Introduction
Table of Contents
Isostatic presses are an essential tool in various industries, offering efficient and effective solutions for material processing. These presses utilize equal pressure in all directions to achieve uniform shaping and densification of materials. Understanding the different types, processes, and applications of isostatic presses is crucial for businesses looking to optimize their manufacturing processes. Whether it's utilizing cold isostatic presses (CIP) for ceramic production or hot isostatic presses (HIP) for aerospace components, the versatility and precision of isostatic pressing make it a valuable technology in today's competitive market. Let's explore the world of isostatic presses and uncover their potential.
Types of Isostatic Presses
Isostatic pressing is a process that involves applying equal pressure to a compacted powder to achieve optimal density and microstructure uniformity. There are two main types of isostatic presses: Cold Isostatic Presses (CIP) and Hot Isostatic Presses (HIP).
Cold Isostatic Presses (CIP)
Cold isostatic pressing (CIP) is a method of isostatic pressing that involves the compaction of powders encased in elastomer molds. This process applies pressure from multiple directions, resulting in greater uniformity of compaction and increased shape capability compared to uniaxial pressing.
There are two methods of carrying out cold isostatic pressing:
-
Wet-bag isostatic pressing: In this method, the powder is encased in a rubber sheath that is immersed in a liquid, which transmits the pressure uniformly to the powder.
-
Dry-bag isostatic pressing: Instead of immersing the tooling in a fluid, the tooling itself is built with internal channels into which high-pressure fluid is pumped.
The cold isostatic press, also known as a rubber press, is capable of forming complicated shapes that cannot be compressed without a uniaxial press or machine press. Ceramic powder and metal powder are filled into a rubber mold, which is then dipped into the pressure vessel. The powder is compressed at a maximum water pressure of 400 MPa.
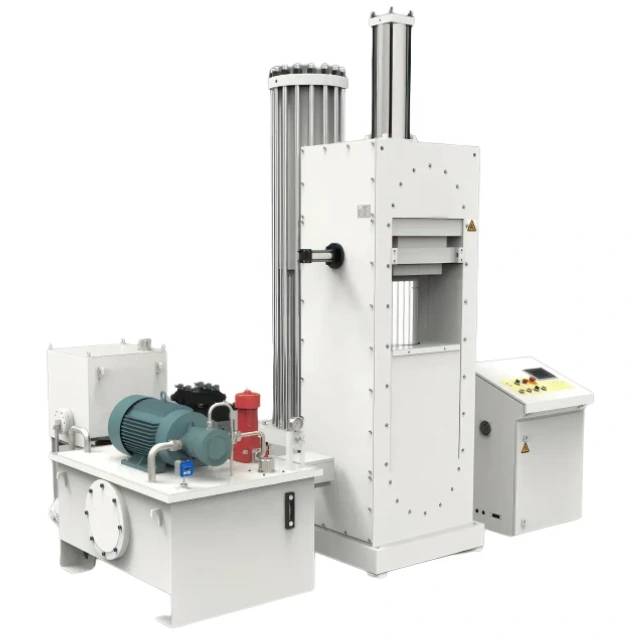
Hot Isostatic Presses (HIP)
Hot Isostatic Pressing (HIP) is another method of isostatic pressing that involves compressing materials by applying high temperature and isostatic pressure simultaneously. Argon is commonly used as the pressure medium in HIP.
Hot pressing is similar to HIP, but it applies only uniaxial pressure instead of isostatic pressure. Hot Isostatic Pressing is used to reduce the porosity of metals and increase the density of many ceramic materials.
In powder metallurgy, HIP allows the compression of metal powder at high temperatures and pressures, resulting in a product with a homogeneous annealed microstructure and minimal impurities. This process is essential for manufacturing aerospace components and other applications.
Hot Isostatic Pressing (HIP) is a manufacturing technique used to increase the density of materials by reducing or eliminating their porosity. It creates fully dense 'wrought' materials and improves density, composition, and dynamic strength.
