Introduction
Table of Contents
Isostatic pressing plays a crucial role in improving additive manufacturing materials, but what exactly is it? Isostatic pressing is a technique used to enhance the properties of materials by applying equal pressure from all directions. This process helps to eliminate porosity and achieve uniform density in the final components. By understanding the ins and outs of isostatic pressing, we can unlock the potential for stronger and more reliable additive manufacturing materials. In this article, we will delve into the process and types of isostatic pressing, explore its benefits over traditional methods, and discuss the importance of metal powder characterization in achieving optimal results. So, let's dive in and discover the world of isostatic pressing!
Process and Types of Isostatic Pressing
Process of Isostatic Pressing
Isostatic pressing is a powder processing technique that uses fluid pressure to compact materials. It applies equal force over the entire product, regardless of its shape or size. The process involves placing metal powders or other materials in a flexible container, which acts as a mold. Fluid pressure is then exerted on the container from all directions, causing it to press and form the powder into the desired shape. Isostatic pressing is commonly used in industries such as ceramics, metals, composites, plastics, and carbon.
Hot Isostatic Pressing (HIP)
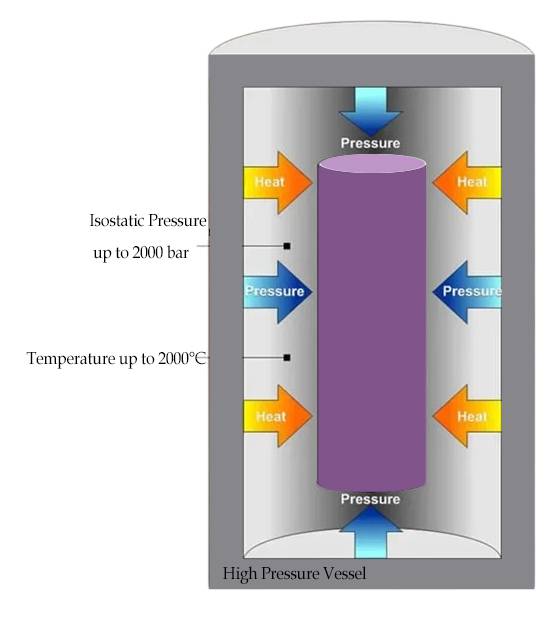
Hot isostatic pressing, or HIP, is a type of isostatic pressing that involves applying high temperature and pressure to materials. This process is used to reduce the porosity of metals and increase the density of ceramic materials, improving their mechanical properties and workability. HIP compresses materials by subjecting them to temperatures ranging from several hundreds to 2000 °C and isostatic pressure ranging from several tens to 200 MPa. The most commonly used pressure medium in HIP is argon.
Cold Isostatic Pressing (CIP)
Cold isostatic pressing, or CIP, is another method of isostatic pressing that is performed at room temperature. It uses a mold made from an elastomer material such as urethane, rubber, or polyvinyl chloride. CIP functions based on Pascal's law, which states that pressure applied in an enclosed fluid is transmitted in all directions without any change in magnitude. In CIP, powders are compacted by enclosing them in the elastomer mold and applying uniform liquid pressure to compress them. This results in a highly compact solid. CIP can be used for materials like plastics, graphite, powdered metallurgy, ceramics, and sputtering targets.
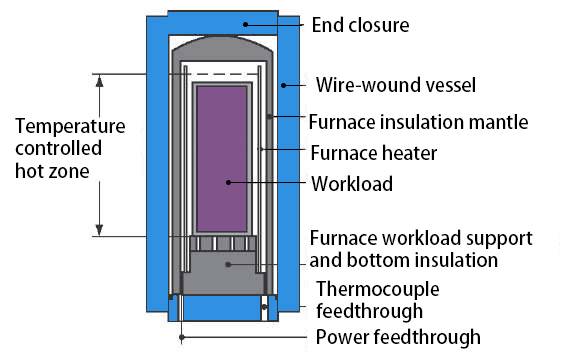
The Difference between HIP and Hot Pressing
The main difference between HIP and hot pressing lies in the application of pressure. HIP applies isostatic pressure using gas pressure, while hot pressing applies uniaxial pressure. Other processes like milling, forging, and extrusion also involve high temperature and pressure, but they do not apply isostatic pressure like HIP.
