance performance by enabling rapid heating and minimizing defects, making sintering indispensable for producing high-quality ceramics.
Key Points Explained:
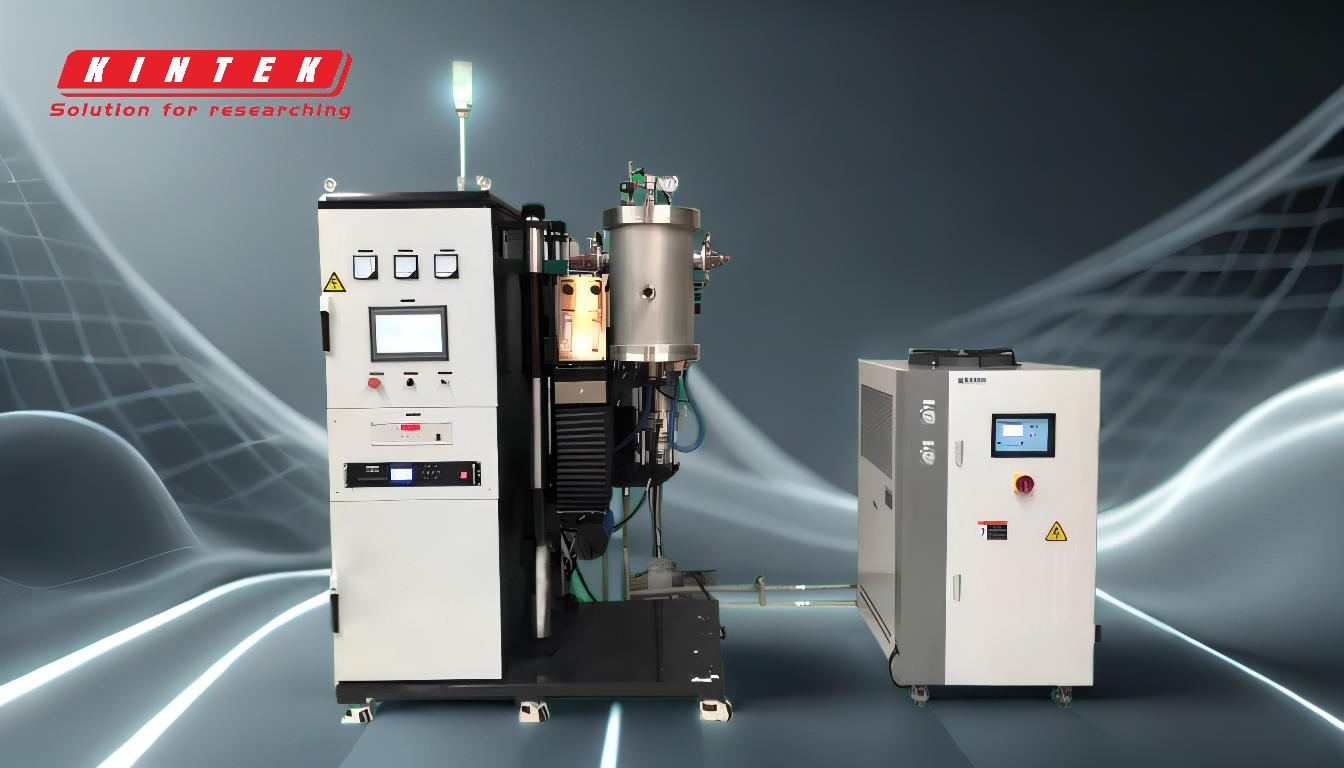
-
Purpose of Sintering in Ceramics:
- Sintering is used to consolidate ceramic powders or green bodies into a dense, strong, and durable final product. It reduces porosity and increases material density, which are crucial for enhancing mechanical properties like strength and hardness.
-
Process Mechanism:
- The process involves heating ceramic materials in a sintering furnace at temperatures below their melting point. This allows atoms to diffuse across particle boundaries, leading to bonding and grain growth. The result is a polycrystalline structure with fewer voids and improved material integrity.
-
Driving Forces in Sintering:
- Sintering is driven by factors such as the reduction of surface free energy, chemical potential gradients, phase transitions, and external forces (mechanical, electric, magnetic, or ultrasonic). These forces promote material transfer, grain orientation, and densification.
-
Benefits of Sintering:
- Increased density and strength: Sintering compacts ceramic particles, resulting in a stronger and harder material.
- Reduced porosity: The process minimizes voids, enhancing the material's structural integrity.
- Improved microstructure: Sintering leads to uniform grain growth and a well-defined polycrystalline structure.
-
Advanced Sintering Techniques:
- Techniques like spark plasma sintering (SPS) enable rapid heating and densification in a short time. This method is particularly effective for producing ceramics with uniform pores, no defects, and optimized piezoelectric properties.
-
Applications of Sintered Ceramics:
- Sintered ceramics are used in various industries, including electronics, aerospace, and biomedical engineering, due to their enhanced mechanical and thermal properties.
-
Importance of Sintering Furnaces:
- The sintering furnace plays a crucial role in controlling temperature and atmosphere during the process, ensuring consistent and high-quality results.
By understanding these key points, a purchaser can appreciate the importance of sintering in ceramic manufacturing and make informed decisions when selecting equipment or materials for their specific needs.
Summary Table:
Aspect | Details |
---|---|
Purpose | Consolidates ceramic powders, reduces porosity, and enhances density. |
Process Mechanism | Heating below melting point enables atomic diffusion and grain growth. |
Driving Forces | Surface energy reduction, chemical gradients, and external forces. |
Benefits | Increased strength, reduced porosity, and improved microstructure. |
Advanced Techniques | Spark plasma sintering for rapid heating and defect-free ceramics. |
Applications | Used in electronics, aerospace, and biomedical engineering. |
Role of Furnaces | Ensures precise temperature control for consistent, high-quality results. |
Ready to optimize your ceramic manufacturing process? Contact us today to learn more about sintering solutions!