Understanding Tablet Presses
Table of Contents
Purpose of tablet presses in the pharmaceutical industry
Tablet presses are machines designed to compress pharmaceutical powders and granules into tablets. They play a crucial role in the pharmaceutical industry by ensuring the uniformity of each dosage unit, which is essential for patient safety. The precision capabilities offered by modern tablet presses are invaluable for pharmaceutical companies, as they help create tablets that contain the same amount of active pharmaceutical ingredients and excipients.
Importance of precision in tablet compression
Precision is of utmost importance in tablet compression. The goal is to create uniform tablets that meet specific size, weight, and hardness requirements. Tablet presses must be highly precise to ensure that each tablet contains the correct dosage of the medication. This precision ensures consistency in the therapeutic effects of the tablets and minimizes the risk of dosage variations that could potentially harm patients.
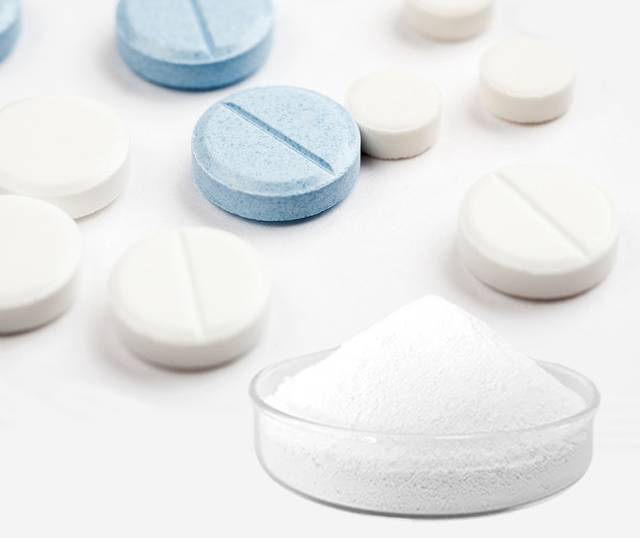
Types of tablet presses: Single punch presses and multi-station/rotary presses
There are two different classifications of tablet press machines: single punch presses and multi-station/rotary presses.
Single punch presses, also known as eccentric or single station presses, are the simplest form of tablet press. They consist of a single station of tooling that includes a pair of upper and lower punches and a die. In this type of press, the lower punch remains stationary while the upper punch exerts the compression force to create the tablets. Single punch presses are commonly used for projects where minimal amounts of test material are available or when the user only needs to confirm the compressibility of the material.
Multi-station/rotary tablet presses have multiple tooling stations. As the turret, which holds the tooling, rotates, the punches move between a set of upper and lower compression rolls that exert enough compression to form uniform tablets in large quantities. In this type of press, both the upper and lower punches move, and the tablet compression occurs between the two. Rotary presses are ideal for applications requiring high batch production as they offer significant output and precise control.
Rotary presses have several advantages over single punch presses, including the ability to independently control the weight, thickness, and hardness of tablets. They also have the capability to produce a higher number of tablets per hour, depending on press size and tooling configurations. Rotary presses are more cost-efficient compared to single punch presses and can meet most tablet batch requirements in various industries, including pharmaceutical, nutraceutical, confectionery, and veterinary applications.
In conclusion, tablet presses are essential machines in the pharmaceutical industry for compressing powders and granules into uniform tablets. The precision offered by these presses ensures consistent dosages and patient safety. Understanding the different types of tablet presses, such as single punch presses and multi-station/rotary presses, helps in choosing the right equipment for specific production needs.
Single Punch Tablet Presses
Description and basic functioning
The goal of single punch tablet presses is to increase the output of tablets. These presses utilize a single station of tooling, consisting of a pair of upper and lower punches and a die. The lower punch remains stationary while the upper punch exerts the compression force to create the tablets. This type of press is categorized as a stamping process.
