A vacuum furnace is a highly advanced piece of equipment used in various industrial applications, particularly in heat treatment processes. Its unique design and operational principles offer numerous advantages, making it a preferred choice for industries requiring high precision, cleanliness, and efficiency. The use of a vacuum furnace ensures a controlled environment free from contaminants, precise temperature control, and enhanced mechanical properties of treated materials. Additionally, it supports a wide range of heat treatment processes, from annealing to hardening, while being energy-efficient and environmentally friendly. These benefits collectively contribute to its status as a cornerstone in modern heat treatment technology.
Key Points Explained:
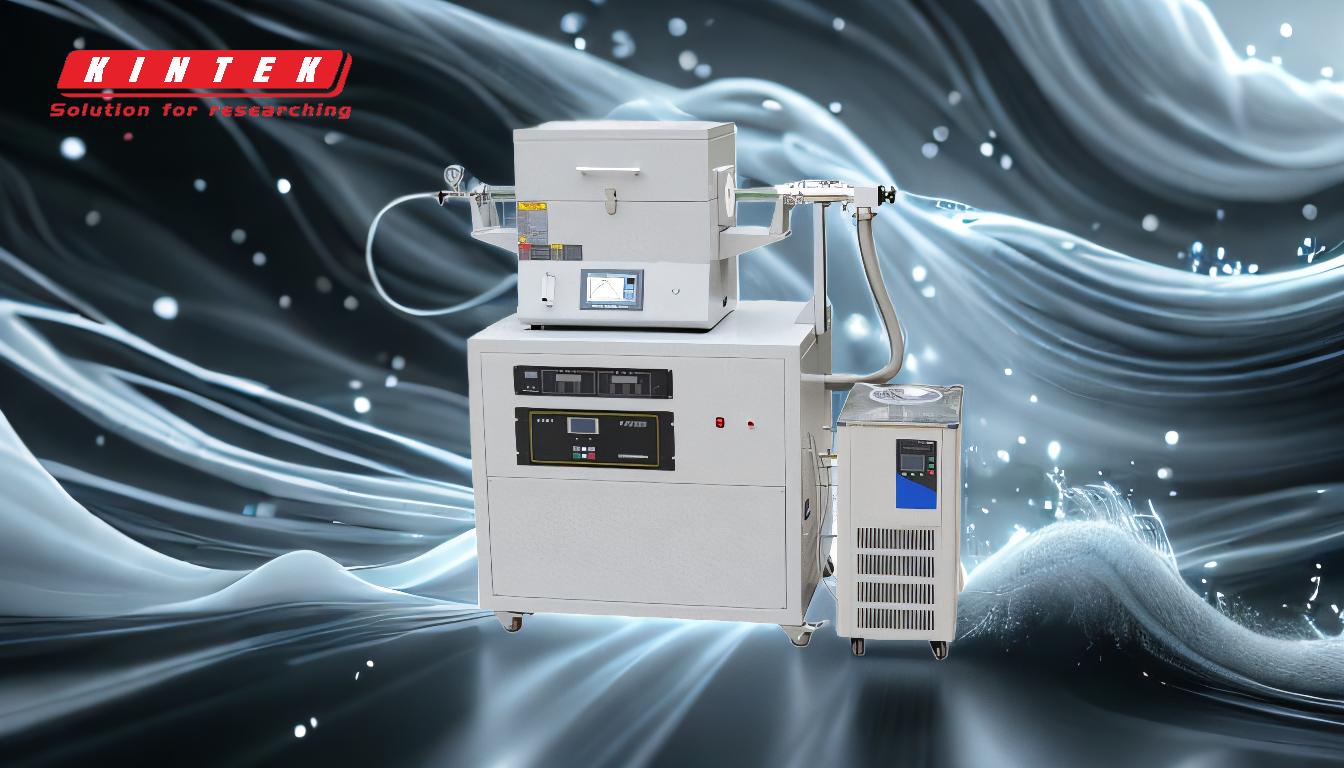
-
Clean and Controlled Environment:
- A vacuum furnace operates in a vacuum or low-pressure environment, which eliminates the presence of impurities and reactive gases like oxygen and carbon. This ensures that the treated materials remain ultra-clean and free from contamination, leading to high-quality end products.
- The absence of reactive gases prevents oxidation and decarburization, which are common issues in conventional furnaces. This is particularly crucial for materials that require high purity, such as those used in aerospace, medical, and semiconductor industries.
-
Improved Mechanical Properties:
- The controlled environment and precise temperature management in a vacuum furnace enhance the mechanical properties of treated materials. Processes like annealing, tempering, and hardening result in improved hardness, strength, and wear resistance.
- Dimensional stability is preserved during heat treatment, reducing the risk of warping or distortion. This is especially important for components with tight tolerances, such as gears, bearings, and cutting tools.
-
Precise Temperature Control:
- Vacuum furnaces offer excellent temperature uniformity and stability, with precise control over the heating zone. This ensures consistent and repeatable results, which are critical for achieving desired metallurgical properties.
- The ability to maintain uniform temperatures over a wide range (from 800°C to 3,000°C) allows for versatile heat treatment options, accommodating various materials and processes.
-
Versatile Heat Treatment Options:
- A vacuum furnace supports a wide array of heat treatment processes, including annealing, brazing, sintering, tempering, and hardening. This versatility makes it suitable for diverse applications across multiple industries.
- For example, brazing in a vacuum furnace produces strong, clean joints without the need for flux, while sintering ensures high-density components with minimal porosity.
-
Energy Efficiency:
- Advanced insulation materials and control systems in vacuum furnaces minimize heat loss and optimize energy consumption. This not only reduces operational costs but also contributes to environmental sustainability.
- The rapid cooling (quenching) capability further enhances efficiency by shortening process cycle times, allowing for faster production rates.
-
Low Contamination and High Purity:
- The vacuum environment significantly reduces contamination from carbon, oxygen, and other gases, ensuring higher purity of the treated materials. This is particularly beneficial for applications requiring ultra-clean surfaces, such as in the production of medical implants or electronic components.
- Vacuum pumping systems remove byproducts and impurities, further enhancing the purity and quality of the final product.
-
Computer-Controlled Processes:
- Modern vacuum furnaces are equipped with computer-controlled systems that ensure precise and repeatable processes. This automation reduces human error and enhances the consistency of heat treatment results.
- The ability to program and monitor processes in real-time allows for greater control and optimization, leading to improved product quality and reduced waste.
In summary, the use of a vacuum furnace offers a multitude of benefits, including a clean and controlled environment, enhanced mechanical properties, precise temperature control, versatile heat treatment options, energy efficiency, low contamination, and automated processes. These advantages make it an indispensable tool in modern industrial applications, particularly in sectors where precision, quality, and efficiency are paramount.
Summary Table:
Advantage | Description |
---|---|
Clean and Controlled Environment | Eliminates impurities and reactive gases, ensuring high-purity materials. |
Improved Mechanical Properties | Enhances hardness, strength, and wear resistance of treated materials. |
Precise Temperature Control | Offers uniform heating and stability for consistent results. |
Versatile Heat Treatment Options | Supports annealing, brazing, sintering, tempering, and hardening processes. |
Energy Efficiency | Reduces heat loss and operational costs while being environmentally friendly. |
Low Contamination and High Purity | Ensures ultra-clean surfaces, ideal for medical and electronic applications. |
Computer-Controlled Processes | Automates processes for precise, repeatable, and optimized heat treatment. |
Ready to enhance your heat treatment processes? Contact us today to learn more about vacuum furnaces!