Deposition processes are primarily categorized into two main types: Physical Vapor Deposition (PVD) and Chemical Vapor Deposition (CVD). PVD involves the physical transfer of materials to a substrate in a vacuum environment, typically using heat or sputtering techniques. On the other hand, CVD relies on chemical reactions of gaseous precursors to form a thin film on the substrate. These two methods form the foundation of modern deposition techniques, each with its own set of advantages, applications, and variations.
Key Points Explained:
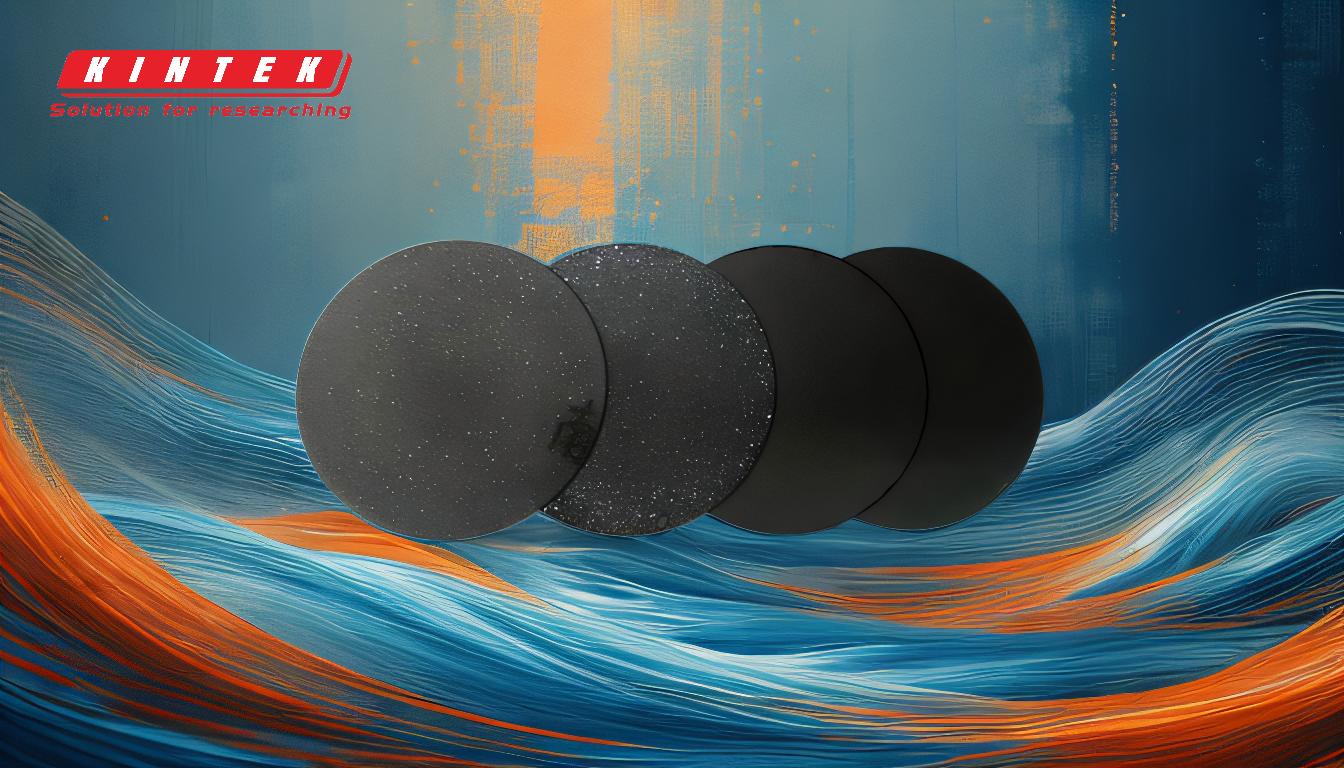
-
Physical Vapor Deposition (PVD):
- Definition: PVD is a process where materials are physically transferred from a source to a substrate in a vacuum environment.
- Mechanism: The process typically involves heating the source material until it vaporizes or using sputtering to eject atoms from the target material.
-
Key Techniques:
- Evaporation: The source material is heated to its vaporization point, and the vapor then condenses on the substrate.
- Sputtering: High-energy particles bombard the target material, causing atoms to be ejected and deposited onto the substrate.
- Applications: PVD is widely used in the production of thin films for semiconductors, optical coatings, and wear-resistant coatings.
-
Chemical Vapor Deposition (CVD):
- Definition: CVD is a process where a thin film is formed on a substrate through the chemical reaction of gaseous precursors.
- Mechanism: The gaseous precursors are introduced into a reaction chamber, where they react or decompose to form a solid material on the substrate.
-
Key Techniques:
- Thermal CVD: The substrate is heated to high temperatures to facilitate the chemical reaction.
- Plasma-Enhanced CVD (PECVD): A plasma is used to enhance the chemical reaction at lower temperatures.
- Atomic Layer Deposition (ALD): A highly controlled process where thin films are deposited one atomic layer at a time.
- Applications: CVD is used in the production of semiconductors, coatings for tools, and the fabrication of nanostructures.
-
Comparison Between PVD and CVD:
- Environment: PVD requires a vacuum environment, while CVD can be performed at atmospheric pressure or in a vacuum.
- Temperature: PVD generally operates at lower temperatures compared to CVD, which often requires high temperatures for the chemical reactions to occur.
- Material Compatibility: PVD is suitable for a wide range of materials, including metals and ceramics, while CVD is particularly effective for depositing complex compounds and alloys.
- Film Quality: CVD typically produces films with better step coverage and uniformity, while PVD films may have higher density and fewer impurities.
-
Other Deposition Techniques:
- Electrochemical Deposition: This involves the use of an electric current to deposit a material onto a conductive substrate. It is commonly used in electroplating.
- Spray Pyrolysis: A solution containing the desired material is sprayed onto a heated substrate, where it decomposes to form a thin film.
- Molecular Beam Epitaxy (MBE): A highly controlled process used to grow high-quality crystalline films, typically for semiconductor applications.
-
Choosing the Right Deposition Method:
- Substrate Material: The choice of deposition method often depends on the substrate material and the desired properties of the film.
- Application Requirements: Factors such as film thickness, uniformity, and purity play a crucial role in selecting the appropriate deposition technique.
- Cost and Scalability: The cost of the equipment and the scalability of the process are also important considerations, especially for large-scale production.
In summary, deposition techniques are diverse and can be broadly categorized into PVD and CVD, each with its own set of advantages and applications. The choice of deposition method depends on various factors, including the material properties, application requirements, and production considerations. Understanding these techniques and their differences is crucial for selecting the right method for specific applications.
Summary Table:
Aspect | PVD | CVD |
---|---|---|
Environment | Requires a vacuum environment | Can be performed at atmospheric pressure or in a vacuum |
Temperature | Generally operates at lower temperatures | Often requires high temperatures for chemical reactions |
Material Compatibility | Suitable for metals and ceramics | Effective for complex compounds and alloys |
Film Quality | Higher density, fewer impurities | Better step coverage and uniformity |
Applications | Semiconductors, optical coatings, wear-resistant coatings | Semiconductors, tool coatings, nanostructures |
Need help choosing the right deposition method for your application? Contact our experts today!