Isostatic Pressing Process
In the isostatic pressing process, products are placed in a closed container filled with liquid, and equal pressure is applied to each surface. This high-pressure environment increases the density of the products, resulting in the desired shapes. Isostatic presses are widely used in the forming of high-temperature refractory materials, ceramics, cemented carbide, lanthanum permanent magnets, carbon materials, and rare metal powders.
Characteristics of Isostatic Pressing Process
Cold Isostatic Pressing (CIP) is performed at room temperature using an elastomer mold and fluid pressure typically ranging from 60,000 lbs/in2 (400 MPa) to 150,000 lbs/in2 (1000 MPa). One disadvantage of CIP is its low geometric accuracy due to the flexibility of the mold. After the powder is compacted by CIP, the green compact is usually sintered conventionally to produce the desired part.
Benefits of Isostatic Pressing Over Press and Sinter Method
Isostatic pressing has several benefits over the commonly used press and sinter method, including equal compaction in all directions and a more uniform final component density. Nevertheless, as with other powder metallurgy processes, manufacturers must carefully characterize the metal powder’s properties for isostatic pressing to be successful.
Why is material characterization important?
Like other powder metallurgy processes, the properties of the metal powder used in isostatic pressing will affect the final sintered component’s properties. For this reason, these properties should be carefully characterized to ensure optimum final component properties.
Advantages of Isostatic Press
- Powder is compacted with the same pressure in all directions, and, since no lubricant is needed, high and uniform density can be achieved.
- The process removes many of the constraints that limit the geometry of parts compacted unidirectionally in rigid dies.
- It is applicable to difficult-to-compact and expensive materials such as superalloys, titanium, tool steels, stainless steel, and beryllium, with material utilization that is highly efficient.
Application of Isostatic Press
Below is a list of some of the most common applications of the isostatic press:
- Pharmaceuticals
- Explosives
- Chemicals
- Food
- Nuclear fuel Ferrites
Other application industries of isostatic presses (pharmaceuticals, explosives, chemicals, nuclear fuel ferrite)
Working of Isostatic Press
Isostatic pressing is enabled to produce various types of materials from powder compacts by reducing the porosity of the powder mixture. The powder mixture is compacted and encapsulated using isostatic pressure, by using pressure equally applied from all directions. Isostatic pressing confines the metal powder within a flexible membrane or hermetic container which acts as a pressure barrier between the powder and the pressurizing mediums, liquid or gas that surrounds it.
Additional Advantages of Isostatic Press
- Uniform density: The resulting compacted piece will have uniform shrinkage during sintering or hot isostatic pressing with little or no warpage.
- Shape flexibility: Isostatic pressing makes it practical to produce shapes and dimensions that are difficult or impossible to produce by other methods.
- Component size: A wide range of component sizes can be made from massive 30-ton near net PM shapes down to densifying less than 100-gram MIM parts.
- Larger parts: Part sizes are limited only by the size of the isostatic pressure chamber.
- Low tooling cost: For short production runs, the tooling cost is low in comparison to other manufacturing methods.
- Enhance alloying possibilities: Able to enhance alloying elements without inducing segregation in the material.
- Reduced lead times: Complex shapes can be economically made from prototype to production quantities with significantly reduced lead times versus forgings or machined components.
- Material and machining costs: Near net shape parts can be fabricated, greatly reducing material and machining costs.
Requirement for Metal Powder Characterization in Isostatic Pressing
Isostatic pressing has several benefits over the commonly used press and sinter method, including equal compaction in all directions and a more uniform final component density. Nevertheless, as with other powder metallurgy processes, manufacturers must carefully characterize the metal powder’s properties for isostatic pressing to be successful. KinTek offers several solutions to support this.
