Yes, graphene can be made artificially through various methods, which are broadly categorized into "top-down" and "bottom-up" approaches. The top-down methods involve breaking down graphite into graphene layers, while the bottom-up methods involve building graphene from smaller carbon-containing molecules. The most common techniques include mechanical exfoliation, chemical vapor deposition (CVD), reduction of graphene oxide, and liquid-phase exfoliation. Each method has its own advantages and limitations, with CVD being particularly promising for producing large-area, high-quality graphene.
Key Points Explained:
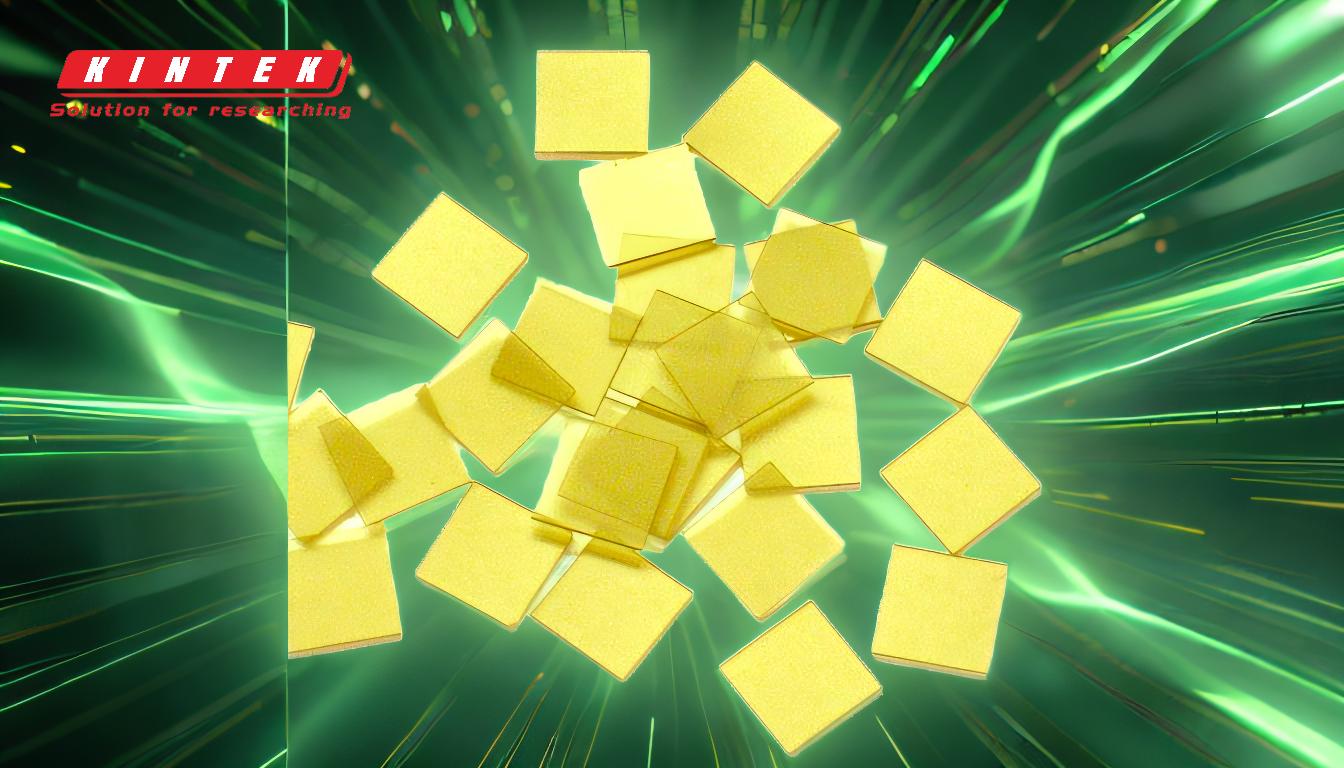
-
Top-Down Methods:
- These methods involve deriving graphene from graphite or other carbon-rich materials.