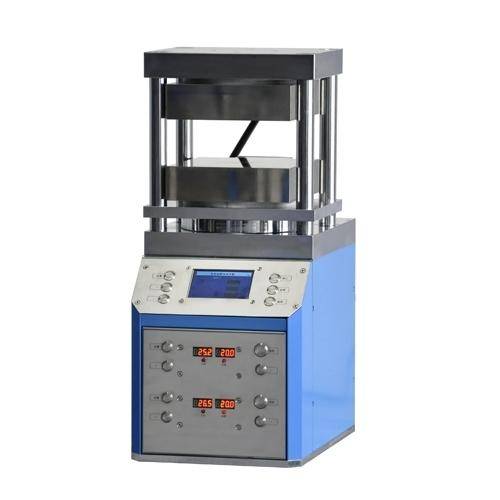
Components: Hopper, Die Cavity, Punches, Dosing plow, Ejection Cam
Single punch presses contain several components:
- Hopper: The area that holds the powder mixture prior to compression.
- Die Cavity: The area where compression occurs, determining the tablet's size and diameter.
- Punches: Components that compress the powder mixture.
- Dosing plow: Pushes a small, precise amount of product into the die cavity.
- Ejection Cam: Pushes the bottom punch upwards, ejecting the finished tablet from the die cavity.
Advantages: Small size, Ease of operation, Low noise levels, Compression feasibility
Single punch tablet presses offer several advantages:
- Small size: These presses have a compact footprint, making them easily movable.
- Ease of operation: They are simple to operate and require minimal training.
- Low noise levels: Single punch presses operate with low noise levels, providing a quieter work environment.
- Compression feasibility: These presses are capable of effectively compressing powder mixtures into tablets.
Applications suited for single punch presses
Single punch tablet presses are best suited for the following applications:
- Small batch production: They are ideal for projects with minimal amounts of test material available.
- Compressibility testing: Single punch presses allow users to confirm the compressibility of materials.
- Research and development: These presses are commonly used in laboratory settings for small-scale production.
Please note that the above information is specific to single punch tablet presses and does not cover rotary tablet presses, which are used for high batch production.
Multi-Station/Rotary Tablet Presses
Description and basic functioning
Multi-station/rotary tablet presses are machines designed to compress pharmaceutical powders and granules into tablets. They are highly precise and efficient, allowing for high-volume production of uniform tablets.
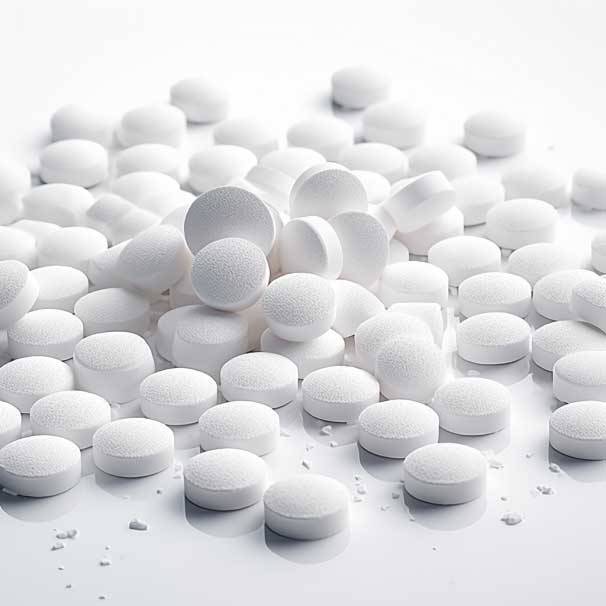
Components
- Hopper: The area that holds the powder mixture prior to compression.
- Die Cavity: The area where compression occurs, determining the size and diameter of the tablet.
- Punches: Components that compress the powder mixture.
- Dosing plow: Pushes a small, precise amount of product into the die cavity.
- Ejection Cam: Pushes the bottom punch upwards, ejecting the finished tablet from the die cavity.
- Feeder System: Distributes product from the hopper into the die cavities, over-filling them prior to more precise control by the dosing station.
- Fill cams and Dosing station: Control the precise amount of product fed into the die cavities prior to compression, determining tablet weight.
- Pre-Compression Rollers: Provide initial compression to remove any air trapped within the die cavity.
- Main Compression Rollers: Exert the final compression force to form the finished tablets.
- Take-Off Blade: Guides tablets into the discharge chute after they have been ejected from the die cavity.
