Target Manufacturing
Manufacturing Methods
Sputtering target sheets and tubes are fabricated through conventional methods tailored to the specific material system. These methods encompass a range of techniques, including casting, rolling, and machining, which are selected based on the material's properties and the desired target specifications. For instance, materials with high melting points, such as tungsten and molybdenum, often require specialized processes like powder metallurgy to achieve the necessary density and homogeneity.
In the case of composites, which typically consist of two or more distinct materials, the manufacturing process becomes more intricate. Powder metallurgy, a versatile method, is frequently employed to combine these materials into a cohesive structure. This process involves several steps: the raw materials are first blended into a homogeneous powder mix, which is then compacted into the desired shape under high pressure. The compacted form is subsequently sintered at elevated temperatures to achieve bonding between the particles, resulting in a dense and uniform target.
For materials that require even higher levels of purity and control, advanced techniques such as vacuum arc melting or electron beam melting are utilized. These methods not only enhance the purity of the target but also refine its microstructure, which is crucial for achieving optimal sputtering performance. The choice of manufacturing method is thus a critical factor in determining the final quality and performance of the sputtering target.
Purification Techniques
To achieve ultra-high purity sputtering targets, the removal of impurities is paramount. This process can be accomplished through two primary methods: electron beam melting in a high vacuum system and leaching in reactive salts. Each method offers unique advantages and is suited to different types of materials and manufacturing requirements.
Electron Beam Melting
Electron beam melting (EBM) operates under high vacuum conditions, which minimizes the risk of contamination from atmospheric gases. The process involves directing a focused beam of electrons onto the target material, causing it to melt and then solidify. This method is particularly effective for materials with high melting points, as the intense heat generated by the electron beam can easily surpass their melting temperatures. The high vacuum environment ensures that any residual gases are evacuated, further purifying the material.
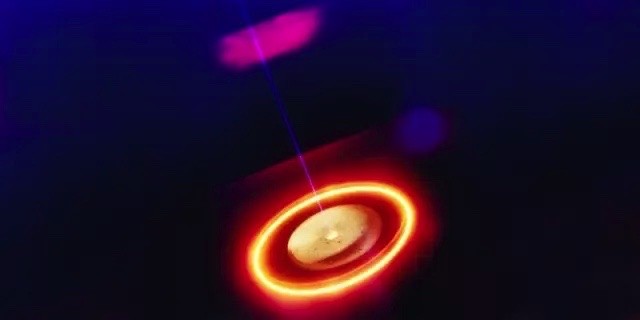
Leaching in Reactive Salts
Leaching, on the other hand, involves immersing the target material in a bath of reactive salts. These salts selectively react with and dissolve impurities, leaving the pure material behind. This technique is often used for materials that are sensitive to high temperatures or for those that require a more controlled purification process. The choice of salt and the duration of the leaching process are critical factors that can significantly influence the purity of the final product.
Both methods are essential components of the manufacturing process for ultra-high purity sputtering targets, ensuring that the final product meets the stringent purity requirements necessary for high-performance applications.
Backing Plates/Tubing, Soldering, and Diffusion Bonding
Backing plates play a crucial role in the performance of sputtering targets, necessitating properties such as low resistivity, high magnetic permeability, and good thermal conductivity. These characteristics are essential to ensure efficient energy transfer and optimal magnetic field distribution during the sputtering process.
To attach targets to these backing plates, two primary techniques are employed: soldering and diffusion bonding. Soldering involves the use of a filler metal with a lower melting point than the target and backing plate materials. This method allows for precise control over the bond's strength and thermal properties, making it suitable for applications requiring specific thermal management.
In contrast, diffusion bonding is a solid-state joining process that does not involve the melting of materials. Instead, it relies on applying high pressure and temperature to create a strong metallurgical bond between the target and backing plate. This technique is particularly advantageous for high-temperature applications and materials that may degrade when exposed to high temperatures, as it minimizes thermal damage and ensures a robust bond.