- Mechanical Exfoliation: This is the simplest method, where graphene is peeled off from graphite using adhesive tape. It is primarily used for fundamental research due to its simplicity and ability to produce high-quality graphene. However, it is not scalable for mass production.
- Liquid-Phase Exfoliation: In this method, graphite is dispersed in a liquid medium and subjected to ultrasonic treatment to separate the layers. This method is suitable for mass production but often results in graphene with lower electrical quality due to defects and impurities.
- Reduction of Graphene Oxide (GO): Graphene oxide is produced by oxidizing graphite, and then it is chemically reduced to produce graphene. This method is cost-effective and scalable but often results in graphene with structural defects and reduced electrical conductivity.
-
Bottom-Up Methods:
- These methods involve building graphene from smaller carbon-containing molecules.
- Chemical Vapor Deposition (CVD): This is the most promising method for producing large-area, high-quality graphene. In CVD, a carbon-containing gas (such as methane) is decomposed on a metal substrate (like copper or nickel) at high temperatures, forming a graphene layer. CVD is scalable and can produce graphene with excellent electrical properties, making it suitable for industrial applications.
- Epitaxial Growth: This method involves growing graphene on a silicon carbide (SiC) substrate by sublimating silicon atoms at high temperatures. The remaining carbon atoms form a graphene layer. This method produces high-quality graphene but is expensive and not suitable for large-scale production.
- Arc Discharging: This method involves creating an electric arc between two graphite electrodes in an inert gas atmosphere. The high temperature causes carbon atoms to vaporize and then condense into graphene. This method is less common and typically produces graphene with lower quality compared to CVD.
-
Advantages and Disadvantages of Each Method:
-
Mechanical Exfoliation:
- Advantages: Produces high-quality graphene, simple and inexpensive.
- Disadvantages: Not scalable, labor-intensive.
-
Liquid-Phase Exfoliation:
- Advantages: Scalable, relatively low cost.
- Disadvantages: Lower quality graphene, potential for defects and impurities.
-
Reduction of Graphene Oxide:
- Advantages: Scalable, cost-effective.
- Disadvantages: Structural defects, reduced electrical conductivity.
-
Chemical Vapor Deposition (CVD):
- Advantages: Scalable, produces high-quality graphene, suitable for industrial applications.
- Disadvantages: Requires high temperatures, expensive equipment.
-
Epitaxial Growth:
- Advantages: Produces high-quality graphene.
- Disadvantages: Expensive, not suitable for large-scale production.
-
Arc Discharging:
- Advantages: Simple setup.
- Disadvantages: Lower quality graphene, less control over the process.
-
Mechanical Exfoliation:
-
Applications and Suitability:
- Research and Fundamental Studies: Mechanical exfoliation is ideal due to its simplicity and ability to produce high-quality graphene.
- Mass Production: Liquid-phase exfoliation and reduction of graphene oxide are more suitable due to their scalability, despite the lower quality of the resulting graphene.
- Industrial Applications: CVD is the most promising method for producing large-area, high-quality graphene, making it suitable for applications in electronics, sensors, and energy storage.
In conclusion, graphene can indeed be made artificially through various methods, each with its own set of advantages and limitations. The choice of method depends on the intended application, with CVD being the most promising for industrial-scale production of high-quality graphene.
Summary Table:
Method | Type | Advantages | Disadvantages |
---|---|---|---|
Mechanical Exfoliation | Top-Down | High-quality graphene, simple, inexpensive | Not scalable, labor-intensive |
Liquid-Phase Exfoliation | Top-Down | Scalable, relatively low cost | Lower quality graphene, defects, and impurities |
Reduction of Graphene Oxide | Top-Down | Scalable, cost-effective | Structural defects, reduced electrical conductivity |
Chemical Vapor Deposition (CVD) | Bottom-Up | Scalable, high-quality graphene, suitable for industrial applications | Requires high temperatures, expensive equipment |
Epitaxial Growth | Bottom-Up | Produces high-quality graphene | Expensive, not suitable for large-scale production |
Arc Discharging | Bottom-Up | Simple setup | Lower quality graphene, less control over the process |
Want to learn more about graphene production methods? Contact our experts today for tailored solutions!