Basic Principles of PVD Coating Process
Evaporation
In a vacuum environment, the solid material, known as the target, undergoes a transformation into its gaseous state through various methods, primarily involving heating. This process, known as evaporation, is fundamental to the Physical Vapor Deposition (PVD) coating process. Several techniques are employed to achieve this transformation:
-
Thermal Evaporation: This method involves heating the target material to its evaporation temperature using electrical resistance or other heating elements. Once the material reaches its vaporization point, it turns into a gas, which then diffuses and condenses on the substrate to form a thin film.
-
Electron Beam Evaporation: Here, a high-energy electron beam is directed towards the target material, causing it to evaporate. This technique is particularly useful for materials with high melting points, as the localized heating effect allows for precise control over the evaporation process.
-
Laser Evaporation: Utilizing high-energy laser pulses, this method vaporizes the target material. Laser evaporation is advantageous for preparing complex thin film materials, as it offers high precision and can be used to evaporate materials that are difficult to handle with traditional methods.
Each of these methods has its unique advantages and is chosen based on the specific requirements of the coating process, such as the type of material being used and the desired properties of the resulting film.
Transportation
The gaseous material, once transformed into a vapor state, undergoes diffusion within the vacuum chamber. This diffusion is a critical phase in the PVD process, as it directly influences the uniformity and quality of the subsequent film deposition. Several key factors significantly impact this transportation phase:
-
Gas Pressure: The pressure within the vacuum chamber plays a pivotal role. Lower pressures typically enhance the diffusion efficiency, ensuring that the gaseous material spreads more uniformly across the substrate. Conversely, higher pressures can lead to collisions between gas molecules, potentially reducing the overall diffusion rate and affecting the film's uniformity.
-
Temperature: The temperature within the vacuum environment is another crucial variable. Higher temperatures can accelerate the diffusion process, but they must be carefully controlled to prevent thermal damage to the substrate or the formation of non-uniform deposits. Balancing temperature with other process parameters is essential for optimal diffusion.
-
Substrate Position: The spatial arrangement of the substrate relative to the source of the gaseous material is also significant. Proper alignment ensures that the gaseous material reaches all areas of the substrate evenly, preventing localized over-deposition or under-deposition. Techniques such as rotating or tilting the substrate can help achieve more uniform coverage.
In summary, the transportation of gaseous material in a vacuum is a nuanced process that requires meticulous control over gas pressure, temperature, and substrate positioning to ensure the successful deposition of a high-quality film.
Deposition
During the deposition phase, the gaseous material, which has been transported to the substrate, begins to cool and condense. This cooling process is crucial as it transforms the gas into a solid thin film, adhering to the substrate's surface. The deposition process is not merely a physical change but also a transformative one, significantly altering the substrate's properties based on the specific application.
The type of gas used during deposition plays a pivotal role in determining the film's final structure and characteristics. For instance, inert gases like argon and helium are often employed to maintain the purity of the film, ensuring that no unwanted chemical reactions occur. On the other hand, reactive gases such as oxygen, nitrogen, and fluorine are introduced to create specific compounds like oxides, nitrides, and fluorides, enhancing the film's functionality for particular applications.
Moreover, the pressure of the gas in the deposition chamber is a critical parameter that influences both the deposition rate and the quality of the film. Lower gas pressures typically result in denser and more homogeneous films, which are desirable for many applications. Conversely, higher gas pressures can lead to rougher films, which might be beneficial in certain contexts, such as when increased surface area is needed for better adhesion or reactivity.
In summary, the deposition process is a sophisticated interplay of cooling, gas type, and pressure, each factor meticulously controlled to achieve the desired film properties. This careful orchestration ensures that the resulting thin film meets the exacting standards required by various industries, from electronics to optics and beyond.
Main Types of PVD Process
Evaporation Deposition
Evaporation deposition is a sophisticated technique used to produce thin films by heating target materials to their vaporization point. This process is particularly effective for metals and certain alloys, transforming them from solid to gaseous states through thermal energy. The vaporized atoms then condense onto the substrate, forming a uniform and conformal thin film. This method is typically conducted in a high-vacuum environment to minimize collisions and contamination, ensuring the purity and integrity of the deposited film.
One of the key advantages of evaporation deposition is its ability to create high-quality films with excellent uniformity and conformality. This technique is versatile, capable of depositing a wide array of materials, including metals, ceramics, and semiconductors. However, the process demands a high-vacuum setting and is highly sensitive to environmental factors, which can restrict its applicability in certain scenarios.
