Temperature plays a pivotal role in casting processes, influencing the quality, consistency, and characteristics of the final product. Precise temperature control is essential to ensure that the casting material flows properly, solidifies uniformly, and achieves the desired mechanical and structural properties. Inconsistent or improper temperatures can lead to defects such as cracks, voids, or incomplete filling of molds, which compromise the integrity and performance of the cast product. Additionally, maintaining accurate temperature control ensures repeatability in production, allowing manufacturers to reproduce high-quality results consistently across multiple batches. This is particularly important in industries where safety, reliability, and precision are paramount.
Key Points Explained:
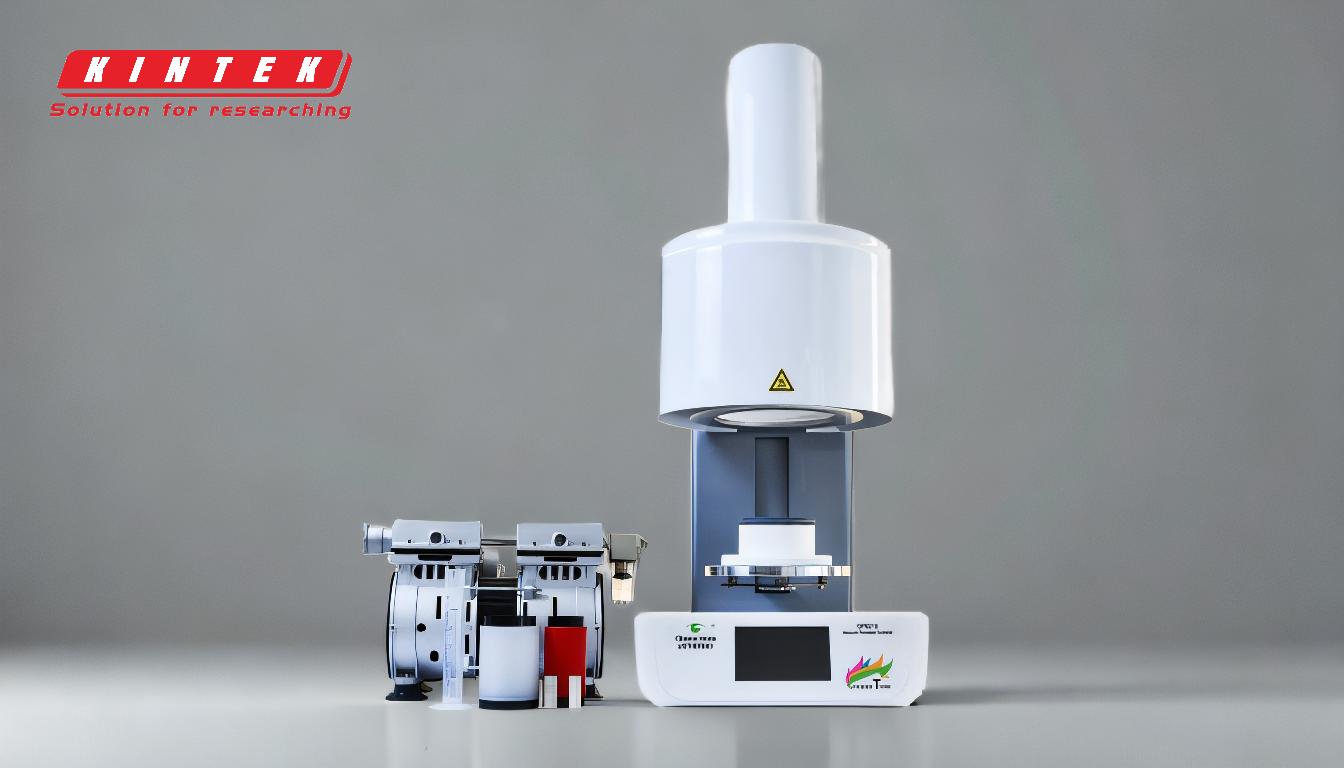
-
Flow and Filling of Casting Material:
- Temperature directly affects the viscosity and fluidity of the casting material (e.g., molten metal or resin). If the temperature is too low, the material may not flow properly, leading to incomplete filling of the mold and defects like cold shuts or misruns. Conversely, if the temperature is too high, it can cause excessive turbulence during pouring, leading to gas entrapment or oxidation.
- Precise temperature control ensures that the material maintains optimal flow characteristics, allowing it to fill the mold completely and uniformly.
-
Solidification and Cooling Rates:
- The rate at which the casting material solidifies is influenced by temperature. Rapid cooling can result in internal stresses, cracks, or brittleness, while slow cooling can lead to coarse grain structures, reducing the material's strength and durability.
- Controlling the temperature during the cooling phase ensures a balanced solidification process, minimizing defects and enhancing the mechanical properties of the final product.
-
Microstructure and Mechanical Properties:
- Temperature affects the microstructure of the cast material, which in turn determines its mechanical properties such as strength, hardness, and ductility. For example, in metal casting, the cooling rate influences grain size and phase formation, which are critical for achieving the desired material characteristics.
- By maintaining precise temperature control, manufacturers can tailor the microstructure to meet specific performance requirements.
-
Consistency and Repeatability:
- Consistent temperature control is essential for producing uniform results across multiple batches. Variations in temperature can lead to inconsistencies in product quality, making it difficult to replicate successful outcomes.
- Achieving repeatability is particularly important in industries such as aerospace, automotive, and medical device manufacturing, where even minor deviations can have significant consequences.
-
Defect Prevention:
- Inaccurate temperature control can lead to a range of casting defects, including porosity, shrinkage, and thermal stresses. These defects not only compromise the structural integrity of the product but also increase waste and production costs.
- Precise temperature management helps mitigate these issues, ensuring a defect-free final product.
-
Energy Efficiency and Cost Savings:
- Proper temperature control can optimize energy usage during the casting process. Overheating or excessive cooling requires additional energy, increasing operational costs.
- By maintaining optimal temperatures, manufacturers can reduce energy consumption and improve overall process efficiency.
-
Safety and Process Control:
- Temperature control is critical for ensuring the safety of the casting process. In exothermic reactions, such as those occurring in metal casting, excessive heat can lead to dangerous situations, including explosions or equipment damage.
- Accurate temperature management ensures that the process remains within safe operating limits, protecting both personnel and equipment.
In summary, temperature is a fundamental factor in casting that influences every stage of the process, from material flow and solidification to final product quality. Precise temperature control is essential for achieving consistent, high-quality results, minimizing defects, and ensuring the safety and efficiency of the casting process. By understanding and managing temperature effectively, manufacturers can optimize their production processes and deliver reliable, high-performance cast products.
Summary Table:
Key Aspect | Impact of Temperature |
---|---|
Flow and Filling | Ensures proper material flow, preventing defects like cold shuts or gas entrapment. |
Solidification and Cooling | Balances cooling rates to minimize cracks, stresses, and brittleness. |
Microstructure and Properties | Influences grain size and phase formation for desired mechanical properties. |
Consistency and Repeatability | Maintains uniform results across batches, critical for industries like aerospace. |
Defect Prevention | Reduces defects like porosity, shrinkage, and thermal stresses. |
Energy Efficiency | Optimizes energy use, reducing operational costs. |
Safety and Process Control | Ensures safe operating conditions, protecting personnel and equipment. |
Ready to optimize your casting process? Contact our experts today for tailored solutions!