Both cold and hot isostatic presses have their specific uses and applications in various industries, including pharmaceuticals, explosives, chemicals, nuclear fuel, and ferrites.
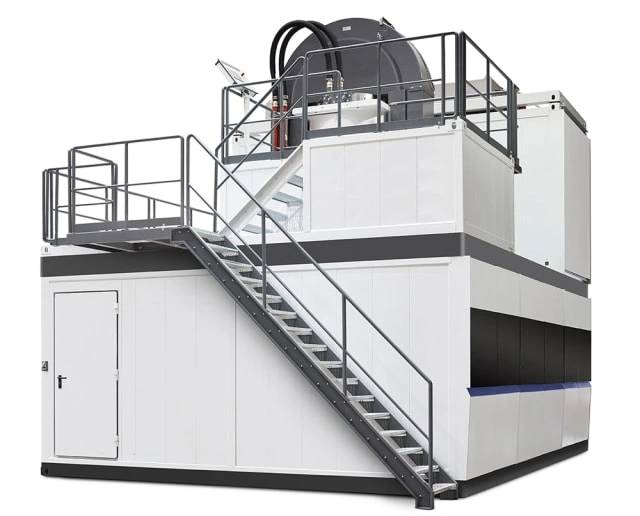
Processes of Isostatic Pressing
Cold Isostatic Pressing Process
Cold isostatic pressing (CIP) is a powder processing technique that uses fluid pressure to compact a part. It involves placing metal powders in a flexible container, which serves as the mold for the part. Fluid pressure is exerted over the entire outside surface of the container, causing it to press and form the powder into the desired geometry. Unlike other processes that exert forces on the powder through an axis, CIP applies pressure from all directions.
The CIP process is performed at room temperature and uses a mold made from elastomer materials such as urethane, rubber, or polyvinyl chloride. The fluid used in CIP is typically oil or water. During the operation, fluid pressure ranges from 60,000 lbs/in2 (400 MPa) to 150,000 lbs/in2 (1000 MPa). One disadvantage of CIP is its low geometric accuracy due to the flexible mold.
Hot Isostatic Pressing Process
Hot isostatic pressing (HIP) is a manufacturing process that utilizes elevated temperature and isostatic gas pressure to eliminate porosity and increase density in metals, ceramics, polymers, and composite materials. This process improves the mechanical properties and workability of the materials. HIP is primarily used for eliminating microshrinkage in castings, consolidating powders, and diffusion bonding.
In the HIP process, the products are placed in a closed container filled with a liquid and subjected to equal pressure on each surface. This high-pressure environment increases the density of the products and shapes them according to the desired specifications. Isostatic presses are widely used in the forming of high-temperature refractory, ceramics, cemented carbide, lanthanon permanent magnet, carbon material, and rare metal powder.
Hot isostatic pressing is also employed as part of a sintering process, for pressure-assisted brazing, and for the fabrication of metal matrix composites.
Isostatic pressing, both cold and hot, offers unique benefits for a wide range of materials, including ceramics, metals, composites, plastics, and carbon. It allows for the formation of product shapes with precise tolerances, reducing the need for costly machining. The isostatic pressing process has evolved from a research curiosity to a viable production tool and is widely used in various industries today.
Applications of Isostatic Presses
Applications of Cold Isostatic Presses
Isostatic pressing is a process involving the application of equal pressure to a compacted powder to achieve optimal density and microstructure uniformity. Cold isostatic pressing, in particular, involves the compaction of powders encased in elastomer molds. Here are some common applications of cold isostatic presses:

- Pharmaceuticals
- Explosives
- Chemicals
- Food
- Nuclear fuel Ferrites
Applications of Hot Isostatic Presses
Hot isostatic pressing technology is widely used in various industries for different purposes. Some of the common applications of hot isostatic presses include:
- Treatment of castings
- Powder metallurgy
- Ceramics industry
- Porous materials
- Near-net forming
- Material bonding
- Plasma spraying
- Manufacture of high-end graphite
Applications of hot isostatic presses (castings, powder metallurgy, ceramics, porous materials, near net shape materials, high-end graphite manufacturing, plasma spraying)
Isostatic pressing offers several advantages, such as achieving high and uniform density, removing constraints on part geometry, and efficient material utilization. It is applicable to a wide range of materials, including superalloys, titanium, tool steels, stainless steel, and beryllium. The process has become a viable production tool and continues to play a significant role in various industries.