Sputtering Deposition
Sputtering deposition is a sophisticated physical vapor deposition (PVD) technique that involves bombarding a target material with high-energy particles, typically ions from a plasma. This bombardment causes the target material to eject atoms or molecules, which then travel through the vacuum and condense onto a substrate, forming a thin film. The process is versatile, applicable to a broad spectrum of materials including metals, oxides, and nitrides.
In sputtering deposition, the target material is exposed to a plasma, often composed of argon ions and electrons. These energetic particles "knock off" atoms from the target, creating a cloud of source atoms. This cloud then condenses onto the substrate, where it forms a thin film. The choice of target material and the conditions of the plasma significantly influence the characteristics of the deposited film.
One notable aspect of sputtering deposition is the phenomenon of resputtering, where the already deposited material can be re-emitted by subsequent ion or atom bombardment. This can affect the uniformity and thickness of the film, requiring careful control of the deposition parameters to achieve desired outcomes.
Sputtering deposition is widely used in various industries due to its ability to produce high-quality, dense films with excellent adhesion to the substrate. It is particularly favored for its applicability to a wide range of materials, making it a versatile tool in the fabrication of advanced thin films for electronics, optics, and mechanical components.
Pulsed Laser Deposition (PLD)
Pulsed Laser Deposition (PLD) is a sophisticated evaporation process that employs high-energy laser pulses to vaporize a target material within a vacuum chamber. This method is particularly adept at preparing complex thin film materials, making it a preferred choice in various scientific and industrial applications.
The PLD process begins with the laser beam targeting the material, causing it to vaporize and form a plume of plasma. This plasma then deposits onto a substrate, where it condenses to form a thin film. The complexity of this process, which involves evaporation, ablation, plasma formation, and exfoliation, necessitates careful optimization. Despite the increased time and effort required to manage the numerous variables involved, PLD offers several advantages.
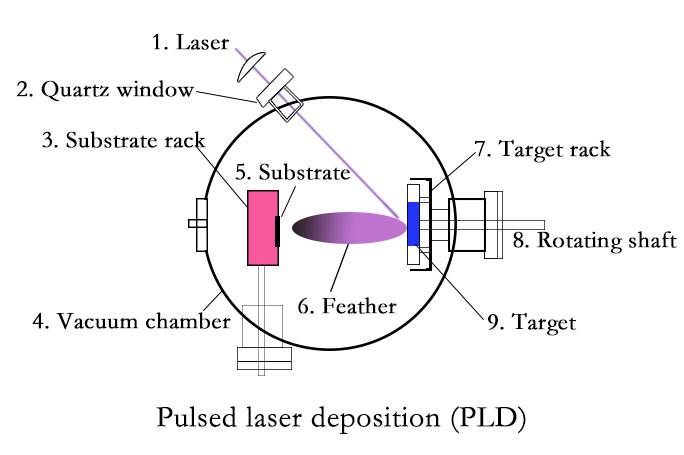
One of the key benefits of PLD is its high deposition rates, which significantly streamline the process compared to other methods. Additionally, PLD eliminates the need for filaments, simplifying maintenance and reducing potential sources of contamination. This makes PLD particularly suitable for applications requiring high precision and purity, such as in the electronics and optics industries.
In summary, while PLD's complexity demands meticulous control, its ability to produce high-quality, complex thin films efficiently and with minimal maintenance makes it a valuable tool in the realm of PVD coating processes.
Chemical Vapor Deposition (CVD)
While Chemical Vapor Deposition (CVD) differs fundamentally from Physical Vapor Deposition (PVD), there are instances where these two techniques are combined to achieve superior film properties. CVD, a vacuum deposition method, is renowned for producing high-quality, high-performance solid materials, particularly thin films used in the semiconductor industry. The process involves exposing a wafer (substrate) to one or more volatile precursors, which react and/or decompose on the substrate surface to form the desired deposit. This method is versatile, capable of depositing materials in various forms, including monocrystalline, polycrystalline, amorphous, and epitaxial structures.
In contrast to PVD, which relies on physical processes like evaporation or sputtering, CVD leverages chemical reactions to deposit materials. This chemical approach allows for greater control over the composition and properties of the deposited film. However, in certain applications, the complementary use of CVD and PVD can yield films with enhanced characteristics, such as improved adhesion, better mechanical properties, or more uniform coatings. For instance, preliminary PVD layers can be used to create a more receptive surface for subsequent CVD layers, thereby optimizing the overall film quality.
The integration of CVD with PVD is particularly beneficial in complex microfabrication processes, where the combination of chemical and physical deposition techniques can address specific challenges that neither method could handle alone. This hybrid approach not only expands the range of materials that can be deposited but also enhances the functionality and performance of the final product.
