Introduction
Table of Contents
Isostatic pressing is an essential manufacturing process that is used to produce high-quality and complex parts. Two common methods of isostatic pressing are wet bag isostatic pressing and dry bag isostatic pressing. In this blog post, we will explore and compare these two methods to understand their differences, benefits, limitations, and suitability for different scenarios. Whether you are new to isostatic pressing or looking for an alternative method, this comparative study will help you make an informed decision. So, let's dive in and explore the world of wet bag and dry bag isostatic pressing!
Understanding Cold Isostatic Pressing
Introduction to Cold Isostatic Pressing
Cold isostatic pressing (CIP) is a technique used to form powdered materials at room temperature by applying pressure to the powder. The pressure is usually between 100-600 MPa, and the process is carried out using a liquid medium such as water, oil, or a glycol mixture. The goal of CIP is to obtain a "raw" part with sufficient strength for handling and processing, which can then be further sintered to achieve its final strength.
For metals, cold isostatic pressing can achieve a theoretical density of about 100%, while for ceramic powders, the density can reach around 95%. This technology is commonly used to produce blanks for further sintering or hot isostatic pressing processes.
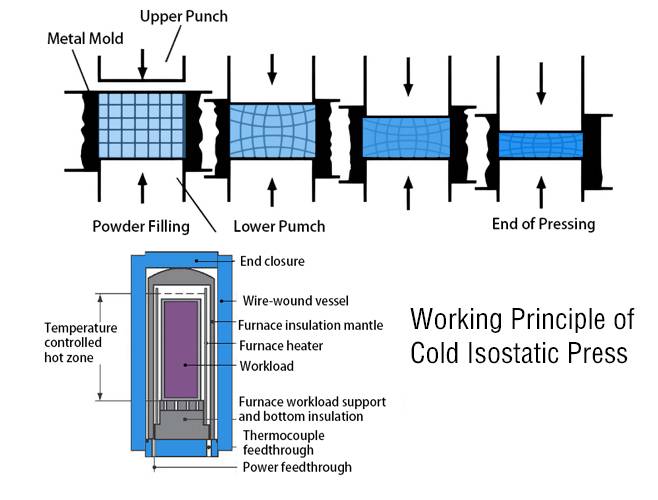
Differentiation between Wet Bag Method and Dry Bag Method
Cold isostatic pressing can be further divided into two methods: the wet bag method and the dry bag method.
Wet Bag Method
In the wet bag method, the powder material is enclosed in a flexible mold bag. This bag is then submerged into a high-pressure liquid within a pressure vessel. Isostatic pressure is applied to the outer surfaces of the mold, compressing the powder into the desired shape. The wet bag method is ideal for producing parts with complex shapes and can be used for both small and large quantity production. Additionally, it allows for the pressing of large products.
Dry Bag Method
The dry bag method, on the other hand, involves creating an integrated mold within the pressure vessel itself. The powder is added to the mold, which is then sealed. Pressure is applied, and the part is ejected once the compaction is complete. The dry bag method eliminates the need for the separate immersion step required in the wet bag method, making automation easier.
Both wet bag and dry bag methods have their advantages and are suitable for different applications. The choice between the two methods depends on the specific goals of the project and the characteristics of the materials involved.
In summary, cold isostatic pressing is a valuable technique for forming powdered materials at room temperature. It allows for the production of parts with high density and can be used for both metals and ceramics. The wet bag and dry bag methods offer different approaches to achieving the desired compaction, with the wet bag method being suitable for complex shapes and larger quantity production. Understanding the differences between these methods can help determine the most appropriate approach for your specific needs.
Wet Bag Isostatic Pressing
Process of wet bag isostatic pressing
In wet bag isostatic pressing, the powder is filled in a mold and sealed tightly outside the pressure vessel. The mold is then submerged in the pressure fluid within the vessel. Isostatic pressure is applied to the external surface of the mold, compressing the powder into a solid mass. This process is slower compared to other types of cold isostatic pressing, taking anywhere from 5 to 30 minutes. However, advancements in high-volume pumps and loading mechanisms can help speed up the process.
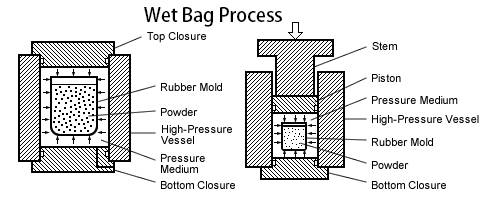
Benefits of using wet bag isostatic pressing
Wet bag isostatic pressing offers several advantages. It is highly applicable and suitable for experimental research and small batch production. It can simultaneously press multiple different shapes of parts in one high-pressure cylinder and produce large and complex parts. The production process is short and cost-effective. Wet bag processes also allow for the engineering of somewhat complex shapes into elastomeric molds, achieving high compact densities.