- Discharge Chute: Directs completed tablets out of the press for collection.
Advantages
- Ability to control weight, thickness, and hardness of tablets.
- High production capacity, with the capability to produce up to 1,000,000+ tablets per hour.
- Precision control and management of the filling of die cavities.
- Interface capability for remote monitoring and data archiving.
- Greater cost efficiency compared to single punch presses.
Applications suited for multi-station/rotary presses
Multi-station/rotary tablet presses are ideal for applications requiring high batch production, such as in the pharmaceutical, nutraceutical, confectionery, and veterinary industries. They can also be used for producing catalysts, ceramics, powdered metals, and other compressible materials. These presses offer precise control, efficiency, and the ability to meet specific requirements for tablet weight, thickness, and hardness.
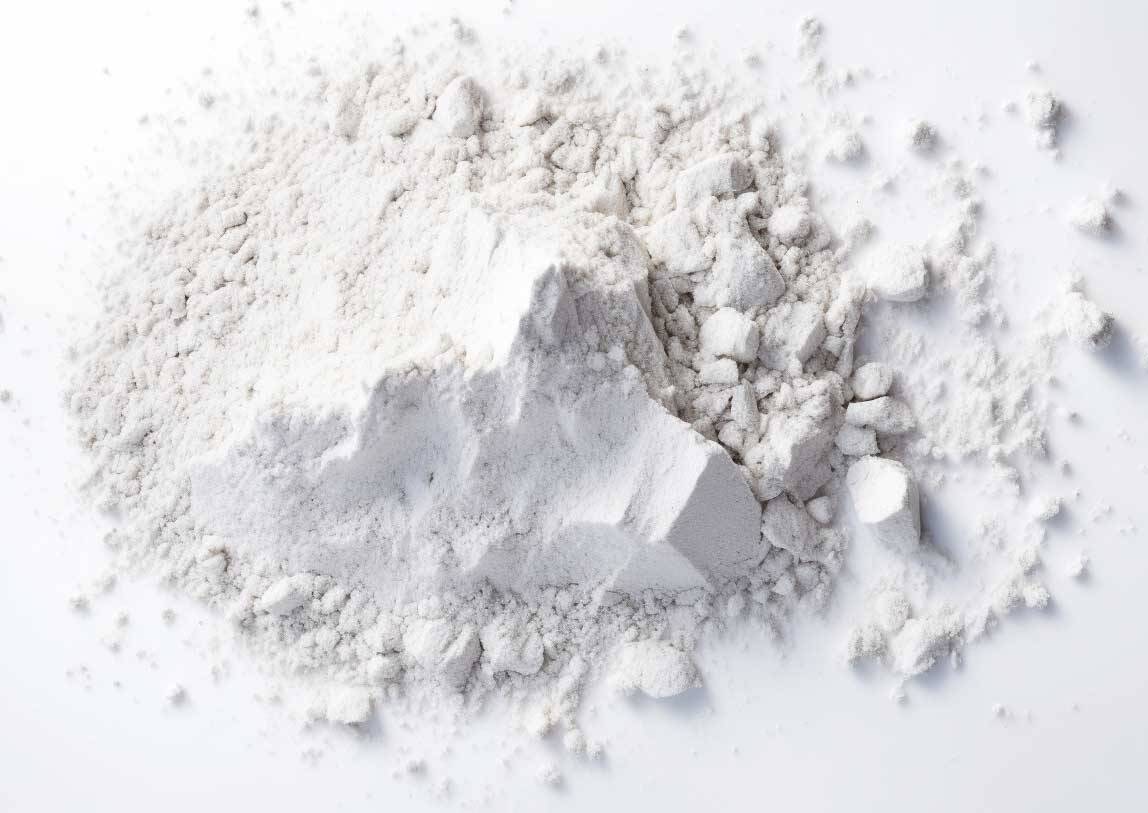
Maintenance and Replacement Parts for Tablet Presses
Importance of quality replacement parts
Tablet presses are composed of various parts that play a crucial role in the production of tablets. It is important to use high-quality replacement parts to ensure the efficient operation of the press. Parts like punches and dies, which determine the size, shape, and appearance of the tablets, are particularly important. Using low-quality or worn-out parts can affect the weight, thickness, and hardness of the tablets, leading to inconsistent results. By choosing quality replacement parts, you can maintain the performance of your tablet press and avoid production issues.