Application of Gases in the PVD Process
Inert Gases
Inert gases, such as argon (Ar) and helium (He), play a crucial role in sputter deposition processes by acting as carrier gases. These gases are favored for their ability to enhance the sputtering efficiency of the target material without causing any chemical reactions. This non-reactive nature ensures that the purity of the deposited film is maintained, which is essential for achieving high-quality coatings.
The use of inert gases is not limited to sputter deposition; they are also employed to prevent unwanted chemical reactions that can degrade a sample. Commonly, these undesirable reactions include oxidation and hydrolysis, which are typically initiated by the presence of oxygen and moisture in the air. By substituting these reactive elements with inert gases, the integrity of the sample is preserved.
Argon, in particular, is the most commonly used inert gas in various applications due to its high natural abundance and relatively low cost. It accounts for about 1% of the Earth's atmosphere, making it readily available for industrial use. While argon is the most popular, other noble gases like helium and neon can also be used depending on the specific requirements of the process.
It's worth noting that the term "inert gas" is context-dependent. While noble gases are often considered inert, they can react under certain conditions, albeit with a low probability. This characteristic is largely due to the complete valence shells of these gases, which generally make them non-reactive. However, this is not an absolute rule, as even noble gases can form compounds under specific conditions.
When specifying the purity of inert gases, it is common to indicate the contamination level in parts-per-million (ppm). For instance, a contamination level of 100 ppm means that out of every million molecules of the inert gas, 100 are foreign molecules. This measure is crucial for ensuring the effectiveness of the inert gas in maintaining the purity of the deposited film.
In summary, inert gases like argon and helium are indispensable in sputter deposition and other processes where maintaining the purity and integrity of materials is paramount. Their non-reactive nature and availability make them ideal for a wide range of industrial applications.
Reactive Gases
Reactive gases play a crucial role in the preparation of various thin films in PVD processes. These gases, which include oxygen (O₂), nitrogen (N₂), and fluorine (F₂), are essential for creating oxide, nitride, and fluoride films, respectively. The introduction of these reactive gases is often necessary to achieve the desired chemical composition and properties in the deposited films.
For instance, when preparing thin films of aluminum oxide (Al₂O₃), oxygen is typically introduced as a reaction gas. This ensures that the aluminum atoms in the vapor phase react with the oxygen to form a stable and uniform Al₂O₃ film. The use of reactive gases is not limited to aluminum oxide; it extends to other materials as well, such as silicon nitride (Si₃N₄) and titanium dioxide (TiO₂), where nitrogen and oxygen are respectively employed.
The choice of reactive gas and its concentration can significantly influence the film's properties, including its density, hardness, and chemical stability. For example, higher oxygen concentrations can lead to more porous and less dense films, while lower concentrations may result in incomplete oxidation, affecting the film's overall quality.
In summary, the judicious use of reactive gases is a critical aspect of PVD processes, enabling the creation of high-performance thin films with tailored properties for various applications.
Organic Gases
In certain specialized applications, organic gases such as ethylene and propylene play a crucial role in the preparation of polymer films and composites. These gases are often introduced into the PVD process to facilitate the formation of specific film structures that are not achievable with inert or reactive gases alone.
The use of organic gases in PVD processes is particularly beneficial for creating polymer films that require specific chemical functionalities. For instance, ethylene can be used to form polyethylene films, which are known for their excellent mechanical properties and chemical resistance. Similarly, propylene can be utilized to create polypropylene films, which are highly resistant to heat and chemicals.
Moreover, organic gases can be combined with other gases to create composite films that exhibit a blend of properties from both organic and inorganic components. This hybrid approach allows for the customization of film properties, making it possible to tailor the films for specific applications in industries such as electronics, optics, and mechanical engineering.
In summary, the incorporation of organic gases in PVD processes opens up new possibilities for the creation of advanced polymer films and composites, enabling the development of materials with unique and enhanced properties.
Adjustment of Gas Pressure
The pressure of the gas within the PVD process plays a pivotal role in determining both the deposition rate and the quality of the film. This parameter directly influences the behavior of the gaseous material as it moves from the target to the substrate.
At lower gas pressures, the gaseous material tends to diffuse more uniformly, leading to improved densification and homogeneity of the film. This is because the reduced pressure minimizes collisions between gas molecules, allowing for a more orderly deposition process. Consequently, the resulting film exhibits fewer defects and a more consistent structure.
Conversely, higher gas pressures can lead to increased film roughness. Under these conditions, the gaseous material experiences more frequent collisions, which can disrupt the orderly deposition process. This results in a less uniform film with potentially higher surface roughness. However, it is worth noting that higher pressures can also enhance the deposition rate, albeit at the expense of film quality.