Ideal scenarios for using wet bag isostatic pressing
Wet bag isostatic pressing is particularly suitable for production of large parts. It is commonly used in industries where high compact densities are required and where complex shapes cannot be compacted using uniaxial presses. However, it is important to note that loading and unloading of the molds can limit automation and decrease productivity in wet bag pressing. The tooling cost and complexity of the process are also higher compared to uniaxial pressing.
In summary, wet bag isostatic pressing provides a versatile and efficient method for producing large and complex parts with high compact densities. It is especially beneficial for experimental research, small batch production, and industries requiring intricate shapes. While it may have some limitations in terms of automation and productivity, advancements in technology continue to improve the efficiency of wet bag isostatic pressing.
Dry Bag Isostatic Pressing
Process of dry bag isostatic pressing
Dry bag isostatic pressing is a production method used for small parts with axisymmetric shapes. It is commonly used in the manufacturing of high-quality ceramic bodies for spark plugs. The process involves compacting a dry or semi-dry powder in an elastomeric mold that is submerged in a pressurized liquid. The powder is shaped with the help of rigid tooling, such as a steel mandrel, combined with the flexible elastomeric mold. Typical forming pressures for ceramics range from 21-210 MPa (3000-30000 psi). One major advantage of dry bag isostatic pressing is that the rubber tooling is integrated into the apparatus, eliminating the need for separate immersion and removal steps. This leads to ease in automation and fast production rates.
Benefits of using dry bag isostatic pressing
Dry bag isostatic pressing offers several benefits in the manufacturing process. Firstly, it allows for the production of high-quality ceramic bodies, particularly for spark plugs. The integrated mold and rubber tooling make automation easier, resulting in higher production rates. Additionally, the process ensures uniform density and low entrapped stress in the compacted parts, leading to minimal distortion during firing. This reduces the need for subsequent machining, which can be difficult and expensive. Overall, dry bag isostatic pressing provides efficiency, precision, and cost-effectiveness for small parts with axisymmetric shapes.
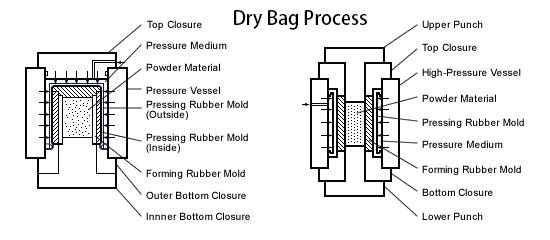
Ideal scenarios for using dry bag isostatic pressing
Dry bag isostatic pressing is an ideal production method in scenarios where small parts with axisymmetric shapes need to be manufactured. It is particularly suitable for the production of high-quality ceramic bodies for spark plugs. The integration of rubber tooling into the apparatus allows for ease in automation, making it well-suited for high-volume production. This method is efficient, precise, and cost-effective, making it a preferred choice for industries requiring small parts with axisymmetric shapes.
Limitations of dry bag isostatic pressing
While dry bag isostatic pressing offers numerous advantages, it also has certain limitations. One limitation is that there is friction on the side of the mold that does not experience compression from the pressurizing liquid. This can result in lower accuracy of pressed surfaces adjacent to the flexible bag, compared to other pressing methods like mechanical pressing or extrusion. This may necessitate subsequent machining to achieve the desired surface finish. Additionally, the dry bag process has more shape and size limitations compared to other methods, which may require green machining to develop the surface features needed for certain applications.
In conclusion, dry bag isostatic pressing is a valuable production method for small parts with axisymmetric shapes, particularly in the manufacturing of high-quality ceramic bodies for spark plugs. It offers efficiency, precision, and cost-effectiveness, making it an ideal choice for industries requiring such components. However, it's important to consider the limitations of the process, such as lower accuracy of pressed surfaces and shape and size limitations, when determining its suitability for specific applications.