The choice between soldering and diffusion bonding often depends on the specific requirements of the application, including the material properties of the target and backing plate, the operating conditions, and the desired bond characteristics. Both methods are integral to the successful integration of targets with backing plates, ensuring the longevity and efficiency of the sputtering process.
Sputtering Target Uniformity and Film Quality
Macroscopic and Microscopic Considerations
Uniformity in sputtering targets is not merely a desirable attribute but a critical factor that directly influences the quality of the deposited films. This uniformity is influenced by a combination of macroscopic and microscopic characteristics, each playing a significant role in determining the sputtering rate and the overall film formation process.
Macroscopic Factors:
- Porosity: The presence of pores within the target material can lead to inconsistencies in the sputtering process. Pores act as barriers, disrupting the uniform flow of atoms from the target to the substrate. This can result in non-uniform film thickness and composition, which are detrimental to the performance of the final product.
- Grain Size: The size of the grains within the target material is another macroscopic factor that affects uniformity. Larger grains can lead to non-uniform sputtering rates, as the material removal process becomes less consistent across the target surface.
Microscopic Factors:
- Crystal Orientation: At the microscopic level, the orientation of the crystal grains within the target material plays a crucial role. Different crystal orientations exhibit varying sputtering rates, a phenomenon known as preferential sputtering. This can cause localized variations in the film's composition and structure, affecting its overall quality and performance.
By carefully controlling both macroscopic and microscopic factors, manufacturers can ensure a more uniform sputtering process, leading to higher quality films with consistent properties.
Porosity and Voids
Porosity and voids are critical defects that can arise during various stages of the manufacturing process, significantly impacting the uniformity of the sputtering rate and the overall quality of the deposited film. These defects often originate from the inherent limitations of conventional manufacturing methods, such as casting, powder metallurgy, and even during the purification stages where high-temperature processes can introduce microstructural inconsistencies.
For instance, in powder metallurgy, the consolidation of metal powders into a solid form can leave behind microscopic voids if the sintering process is not perfectly controlled. Similarly, during casting, gas entrapment can create porosity, especially in materials with high melting points where the viscosity of the molten metal can prevent the escape of gases. These voids and pores can act as preferential sites for the initiation of cracks, leading to non-uniform sputtering rates and poor film quality.
Moreover, the presence of porosity and voids can also affect the thermal and electrical conductivity of the target material, further complicating the sputtering process. For example, regions with high porosity may sputter at different rates compared to denser areas, leading to variations in film thickness and composition. This non-uniformity is particularly problematic in applications where precise film properties are critical, such as in semiconductor manufacturing.
Preferential Sputtering and Grain Morphology
Different crystal orientations exhibit varying sputtering rates, a phenomenon known as preferential sputtering. This selective erosion can significantly influence the grain morphology and size of the material, which are directly affected by the manufacturing processes employed.
In the context of Physical Vapor Deposition (PVD) techniques, the uniformity of the sputtered film is heavily dependent on the consistency of the target material. The grain structure of the target, characterized by its orientation and size, plays a crucial role in determining the sputtering efficiency and the resulting film quality. For instance, grains with certain orientations may erode more rapidly, leading to non-uniform sputtering and potentially compromising the integrity of the deposited film.
The manufacturing processes, such as powder metallurgy and hot isostatic pressing (HIP), are instrumental in shaping the grain structure of the target material. These processes not only influence the density and porosity of the target but also dictate the final grain morphology, which in turn affects the sputtering behavior. Therefore, understanding and controlling these manufacturing parameters is essential for optimizing the performance of PVD sputtering targets.
Hot Isostatic Pressing (HIP) and High Pressure Heat Treatment (HPHT)
HIP Applications
Hot Isostatic Pressing (HIP) is a critical process in the manufacturing of high-quality sputtering targets, particularly for materials produced via castings and powder metallurgy. The primary function of HIP is to eliminate porosity and voids within these materials, thereby enhancing their density and uniformity. This process involves subjecting the material to high pressure and temperature in a controlled environment, which compresses the material and forces it to achieve a near-perfect density.
