Historical Development of Vacuum Coating Technology
Early Challenges and CVD Technology
Vacuum coating technology took its first significant steps in the 1960s with the advent of Chemical Vapor Deposition (CVD). This pioneering technique, while revolutionary at the time, was not without its challenges. One of the most significant hurdles was the requirement for high temperatures, which limited the types of substrates that could be effectively coated. The high thermal demands of CVD processes meant that only materials with high thermal stability could withstand the deposition conditions, significantly narrowing the field of potential applications.
Moreover, the early CVD technology was constrained by the limited variety of coatings it could produce. The complexity and specificity of the chemical reactions involved in CVD meant that only a handful of materials could be reliably deposited, further restricting its utility. These limitations posed significant challenges to the development and widespread adoption of vacuum coating technology, necessitating the search for alternative methods that could overcome these barriers.
In the subsequent decades, these early challenges would pave the way for the development of more versatile and efficient coating technologies, such as Physical Vapor Deposition (PVD), which emerged in the 1970s and offered a more adaptable and environmentally friendly solution.
Emergence of PVD Technology
By the 1970s, the landscape of vacuum coating technology underwent a significant transformation with the advent of Physical Vapor Deposition (PVD) technology. This new method not only addressed some of the environmental concerns associated with its predecessor, Chemical Vapor Deposition (CVD), but also introduced a myriad of versatile surface properties that were previously unattainable. The shift from CVD to PVD was marked by a reduction in operational temperatures and an expansion in the range of coatings that could be applied, thereby broadening its applications across various industries.
The environmental benefits of PVD were particularly noteworthy. Unlike CVD, which often required high temperatures and potentially hazardous chemicals, PVD operated under more controlled conditions, leading to reduced energy consumption and lower emissions. This environmental friendliness, coupled with its ability to produce coatings with superior hardness, wear resistance, and corrosion protection, quickly garnered attention from both researchers and industrialists.
The rapid development of PVD technology during this period can be attributed to its adaptability and the significant improvements it brought to the quality and durability of coatings. Industries ranging from automotive to aerospace began to adopt PVD for its ability to enhance the performance of tools and components, leading to increased efficiency and longer product lifespans. This widespread adoption further fueled advancements in PVD techniques, driving the technology forward and solidifying its place in the realm of modern industrial processes.
Current State and Challenges
Unbalanced Development
Despite the widespread adoption of vacuum coating technology for decorative purposes, the application of these coatings in industrial mold manufacturing remains fraught with challenges. The primary obstacle lies in the stringent adhesion requirements demanded by industrial molds, which necessitate a more robust and durable bond between the coating and the substrate. This heightened demand is not easily met by current coating technologies, which often prioritize aesthetic appeal over functional durability.
Moreover, the lack of comprehensive process technologies tailored specifically for industrial mold coating further exacerbates these challenges. Unlike decorative coatings, which can afford to be less rigorous in their application methods, industrial mold coatings require precise and controlled processes to ensure optimal performance and longevity. This disparity in technological development has led to an unbalanced growth within the vacuum coating industry, where advancements in decorative coatings have not been adequately mirrored in industrial applications.
To address these issues, there is a pressing need for the development of specialized technologies and methodologies that can meet the unique demands of industrial mold coating. This includes not only improving the adhesion properties of the coatings but also refining the entire process chain, from pre-treatment to post-application quality control. By focusing on these areas, the industry can bridge the gap between decorative and industrial coatings, fostering a more balanced and comprehensive development trajectory.
Technical Disparities
In the realm of vacuum coating technology, particularly in the context of PVD (Physical Vapor Deposition), domestic technical capabilities often find themselves trailing behind international standards. This disparity is not merely a matter of equipment sophistication but also encompasses a broader range of factors, including process optimization, material science advancements, and quality control methodologies.
To bridge this gap, there is a pressing need for the domestic industry to not only introduce advanced equipment but also to absorb and integrate cutting-edge technologies. This involves a multi-faceted approach, including:
- Equipment Upgrades: Investing in state-of-the-art vacuum chambers, power supplies, and gas input systems that are capable of handling complex PVD processes with precision.
- Technological Absorption: Engaging in collaborative research and development with international partners to understand and implement best practices in PVD technology.
- Process Optimization: Refining existing processes to ensure uniformity in coating quality, addressing issues such as adhesion and layer consistency.
Aspect | Domestic Status | International Standards |
---|---|---|
Equipment | Basic or outdated | Advanced and highly precise |
Process Control | Manual or semi-automated | Fully automated with AI support |
Material Science | Limited research focus | Extensive research and innovation |
Quality Control | Ad-hoc methods | Systematic and rigorous FQC |
The journey towards parity involves not just the acquisition of technology but also the development of a robust ecosystem that supports continuous innovation and improvement. This holistic approach is essential to elevate domestic capabilities and ensure that they can compete on a global scale.
