Refractory materials are essential in furnaces due to their ability to withstand extreme temperatures, provide thermal insulation, and protect the furnace structure from physical, thermal, and chemical stresses. They act as a barrier between molten materials and the furnace's induction system, ensuring energy efficiency and safety. These materials, often composed of lightweight alumina ceramic fibers and insulation boards, minimize heat loss and energy consumption while maintaining structural integrity under high heat and pressure. Their multi-layer insulation design further enhances performance, making them indispensable in industrial furnace operations.
Key Points Explained:
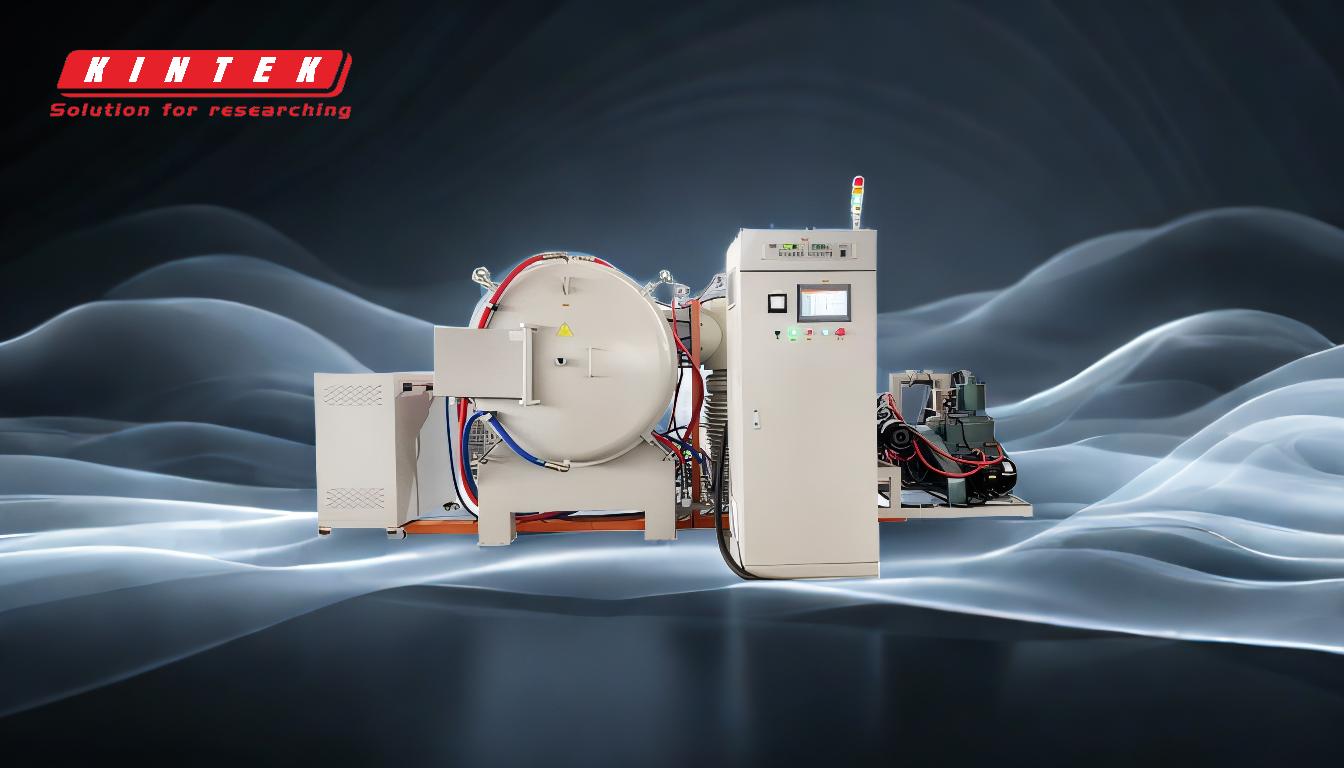
-
High-Temperature Resistance
- Refractory materials are designed to withstand extreme temperatures without decomposing or losing structural integrity.
- This property is critical in furnaces, where temperatures often exceed 1000°C, ensuring the furnace lining remains intact and functional.
-
Thermal Insulation
- Refractory materials, such as lightweight alumina ceramic fibers and high-quality insulation boards, have low thermal conductivity.
- This minimizes heat loss, improving energy efficiency and reducing operational costs.
- The multi-layer insulation design further enhances thermal insulation, maintaining consistent internal temperatures.
-
Protection Against Physical, Thermal, and Chemical Stresses
- Refractory linings act as a barrier between molten materials (ferrous and non-ferrous metals) and the furnace's induction system.
- They protect the furnace coil and other components from intense physical wear, thermal shocks, and chemical reactions.
- This ensures the longevity and reliability of the furnace structure.
-
Energy Efficiency and Low Heat Loss
- The use of refractory materials reduces heat dissipation, leading to lower energy consumption.
- Materials like alumina ceramic fibers are lightweight and free from asbestos, making them environmentally friendly and efficient.
-
Structural Integrity Under High Heat and Pressure
- Refractory bricks and linings maintain their shape and strength even under high heat and pressure.
- This is crucial for large-scale kiln and furnace operations, where structural failure could lead to catastrophic consequences.
-
Multi-Layer Insulation Design
- The combination of lightweight alumina ceramic fibers and insulation boards creates a robust, multi-layered system.
- This design ensures optimal performance, durability, and safety in high-temperature environments.
-
Environmental and Safety Benefits
- Modern refractory materials are asbestos-free, reducing health risks and environmental impact.
- Their low heat loss and energy-efficient properties contribute to sustainable industrial practices.
By addressing these key points, refractory materials play a vital role in ensuring the efficient, safe, and durable operation of furnaces across various industries.
Summary Table:
Key Benefits | Description |
---|---|
High-Temperature Resistance | Withstands extreme temperatures (>1000°C) without losing structural integrity. |
Thermal Insulation | Minimizes heat loss, improves energy efficiency, and reduces operational costs. |
Protection Against Stresses | Shields furnace components from physical, thermal, and chemical stresses. |
Energy Efficiency | Reduces heat dissipation, leading to lower energy consumption. |
Structural Integrity | Maintains strength under high heat and pressure, ensuring durability. |
Multi-Layer Insulation Design | Enhances performance, durability, and safety in high-temperature environments. |
Environmental and Safety Benefits | Asbestos-free, eco-friendly, and contributes to sustainable practices. |
Enhance your furnace's performance with high-quality refractory materials—contact us today for expert advice!