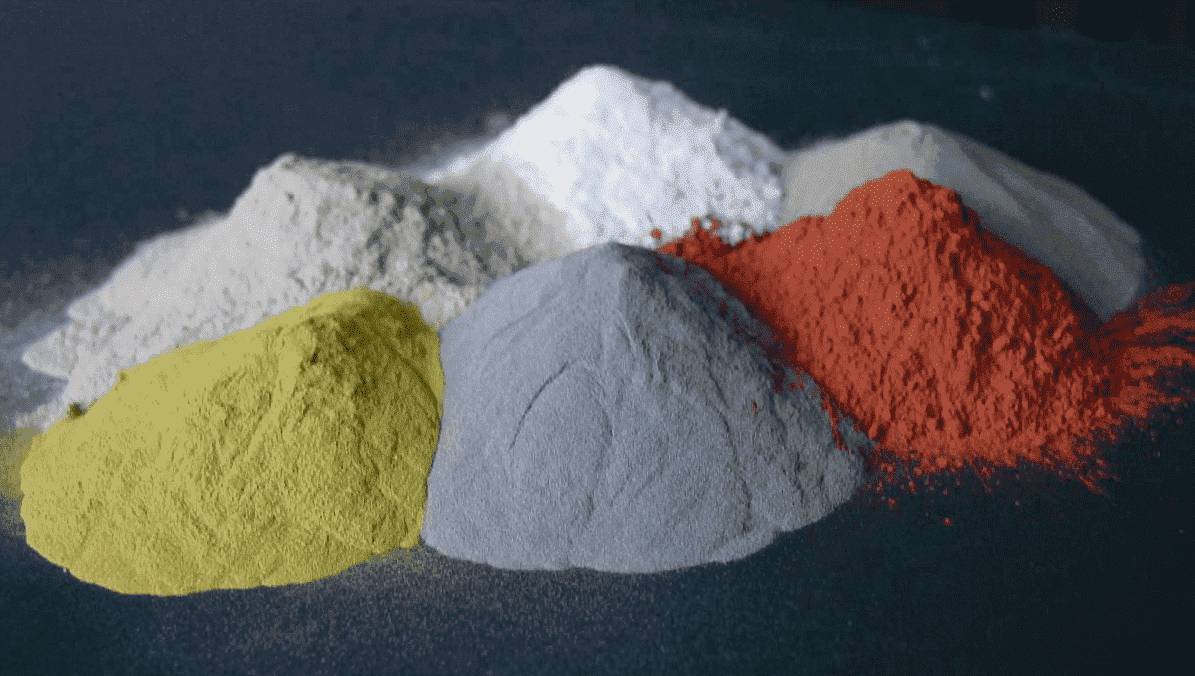
Why is material characterization important?
Like other powder metallurgy processes, the properties of the metal powder used in isostatic pressing will affect the final sintered component’s properties. For this reason, these properties should be carefully characterized to ensure optimum final component properties.
Alternative Processes
Isostatic Pressing
Isostatic pressing is a powder processing technique characteristic in the use of fluid pressure in order to compact the part. Metal powders are placed in a flexible container. This sealed container is the mold for the part. Fluid pressure is exerted over the entire outside surface of the container, causing the container to press and form the powder into the correct geometry. Most processes exert forces on the powder through an axis. Isostatic pressing is special in its use of all around pressure.
Cold isostatic pressing applies pressure to the powder at room temperature or at a slightly higher temperature (< 93°C), 100-600 MPa, to obtain a "raw" part with sufficient strength for handling and processing, and sintering to final strength. Cold isostatic pressing techniques use a liquid medium (e.g. water or oil or a glycol mixture). For metals, cold isostatic pressing achieves a theoretical density of about 100% and for ceramic powders, about 95%. Cold isostatic pressing technology is used to form powdered materials at room temperature by using rubber or plastic as the encasing mold material and liquid as the pressure medium, mainly to provide blanks for further sintering or hot isostatic pressing processes.
