PVD (Physical Vapor Deposition) coatings are highly durable, wear-resistant, and corrosion-resistant, making them suitable for demanding applications in industries like automotive, aerospace, and medical. While PVD coatings are known for their exceptional adhesion, hardness, and low friction properties, recoating them is possible under certain conditions. Recoating involves preparing the existing coating surface to ensure proper adhesion of the new layer. However, the process requires careful consideration of factors such as the condition of the existing coating, substrate material, and application requirements. Recoating can restore or enhance the performance of PVD-coated components, but it must be done with precision to maintain the coating's integrity and functionality.
Key Points Explained:
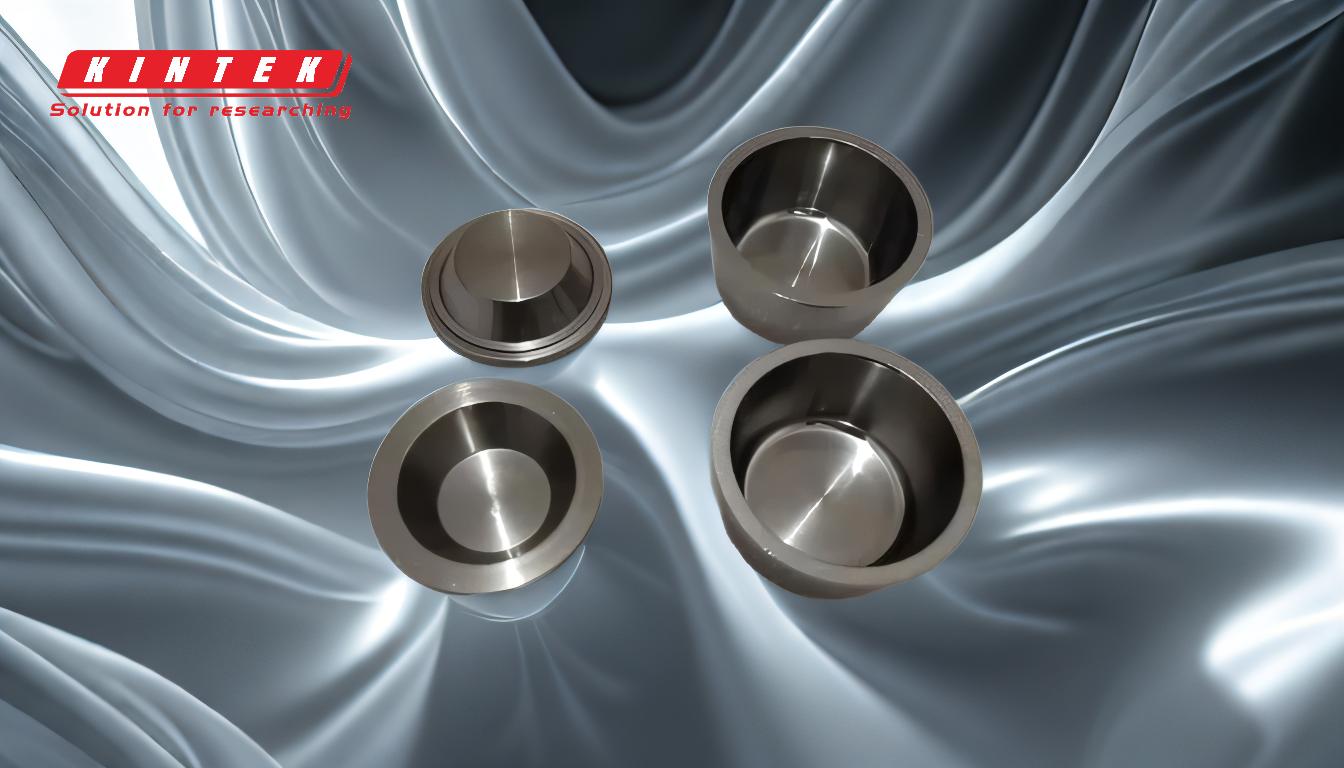
-
PVD Coating Properties and Durability:
- PVD coatings are known for their high hardness, wear resistance, and corrosion resistance. They are typically thin (0.5 to 5 microns) and adhere strongly to the substrate.
- These properties make PVD coatings highly durable, often eliminating the need for additional protective layers.
- Due to their robust adhesion and resistance to wear, PVD coatings are challenging to remove, which is a consideration when planning recoating.
-
Recoating Feasibility:
- Recoating PVD-coated surfaces is possible but requires proper surface preparation to ensure adhesion of the new layer.
- The existing coating must be evaluated for wear, damage, or contamination. If the original coating is intact and clean, recoating can be performed without removing it.
- In cases where the existing coating is damaged or contaminated, it may need to be stripped or polished before applying a new layer.
-
Surface Preparation for Recoating:
- Proper cleaning is critical to remove any contaminants, oils, or oxides that could interfere with adhesion.
- Techniques such as plasma cleaning or chemical etching may be used to prepare the surface.
- The substrate material must also be considered, as different materials may require specific preparation methods.
-
Recoating Process:
- The recoating process involves reapplying a PVD layer using the same or similar deposition techniques as the original coating.
- The new coating must be compatible with the existing layer and substrate to ensure optimal performance.
- Recoating can restore or enhance properties such as wear resistance, corrosion resistance, and aesthetic appearance.
-
Challenges and Considerations:
- PVD coatings have poor performance on the back and sides of tools due to low air pressure during deposition. This limitation must be addressed during recoating.
- The thickness of the new coating must be carefully controlled to avoid compromising the component's dimensions or functionality.
- Recoating may not always be cost-effective, especially for heavily damaged or low-value components.
-
Applications of Recoating:
- Recoating is particularly useful in industries where components are subject to extreme wear or corrosion, such as cutting tools, medical implants, and aerospace parts.
- It can extend the lifespan of high-value components, reducing the need for replacement and lowering overall costs.
In summary, PVD coatings can be recoated, but the process requires careful evaluation of the existing coating, thorough surface preparation, and precise application of the new layer. Recoating is a viable option for restoring or enhancing the performance of PVD-coated components, particularly in demanding industrial applications.
Summary Table:
Key Aspect | Details |
---|---|
PVD Coating Properties | High hardness, wear resistance, corrosion resistance, and strong adhesion. |
Recoating Feasibility | Possible with proper surface preparation and evaluation of existing coating. |
Surface Preparation | Cleaning, plasma cleaning, or chemical etching for optimal adhesion. |
Recoating Process | Reapply PVD layer using compatible techniques and materials. |
Challenges | Thickness control, cost-effectiveness, and addressing deposition limits. |
Applications | Cutting tools, medical implants, aerospace parts, and high-value components. |
Extend the lifespan of your PVD-coated components—contact our experts today to learn more about recoating solutions!