Advantages of Cold Isostatic Presses
Cold isostatic pressing is a technique used to produce large and complex spare parts at a lower initial cost compared to other methods. This method is similar to hot isostatic pressing but is conducted at lower temperatures. One of the key advantages of cold isostatic pressing is the ability to achieve a more uniform density distribution, which results in a higher quality finished product.
Here are 6 key advantages of cold isostatic pressing compared to other pressing methods:
-
Uniform product properties: Cold isostatic pressing offers more uniform product properties, greater homogeneity, and more precise control of the finished product dimensions. This ensures consistent quality and performance.
-
Greater flexibility in shape and size: With cold isostatic pressing, there is greater flexibility in the shape and size of the finished product. This allows for the production of complex and intricate parts that may not be possible with other pressing methods.
-
Longer aspect ratios: Cold isostatic pressing enables the production of long, thin pellets with longer aspect ratios. This is beneficial for applications that require specific dimensions and shapes.
-
Improved compaction and densification: The compaction of powder during cold isostatic pressing is improved, leading to better densification of the material. This results in a higher density and stronger finished product.
-
Ability to process different materials: Cold isostatic pressing can process materials with different characteristics and shapes. This versatility allows for the production of parts with varying properties and requirements.
-
Reduced cycle times and improved productivity: Cold isostatic pressing offers reduced cycle times compared to other pressing methods. This leads to improved productivity and faster production of parts.
In conclusion, cold isostatic pressing provides several advantages over other pressing methods. It offers greater control over product properties, flexibility in shape and size, improved compaction and densification, the ability to process different materials, and increased productivity. These benefits make cold isostatic pressing a preferred choice for producing large and complex spare parts.
Specific Cold Isostatic Pressing Techniques
Wet Bag Processing
Wet bag processing is a method of cold isostatic pressing that involves placing the powder into a forming mold, also known as a casing. The mold is then sealed and submerged in a high-pressure cylinder filled with liquid. The pressure transmission medium comes into direct contact with the jacket during the pressing process.
This technique offers strong applicability and is particularly suitable for experimental research and small batch production. It allows for the simultaneous pressing of multiple different shapes of parts in one high-pressure cylinder, making it ideal for producing large and complex parts. Additionally, wet bag processing has a short production process and low cost.
Segmentation of the Market: Based on product type, the cold isostatic pressing (CIP) equipment market is divided into wet bag pressing and other types.
Dry Bag Processing
In dry bag processing, the powder material is enclosed in a flex mold bag, which is then subjected to isostatic pressure in a pressure vessel. This process is performed at room temperature or at a slightly higher temperature (<93°C) and at pressures ranging from 100-600 MPa.
The goal of dry bag processing is to obtain a "raw" part with sufficient strength for handling, processing, and subsequent sintering to achieve the final strength. This technique utilizes a liquid medium, such as water, oil, or a glycol mixture, to apply pressure to the powder. Cold isostatic pressing can achieve a theoretical density of about 100% for metals and about 95% for ceramic powders.
Dry bag processing is commonly used to form powdered materials at room temperature. It involves using rubber or plastic as the encasing mold material and liquid as the pressure medium. This technique provides blanks for further sintering or hot isostatic pressing processes.
Warm Isostatic Pressing
Warm isostatic pressing is another technique used in cold isostatic pressing. It involves applying isostatic pressure to the powder at a slightly elevated temperature. This process is performed between room temperature and the sintering temperature of the material.