Significance of punches and dies
Punches and dies are essential components in tablet presses. They determine the size, shape, and appearance of the tablets. High-quality punches and dies are crucial for producing tablets with consistent weight, thickness, and hardness. Worn-out or low-quality punches and dies can result in tablets that do not meet the desired specifications. By using high-quality punches and dies, you can ensure the production of high-quality tablets that meet the required standards.
Correlation between preventive maintenance and machine efficacy
Proper maintenance is key to maximizing the efficiency and efficacy of tablet presses. Implementing a preventive maintenance program can result in better equipment reliability and improved process control. Regular maintenance helps identify and address any potential issues before they become major problems. It also helps in maintaining consistent metallurgical and mechanical properties of the tablets. By investing in preventive maintenance, you can minimize downtime, improve productivity, and extend the life of your tablet press.
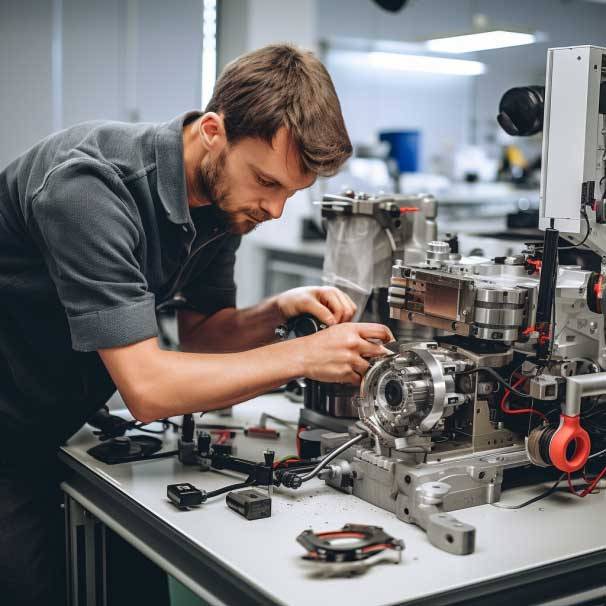
At KinTek, we understand the importance of maintenance and replacement parts for tablet presses. We offer a comprehensive inventory of high-quality parts, spares, and consumables to help you maintain the performance of your equipment. Our extensive network of relationships enables us to supply parts for all makes and models of tablet presses in the market. By choosing our parts and spares, you can extend the life of your equipment, reduce risk, and upgrade your equipment's specifications. Trust KinTek for all your tablet press maintenance and replacement part needs.
With our high-quality tablet presses, including our flagship FE-series, renowned i-series, and economical P-series, you can expect critical efficiency and pin-point accuracy in your tablet production. We have established ourselves as a trusted industry leader with thousands of machines installed globally. Whether you are in the automotive industry or other industrial applications, our tablet presses are designed to meet your needs.
In conclusion, using quality replacement parts, particularly punches and dies, is essential for the efficient operation of tablet presses. Implementing a preventive maintenance program can improve equipment reliability and process control. At [Company Name], we provide a comprehensive inventory of parts and spares to help you maintain the performance of your tablet press. Trust us for all your tablet press maintenance and replacement part needs.
Efficiency and Quality of Tablet Presses
Role of efficiency in tablet press results
Tablet presses play a crucial role in the pharmaceutical industry, where the production of uniform and precise tablets is essential. The efficiency of a tablet press is directly linked to the quality of the tablets it produces. KinTek, a trusted industry leader, understands the importance of efficiency in tablet press results.
Throughout their years of service, KinTek has continually created high-quality tablet presses that provide critical efficiency and pin-point accuracy. Their product line has gained a reputation for its exceptional quality, leading to thousands of installations globally.