Importance of Material Characterization
Effects of metal powder properties on final sintered component
Material properties play a crucial role in the final outcome of the sintering process. The properties of metal powder, such as particle size distribution and shape, can significantly impact the quality of the sintered component. For example, spherical powders with a consistent particle size distribution are preferred for hot isostatic pressing (HIP) because they produce higher fill densities. On the other hand, cold isostatic pressing (CIP) may benefit from some particle irregularity to increase cold-welding without compromising powder flow and packing.
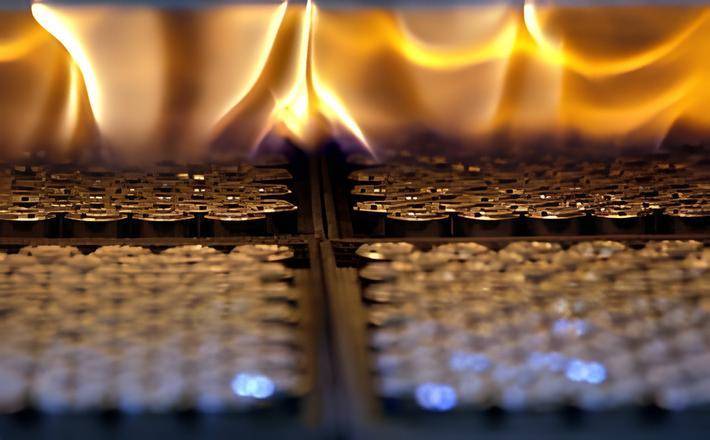
Preferred properties for HIP and CIP
HIP and CIP are two commonly used methods for sintering components. HIP produces materials with improved uniformity, reduced defects, and enhanced mechanical properties compared to CIP. CIP, on the other hand, is a cold process that is suitable for materials sensitive to high temperatures.
Role of phase composition and grain size
Phase composition and grain size are also important characteristics to control in the sintering process. These factors can affect powder hardness, melt properties, pressing efficiency, sintering behavior, and mechanical properties of the final component. It is essential to analyze and control these properties to ensure the desired outcome.
Compliance with alloy composition
The powder used in the sintering process must comply with the specified alloy composition. Whether using pure metals or alloyed powders, it is crucial to ensure that the powder's chemical composition aligns with the desired material characteristics. This compliance ensures that the final sintered component meets the desired specifications.
In conclusion, material characterization is of utmost importance in the sintering process. Understanding the effects of metal powder properties, choosing the right method (HIP or CIP), controlling phase composition and grain size, and ensuring compliance with alloy composition are all critical factors in achieving high-quality sintered components.
Conclusion
In conclusion, isostatic pressing plays a crucial role in improving additive manufacturing materials. This process offers several advantages over the traditional press and sinter method, such as equal compaction in all directions and uniform final component density. Additionally, metal powder characterization is essential in isostatic pressing to ensure the desired properties of the final sintered component. Factors like metal powder properties, phase composition, grain size, and alloy composition need to be carefully considered for successful isostatic pressing. By understanding and implementing these practices, businesses can enhance the quality and performance of their additive manufacturing materials.
If you are interested in this product you can browse our company website:https://kindle-tech.com/product-categories/isostatic-press, as an industry-leading laboratory equipment manufacturer, we are committed to providing the most advanced and high-quality laboratory equipment solutions. Whether you are engaged in scientific research, teaching or industrial production, our products will meet your needs for accurate and reliable laboratory equipment.
CONTACT US FOR A FREE CONSULTATION
KINTEK LAB SOLUTION's products and services have been recognized by customers around the world. Our staff will be happy to assist with any inquiry you might have. Contact us for a free consultation and talk to a product specialist to find the most suitable solution for your application needs!