Basic Concepts and Characteristics of PVD Coating
Methods and Techniques
Physical Vapor Deposition (PVD) encompasses several advanced methods, each with unique characteristics and applications. Two prominent techniques within PVD are multi-arc plating and magnetron sputtering.
Multi-arc plating involves the evaporation of target material using an electric arc, which ionizes the material and propels it toward the substrate. This method is known for its high deposition rates and ability to coat complex geometries. However, it can suffer from issues such as particle contamination and non-uniform coating thickness.
On the other hand, magnetron sputtering employs a magnetic field to enhance the ionization of target atoms, which are then accelerated toward the substrate. This technique offers better control over coating properties, including density and uniformity, making it ideal for applications requiring precise coatings. Despite these advantages, magnetron sputtering can be slower and more energy-intensive compared to multi-arc plating.
Method | Advantages | Disadvantages |
---|---|---|
Multi-Arc Plating | High deposition rates, suitable for complex geometries | Particle contamination, non-uniform coating thickness |
Magnetron Sputtering | Excellent control over coating properties, high density and uniformity | Slower process, higher energy consumption |
Understanding these methods and their respective pros and cons is crucial for selecting the most appropriate PVD technique for specific industrial applications.
Combination of Technologies
The integration of multi-arc and magnetron technologies represents a significant advancement in the field of vacuum coating. This combination is not merely a sum of its parts but a synergistic approach that maximizes the benefits of both technologies, ensuring the production of stable and high-quality coatings.
Multi-arc plating, known for its high deposition rates and ability to produce dense coatings, complements magnetron sputtering, which excels in producing uniform and conformal coatings with minimal substrate heating. By combining these methods, manufacturers can achieve a balance between deposition speed and coating uniformity, critical for applications requiring both efficiency and precision.
Moreover, the hybridization of these technologies allows for the optimization of coating properties. For instance, the incorporation of multi-arc ions into the magnetron sputtering process can enhance the adhesion and hardness of the coatings, addressing common challenges in industrial mold coating where higher adhesion and durability are paramount.
This integration also opens new avenues for material selection and process control. By leveraging the strengths of both technologies, it is possible to deposit a wider range of materials with tailored properties, from hard wear-resistant coatings to more complex multi-layer structures. The result is a more versatile and robust coating solution that meets the diverse demands of various industrial applications.
In summary, the combination of multi-arc and magnetron technologies not only enhances the quality and stability of coatings but also broadens the scope of achievable material properties and process efficiencies. This advancement is pivotal in pushing the boundaries of what vacuum coating technology can achieve, making it a cornerstone in the evolution of industrial coatings.
Modern Coating Equipment and Processes
Components and Systems
Modern coating equipment is a sophisticated assembly of essential components, each playing a crucial role in the vacuum deposition process. At the heart of this system is the vacuum chamber, a sealed environment that isolates the substrate from atmospheric conditions, ensuring a pristine surface for coating. The vacuum chamber is typically constructed from materials like stainless steel, known for their durability and resistance to corrosion.
To achieve the necessary vacuum levels, vacuum obtaining parts are employed. These include vacuum pumps, such as rotary vane pumps and turbo molecular pumps, which work in tandem to reduce the chamber's pressure to the ultra-low levels required for PVD processes. The efficiency of these pumps is critical, as it directly impacts the quality and uniformity of the coating.
Power supplies are another critical component, providing the electrical energy needed to vaporize the coating material. Modern systems often utilize intermediate-frequency power supplies or pulse technology, which offer precise control over the deposition process, resulting in higher quality coatings. These advanced power supplies help mitigate issues like arcing and non-uniform deposition, common challenges in traditional PVD setups.
Finally, the process gas input systems are integral to the operation. These systems introduce reactive gases into the vacuum chamber, enabling the formation of complex coatings with tailored properties. The precise control of gas flow rates and composition allows for the creation of coatings with specific mechanical, chemical, and optical characteristics, enhancing the versatility and applicability of the technology.
In summary, the modern coating equipment is a complex interplay of vacuum chambers, vacuum obtaining parts, power supplies, and process gas input systems, each contributing to the precision and quality of the PVD process.
Advanced Techniques
In the realm of vacuum coating technology, several advanced techniques have emerged, significantly enhancing the quality and applicability of coatings. One such technique is the utilization of non-equilibrium magnetic fields. These fields allow for more precise control over the deposition process, enabling the creation of coatings with superior uniformity and adhesion. This is particularly beneficial in industrial applications where the durability and performance of the coating are critical.