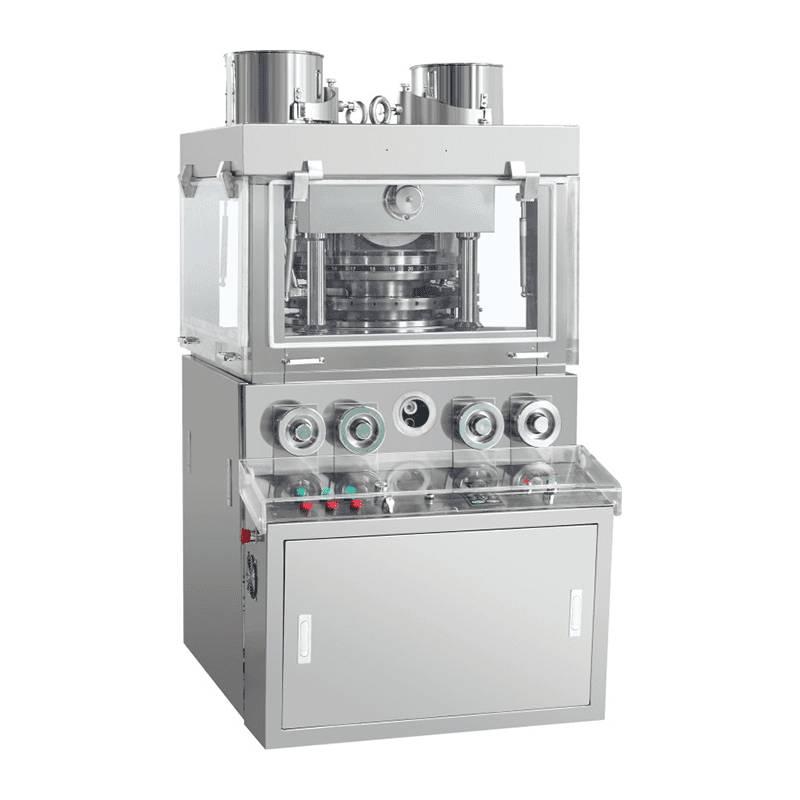
Overview of KinTek's high-quality tablet press models: The FE-series, The i-series, The P-series
KinTek offers a range of tablet press models to cater to different needs. Let's take a closer look at their flagship press models:
-
The FE-series: KinTek's flagship press models, the FE-series, are known for their innovative features for changeover, operation, and maintenance. These presses provide enhanced efficiency and productivity, allowing for seamless transitions between different tablet formulations.
-
The i-series: Renowned worldwide, the i-series tablet presses are recognized for their cutting-edge precision and tank-like strength. These presses combine advanced technology with robust construction to ensure high-quality tablet production.
-
The P-series: KinTek's P-series tablet presses offer the same legendary quality as their flagship models but at a more economical price point. These presses provide cost-effective solutions without compromising on efficiency or reliability.
KinTek's tablet presses are highly versatile and can be customized with a wide variety of ancillary equipment to further enhance productivity. Whether it's a large-scale production run or the production of single pellets, KinTek has a tablet press that suits the requirements.
In addition to their range of tablet presses, KinTek also offers benchtop press options for laboratories with space restrictions. These benchtop presses provide the same level of customization and high-quality output as larger alternatives while occupying a smaller footprint.
Tablet presses must be efficient to produce the best results. KinTek's commitment to efficiency and quality has made them a trusted name in the industry. With their range of high-quality tablet press models, including the FE-series, i-series, and P-series, KinTek continues to deliver exceptional performance for tablet production.
If you are interested in our products, please visit our company website:https://kindle-tech.com/product-categories/heated-lab-press, where innovation has always been a priority. Our R&D team consists of experienced engineers and scientists who closely follow industry trends and are constantly pushing the boundaries of what is possible. Our laboratory equipment incorporates the latest technology to ensure that you can obtain accurate and repeatable results during your experiments. From high-precision instruments to intelligent control systems, our products will provide you with unlimited possibilities for your experimental work.
CONTACT US FOR A FREE CONSULTATION
KINTEK LAB SOLUTION's products and services have been recognized by customers around the world. Our staff will be happy to assist with any inquiry you might have. Contact us for a free consultation and talk to a product specialist to find the most suitable solution for your application needs!