The significance of HIP in reducing porosity cannot be overstated. Porosity, which can arise from various manufacturing processes, significantly impacts the sputtering rate and the overall quality of the film formed. By removing these microscopic voids, HIP ensures that the sputtering target behaves uniformly during the sputtering process, leading to more consistent film deposition.
Moreover, HIP contributes to the structural integrity of the sputtering targets. Materials that undergo HIP exhibit superior mechanical properties, including increased strength and toughness. This is particularly important for high-performance applications where the reliability and longevity of the sputtering targets are paramount.
In summary, HIP is an indispensable technique in the production of sputtering targets, ensuring that they meet the stringent requirements for high density, uniformity, and structural integrity.
Benefits of HPHT
High Pressure, High Temperature (HPHT) treatment offers several advantages in the manufacturing of various material systems. One of the key benefits is the improved temperature uniformity it provides, which ensures that the entire material system is subjected to consistent thermal conditions. This uniformity is crucial for maintaining the integrity and performance of the final product.
HPHT also allows for controlled cooling rates, which is essential for preventing thermal stress and cracking in materials. By precisely managing the cooling process, manufacturers can achieve the desired mechanical properties and minimize defects. This level of control is particularly important in the production of high-value materials like diamonds, where even minor imperfections can significantly impact the quality and market value.
Moreover, HPHT facilitates repeatable process times, ensuring that each batch of materials is produced under identical conditions. This repeatability is vital for maintaining consistent product quality and performance. For instance, in the diamond industry, HPHT can transform less attractive diamonds into high-quality, colorless, pink, blue, or canary yellow diamonds, significantly enhancing their market value.
The process of HPHT involves subjecting diamonds to high pressure and temperature, which not only improves their color but also enhances their clarity. This makes HPHT diamonds highly desirable in the jewelry industry, where clarity and color are key determinants of a diamond's quality. Despite some differences between HPHT and Chemical Vapor Deposition (CVD) diamonds, HPHT treatment is often used to enhance the finish of CVD diamonds, ensuring they meet high-quality standards.
In summary, HPHT treatment offers a range of benefits that are essential for the manufacturing of high-quality materials. Its ability to provide improved temperature uniformity, controlled cooling rates, and repeatable process times makes it an invaluable technique in various industries, particularly in the production of high-value materials like diamonds.
Cannulated HIP and Diffusion Bonding
Cannulated Hot Isostatic Pressing (HIP) and diffusion bonding techniques are integral to producing intricate shapes and ensuring robust bonding between the target and the backing plate. These methods are particularly advantageous when dealing with premium materials that require superior properties such as corrosion and wear resistance, often applied onto more economical substrates to optimize cost efficiency.
HIP can facilitate multiple diffusion bonds within a single process cycle, making it a versatile and efficient solution for complex manufacturing needs. The technique is compatible with a wide range of materials, including metals like nickel, cobalt, tungsten, titanium, molybdenum, aluminum, copper, and iron-based alloys, as well as ceramics, glasses, intermetallics, and high-performance plastics.
The process involves stringent control over inert gas purity, typically using argon, to meet or exceed customer, military, and industry specifications. Reproducible, automated HIP cycles are tailored to meet specific customer needs, ensuring component traceability from start to finish. Additionally, technical support is available for HIPing novel materials or alloys, and the process is adaptable to various tooling requirements, ensuring compatibility with the HIP cycle and material specifications.
By leveraging cannulated HIP and diffusion bonding, manufacturers can achieve not only strong and reliable bonds but also the production of complex geometries that would be challenging to achieve through other methods. This versatility and precision make these techniques indispensable in the manufacturing of high-quality sputtering targets.
CONTACT US FOR A FREE CONSULTATION
KINTEK LAB SOLUTION's products and services have been recognized by customers around the world. Our staff will be happy to assist with any inquiry you might have. Contact us for a free consultation and talk to a product specialist to find the most suitable solution for your application needs!