Gas Pressure | Film Quality | Deposition Rate |
---|---|---|
Lower | Improved densification and homogeneity | Slower |
Higher | Increased roughness | Faster |
The optimal gas pressure is often determined by the specific requirements of the application, balancing the need for high-quality films against the desire for efficient deposition rates. This delicate balance is crucial for achieving the desired properties in the final product.
Application Areas of PVD Coating Process
Electronics Industry
In the realm of semiconductor devices, integrated circuits, and displays, the Physical Vapor Deposition (PVD) process plays a pivotal role in the fabrication of various films. Specifically, PVD is employed to prepare three primary types of films: conductive films, insulating films, and optical films.
Conductive Films
Conductive films are essential for ensuring the flow of electrical current within electronic devices. These films are typically made from metals such as aluminum, copper, and gold, which are deposited using techniques like thermal evaporation or sputtering. The choice of metal and deposition method can significantly impact the film's conductivity, adhesion, and overall performance.
Insulating Films
Insulating films, on the other hand, are crucial for preventing electrical short circuits and protecting sensitive components. Materials like silicon dioxide (SiO₂) and silicon nitride (Si₃N₄) are commonly used to create these films. The PVD process allows for precise control over the film's thickness and uniformity, which is vital for maintaining the device's integrity and reliability.
Optical Films
Optical films are designed to manage the interaction of light with the device's surface, enhancing display clarity and reducing glare. These films often include anti-reflective coatings and transmittance enhancement layers. The PVD process enables the creation of these films with specific optical properties, such as refractive index and transmittance, tailored to meet the device's requirements.
In summary, the PVD process is indispensable in the electronics industry, offering a versatile and precise method for producing the conductive, insulating, and optical films that are fundamental to modern electronic devices.
Optical Devices
The PVD (Physical Vapor Deposition) process plays a crucial role in the manufacturing of optical coatings, which are essential for enhancing the performance of various optical devices. These coatings include anti-reflective coatings, transmittance enhancement films, and protective layers, all of which are designed to optimize the interaction of light with the device's surface.
Types of Optical Coatings
-
Anti-Reflective Coatings: These coatings are engineered to minimize light reflection, thereby increasing the amount of light that passes through the optical surface. This is particularly important in applications such as camera lenses, eyeglasses, and solar panels.
-
Transmittance Enhancement Films: These films are designed to increase the transmission of specific wavelengths of light, which is crucial in devices like optical filters and sensors.
-
Protective Layers: These coatings shield the underlying material from environmental factors such as moisture, dust, and mechanical damage, ensuring the longevity and performance of the optical device.
Benefits of PVD in Optical Coating
- Precision: The PVD process allows for the precise control of film thickness, which is critical for achieving the desired optical properties.
- Durability: PVD-coated optical devices exhibit superior durability compared to those coated using other methods, making them ideal for long-term use in various environments.
- Versatility: The PVD process can be adapted to create a wide range of coatings, catering to the specific needs of different optical applications.
Applications in Optical Devices
Device Type | Coating Purpose |
---|---|
Camera Lenses | Anti-reflective coatings for better imaging |
Eyeglasses | Anti-reflective and scratch-resistant layers |
Solar Panels | Anti-reflective coatings to maximize energy capture |
Optical Filters | Transmittance enhancement for specific wavelengths |
Sensors | Protective layers to ensure consistent performance |
The PVD process not only improves the functionality of these devices but also extends their operational lifespan, making it an indispensable technology in the optical industry.
Mechanical Components
In the realm of surface treatment for mechanical components, Physical Vapor Deposition (PVD) processes play a pivotal role in enhancing their operational longevity and performance. PVD techniques are meticulously employed to augment the wear resistance, corrosion resistance, and oxidation resistance of these components. This results in a significant extension of their service life, making them more reliable and durable in demanding industrial environments.
The application of PVD in mechanical components is not merely about adding a protective layer; it is about integrating advanced materials science to create surfaces that can withstand extreme conditions. For instance, components in automotive engines, aerospace turbines, and industrial machinery often undergo rigorous conditions that can lead to rapid degradation. By applying PVD coatings, these components are fortified against the wear and tear caused by friction, chemical reactions, and high-temperature exposure.
Moreover, PVD coatings can be tailored to meet specific requirements of different mechanical components. Whether it is a high-precision tool in the manufacturing sector or a critical part in a medical device, the ability to customize the coating ensures that each component performs optimally under its unique set of conditions. This level of customization is achieved by varying the deposition parameters, such as the type of target material, gas pressure, and temperature, to fine-tune the properties of the resulting film.