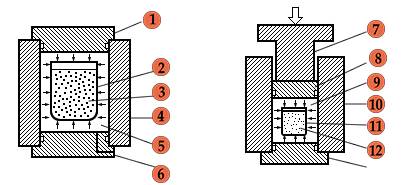
Warm isostatic pressing offers advantages such as improved densification and reduced sintering time compared to cold isostatic pressing. It is particularly suitable for materials that require high density and fine microstructure.
In conclusion, cold isostatic pressing techniques, including wet bag processing, dry bag processing, and warm isostatic pressing, offer various benefits for materials processing. Wet bag processing is ideal for experimental research and small batch production, while dry bag processing provides a method for forming powdered materials at room temperature. Warm isostatic pressing offers improved densification and reduced sintering time. The choice between these techniques depends on the specific goals of the project and the characteristics of the materials involved.
Hot Isostatic Presses' Treatment of Materials
Hot Isostatic Pressing for metal Additive Manufacturing
Hot Isostatic Pressing (HIP) is a well-established process used to improve a wide variety of materials such as titanium, steel, aluminum, and superalloys. This process is particularly effective in reducing or eliminating voids within castings and consolidating encapsulated powders to create fully dense materials. Additionally, HIP can be used to bond similar or dissimilar materials together, resulting in the manufacturing of unique and cost-effective components.
Isostatic Pressing
The isostatic pressing process was pioneered in the mid-1950s and has since become a viable production tool. It is widely used across various industries for consolidating powders and healing defects in castings. This process is suitable for a range of materials, including ceramics, metals, composites, plastics, and carbon.
Isostatic pressing applies a uniform and equal force over the entire product, regardless of its shape or size. This feature makes it particularly beneficial for ceramic and refractory applications. The ability to form products with precise tolerances reduces the need for costly machining, making isostatic pressing commercially attractive.
Hot Isostatic Pressing
Hot Isostatic Pressing (HIP) is a manufacturing process that utilizes elevated temperature and isostatic gas pressure to eliminate porosity and increase density in metals, ceramics, polymers, and composite materials. By subjecting the material to high temperatures and uniform pressure, HIP improves its mechanical properties and workability.
The primary applications of HIP include eliminating microshrinkage in castings, consolidating powders, and diffusion bonding (cladding). HIP is also commonly used in sintering processes for powder metallurgy, pressure-assisted brazing, and the fabrication of metal matrix composites.
Cold Isostatic Pressing
Cold Isostatic Pressing (CIP) is another variation of the isostatic pressing process that operates at room temperature. It applies equal pressure from all directions to compact powders or shape materials. CIP is commonly used for forming intricate shapes and achieving precise tolerances in materials such as ceramics and metals.
In conclusion, Hot Isostatic Pressing (HIP) is a highly effective process for improving the properties of various materials. It eliminates porosity, increases density, and allows for the bonding of different materials. Whether it's reducing defects in castings or consolidating powders, HIP offers numerous benefits for manufacturing industries. Additionally, the use of Cold Isostatic Pressing (CIP) at room temperature provides an alternative method for shaping materials with precision.
Conclusion
In conclusion, understanding isostatic presses and their various types, processes, and applications can greatly benefit businesses in a wide range of industries. Whether it's the use of cold isostatic presses (CIP) for manufacturing components with uniform density or hot isostatic presses (HIP) for materials treatment, these machines offer unique advantages. Cold isostatic pressing processes and specific techniques like wet bag processing, dry bag processing, and warm isostatic pressing further enhance the capabilities of isostatic presses. By harnessing the power of isostatic pressing, businesses can achieve higher quality products and improve their overall efficiency.
CONTACT US FOR A FREE CONSULTATION
KINTEK LAB SOLUTION's products and services have been recognized by customers around the world. Our staff will be happy to assist with any inquiry you might have. Contact us for a free consultation and talk to a product specialist to find the most suitable solution for your application needs!