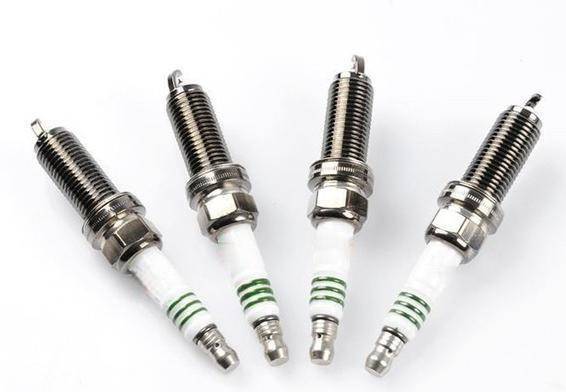
Comparison of Wet Bag and Dry Bag Isostatic Pressing
Comparing production process and cost
Wet bag isostatic pressing involves putting the powder into a forming mold and then placing it in a high-pressure cylinder for pressing after sealing. During pressing, the mold is completely immersed in liquid and in direct contact with the pressure transmission medium. This method is suitable for experimental research and small batch production. It allows for the simultaneous pressing of multiple parts with different shapes in one high-pressure cylinder, making it ideal for producing large and complex parts. The production process is short and cost-effective.
The dry bag variation of isostatic pressing involves creating a mold integrated into the pressure vessel. In this process, the powder is added to the mold, sealed, pressure is applied, and then the part is ejected. The dry bag method allows for easier automation compared to the wet bag method as the molds are integrated into the vessel. It is more suitable for production of smaller parts and offers higher production rates.
Comparing automation and operation cycle
The wet bag method requires the loading and unloading of molds, which decreases productivity and limits automation. On the other hand, the dry bag method, with its integrated molds, allows for easier automation and higher production rates. The operation cycle for wet bag isostatic pressing involves removing the mold from the pressure vessel, retrieving the part, and repeating the process. In the dry bag method, the mold is sealed, pressure is applied, and the part is ejected.
Comparing suitability for different production volumes
Wet bag isostatic pressing is particularly suitable for experimental research and small batch production. It allows for the simultaneous pressing of multiple parts with different shapes in one high-pressure cylinder, making it suitable for producing large and complex parts. The dry bag method, on the other hand, is more suitable for production of smaller parts and offers higher production rates.
Comparing limitations in product size and shape
Wet bag isostatic pressing is better suited for the production of large parts compared to the dry bag method. This is due to the ability to simultaneously press multiple parts with different shapes in one high-pressure cylinder. However, the loading and unloading of molds in the wet bag method decreases productivity and limits automation. The dry bag method, with its integrated molds, offers easier automation and higher production rates. Both types of isostatic pressing have higher tooling costs and process complexity compared to uniaxial pressing.
Isostatic pressing, whether wet bag or dry bag, is frequently chosen to achieve high compact densities and access shapes that cannot be compacted in uniaxial presses. The wet bag method allows for the engineering of somewhat complex shapes into the elastomeric molds. Wet bag processes also offer the advantage of higher densities as they involve very little friction. The dry bag method has the edge on automation and production rate.
Overall, the choice between wet bag and dry bag isostatic pressing depends on the specific requirements of the production process, such as the desired part size, shape, production volume, and automation level.
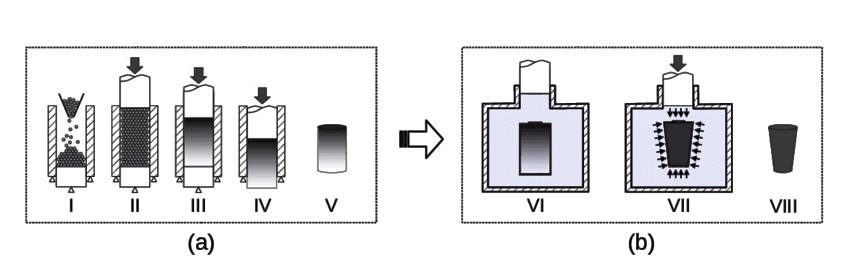
Conclusion
In conclusion, both wet bag isostatic pressing and dry bag isostatic pressing have their advantages and limitations. Wet bag isostatic pressing is ideal for situations where higher pressure is required, and it offers better uniformity and density of the final product. On the other hand, dry bag isostatic pressing is more suitable for smaller production volumes and offers faster cycle times. However, it has limitations in terms of product size and shape. Ultimately, the choice between the two methods depends on the specific requirements and constraints of the production process.
If you are interested in this product you can browse our company website:https://kindle-tech.com/product-categories/isostatic-press, we always insist on the principle of quality first. During the production process, we strictly control every step of the process, using high quality materials and advanced production technology to ensure the stability and durability of our products. to ensure that their performance meets the highest standards. We believe that only by providing customers with excellent quality can we win their trust and long-term cooperation.
CONTACT US FOR A FREE CONSULTATION
KINTEK LAB SOLUTION's products and services have been recognized by customers around the world. Our staff will be happy to assist with any inquiry you might have. Contact us for a free consultation and talk to a product specialist to find the most suitable solution for your application needs!