In summary, the use of PVD processes in the surface treatment of mechanical components is a strategic investment in enhancing their durability and performance, ultimately contributing to the efficiency and reliability of various industrial applications.
Decorative Coatings
The PVD process is instrumental in creating decorative films that enhance the aesthetic appeal of various products. These films, characterized by their metallic luster and vibrant colors, are extensively employed in sectors such as jewelry, watches, and household items. The process allows for the precise control of film thickness and uniformity, ensuring that the final product meets the high standards of visual appeal and durability required in these industries.
In the realm of jewelry, PVD coatings provide a sophisticated finish that can mimic the look of precious metals at a fraction of the cost. This is particularly advantageous for high-volume production where maintaining a luxurious appearance is crucial. Watches, on the other hand, benefit from PVD coatings that not only enhance their visual appeal but also offer resistance to scratches and corrosion, extending the lifespan of these timepieces.
Household products, such as kitchenware and decorative items, also leverage PVD coatings to achieve a modern and sleek appearance. The ability to incorporate various colors and patterns into the coatings opens up a wide array of design possibilities, making PVD a versatile tool in the manufacturing of consumer goods.
Moreover, the PVD process is environmentally friendly, as it operates under vacuum conditions, minimizing waste and reducing the environmental impact associated with traditional coating methods. This sustainability aspect further cements its appeal in industries where both aesthetics and environmental responsibility are paramount.
Advantages and Challenges of PVD Process
Advantages
PVD coating processes offer several compelling advantages that make them a preferred choice in various industries. One of the most significant benefits is the production of high-quality films. These films exhibit exceptional adhesion, uniformity, and structural integrity, which are crucial for enhancing the performance of the coated materials. For instance, in the electronics industry, PVD-coated conductive films ensure superior electrical conductivity and minimal signal loss, while in optical devices, the coatings provide precise optical properties that enhance device performance.
Another notable advantage is the environmental friendliness of PVD processes. Unlike some other coating methods, PVD operates under vacuum conditions, minimizing the release of harmful substances into the environment. This makes PVD a sustainable option, particularly in industries where environmental regulations are stringent. Moreover, the use of inert gases like argon and helium ensures that the purity of the films is maintained without introducing any reactive by-products that could harm the environment.
The versatility of PVD processes is also a key strength. PVD can be applied to a wide range of materials, including metals, ceramics, and polymers, making it suitable for diverse applications. Whether it's preparing thin films for semiconductors, enhancing the durability of mechanical components, or creating decorative coatings for consumer products, PVD offers a flexible solution that can be tailored to meet specific needs. For example, the use of reactive gases like oxygen and nitrogen allows for the creation of complex oxide and nitride films, expanding the range of possible applications even further.
In summary, the combination of high-quality film production, environmental sustainability, and broad applicability makes PVD coating processes a highly advantageous technology across multiple sectors.
Challenges
One of the primary challenges associated with Physical Vapor Deposition (PVD) processes is the significant equipment cost. Advanced PVD systems, such as those utilizing electron beam evaporation or pulsed laser deposition, require sophisticated machinery and precise control systems, which can be prohibitively expensive for smaller operations. Additionally, the maintenance and calibration of these systems demand specialized expertise, further contributing to the overall cost.
Another critical challenge is deposition rates. Achieving optimal deposition rates is crucial for efficient production, but it can be influenced by a myriad of factors, including gas pressure, substrate temperature, and the type of target material being used. Slower deposition rates can lead to extended processing times, increasing operational costs and potentially affecting the quality of the deposited film. Conversely, higher deposition rates may result in films with suboptimal properties, such as reduced density or increased roughness.
Film thickness control is also a significant hurdle in PVD processes. Ensuring uniform film thickness across the substrate is essential for the performance and reliability of the final product. However, maintaining precise control over film thickness can be challenging, particularly when dealing with complex geometries or large-area substrates. Variations in thickness can lead to inconsistencies in the film's properties, such as its optical, mechanical, or electrical characteristics, which can be detrimental to the intended application.
To address these challenges, ongoing research and technological advancements are focused on developing more cost-effective equipment, optimizing deposition parameters, and improving control mechanisms for film thickness. These efforts aim to enhance the efficiency and reliability of PVD processes, making them more accessible and effective across various industries.
CONTACT US FOR A FREE CONSULTATION
KINTEK LAB SOLUTION's products and services have been recognized by customers around the world. Our staff will be happy to assist with any inquiry you might have. Contact us for a free consultation and talk to a product specialist to find the most suitable solution for your application needs!