Another pivotal advancement is the introduction of intermediate-frequency power supplies. Unlike traditional power supplies, these intermediate-frequency systems offer greater stability and efficiency. They facilitate the deposition of thicker and more robust coatings without compromising the integrity of the underlying material. This innovation is particularly useful in industries requiring high-performance coatings for molds and tools.
Additionally, pulse technology has revolutionized the coating process. By delivering energy in short, controlled bursts, pulse technology minimizes thermal stress on the substrate, preventing warping and degradation. This method is especially advantageous for delicate materials or those that require intricate surface treatments. The precise energy delivery also ensures that the coating adheres more effectively, leading to longer-lasting and more reliable results.
These advanced techniques collectively contribute to the evolution of vacuum coating technology, making it more versatile and effective across various industrial applications. The integration of non-equilibrium magnetic fields, intermediate-frequency power supplies, and pulse technology not only improves the quality of coatings but also broadens their applicability, meeting the increasingly stringent demands of modern industries.
Application and Quality Control in PVD for Molds
Pre-Treatment and Coating Processes
Pre-treatment methods are crucial steps in preparing surfaces for Physical Vapor Deposition (PVD) coating. These methods include high-temperature steam cleaning, which effectively removes contaminants and ensures a clean substrate. Sandblasting is another vital technique, providing a rough surface that enhances the adhesion of the coating. The PVD coating process itself relies heavily on precise temperature control and uniform heating to achieve optimal results.
Uniform heating is essential because it ensures that the substrate is evenly heated, which in turn allows for a uniform deposition of the coating material. Temperature control is equally important, as deviations can lead to inconsistencies in the coating's thickness and quality. Advanced techniques such as intermediate-frequency power supplies and pulse technology are often employed to maintain stable and consistent heating conditions, thereby enhancing the overall quality of the PVD coating.
These pre-treatment and coating processes are integral to the success of PVD applications in industrial molds. They not only improve the durability and performance of the molds but also extend their operational life, making them indispensable in high-precision manufacturing environments.
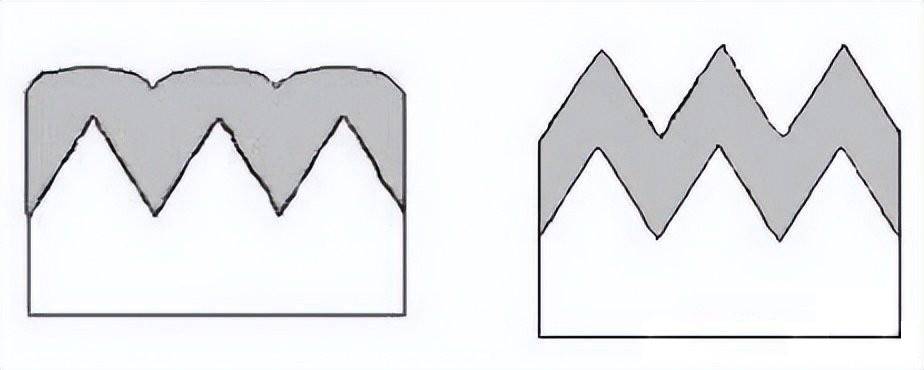
Quality Control Measures
Function Quality Control (FQC) is a critical aspect of ensuring the reliability and performance of coated molds. This process encompasses several meticulous inspections to guarantee that the coatings meet the required standards.
One of the primary methods in FQC is the appearance inspection. This involves a thorough visual examination to detect any surface imperfections such as scratches, pits, or discoloration. These defects can significantly impact the mold's functionality and lifespan, making this step indispensable.
Another key method is the layer depth inspection. This technique measures the thickness of the coating layers to ensure they adhere to the specified parameters. Various instruments, such as profilometers and scanning electron microscopes, are employed to accurately determine the depth and uniformity of the coating.
The adhesion inspection is also crucial. This process evaluates the bond strength between the coating and the mold substrate. Common methods include scratch tests, pull tests, and cross-cut tests. These tests help identify any potential delamination or peeling issues, ensuring the coating's durability and effectiveness.
By integrating these FQC methods, manufacturers can ensure that their coated molds not only meet but exceed industry standards, providing reliable and high-performance tools for various industrial applications.
CONTACT US FOR A FREE CONSULTATION
KINTEK LAB SOLUTION's products and services have been recognized by customers around the world. Our staff will be happy to assist with any inquiry you might have. Contact us for a free consultation and talk to a product specialist to find the most suitable solution for your application needs!