Soldering and brazing are both techniques used to join metals, but they differ significantly in terms of temperature, filler materials, and application strength. While soldering is performed at lower temperatures (below 840°F) and is suitable for delicate or low-stress applications, brazing occurs at higher temperatures (above 840°F) and creates stronger joints, often as robust as the base metals themselves. Solder is not typically used for brazing because it lacks the strength and high-temperature resistance required for brazed joints. Brazing is preferred in industries like automotive, HVAC, and cookware due to its durability and ability to withstand stress and heat.
Key Points Explained:
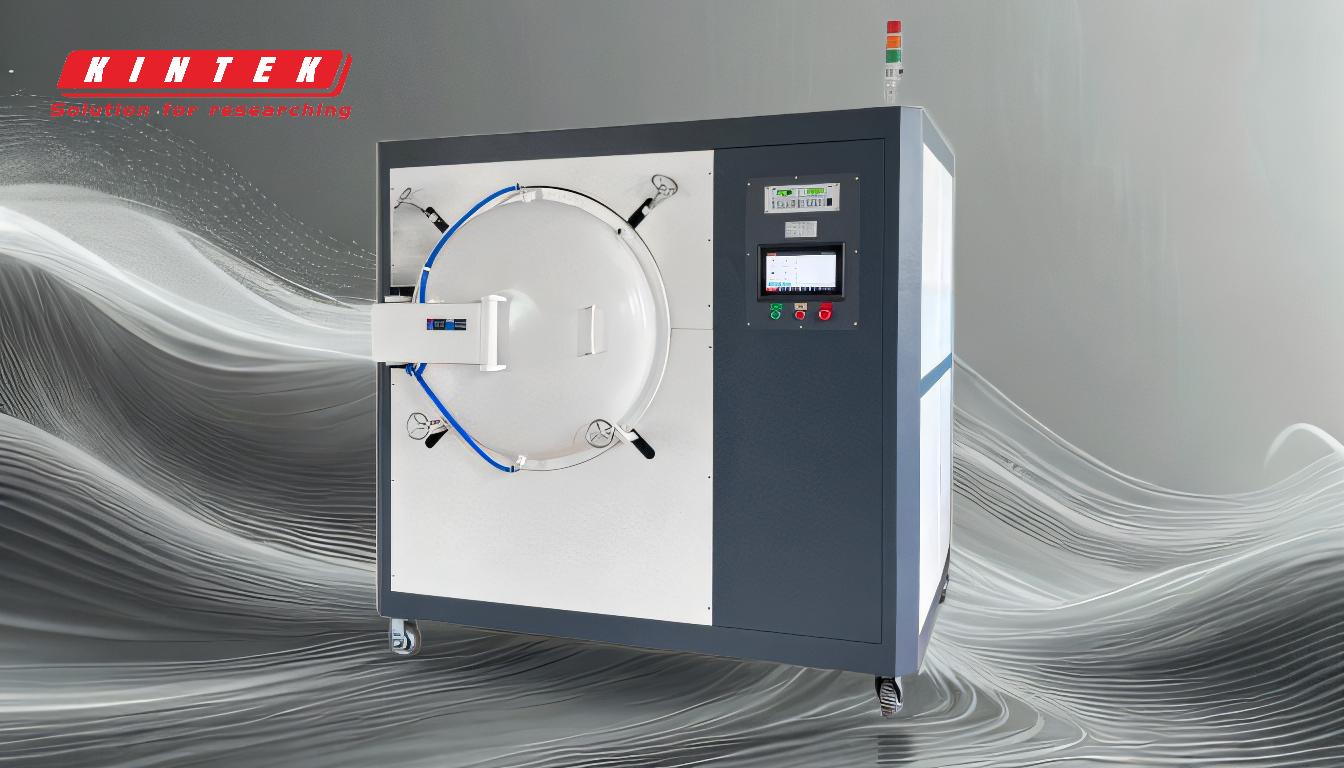
-
Difference Between Soldering and Brazing:
- Temperature: Soldering is performed at temperatures below 840°F, while brazing requires temperatures above 840°F. This difference is critical because it determines the strength and durability of the joint.
- Filler Material: Soldering uses softer filler metals like tin-lead or silver alloys, which melt at lower temperatures. Brazing uses harder filler metals like copper, silver, or aluminum alloys, which can withstand higher temperatures and provide stronger bonds.
- Strength: Brazed joints are typically as strong as the base metals, making them suitable for high-stress applications. Soldered joints, while effective for electrical connections or low-stress applications, are not as robust.
-
Why Solder is Not Suitable for Brazing:
- Low Melting Point: Solder melts at temperatures below 840°F, which is insufficient for brazing. Brazing requires higher temperatures to ensure proper bonding and strength.
- Inadequate Strength: Solder lacks the mechanical strength needed for brazed joints. Brazing filler metals are designed to create durable, high-strength bonds that can withstand stress and heat.
- Application Limitations: Solder is better suited for applications like electronics or plumbing, where high strength is not a primary requirement. Brazing is used in industries like automotive and HVAC, where joints must endure significant stress and temperature fluctuations.
-
Applications of Brazing vs. Soldering:
- Brazing: Commonly used in industries requiring strong, durable joints, such as automotive manufacturing, HVAC systems, and cookware production. It is ideal for joining dissimilar metals and creating leak-proof seals.
- Soldering: Primarily used in electronics, plumbing, and jewelry making. It is ideal for delicate work where high strength is not necessary, and low temperatures are preferred to avoid damaging sensitive components.
-
Material Compatibility:
- Brazing filler metals are designed to bond with a wide range of base metals, including steel, copper, and aluminum. Solder, on the other hand, is limited in its compatibility and is typically used with softer metals like copper or brass.
-
Process Requirements:
- Brazing: Requires precise temperature control, often using a torch or furnace, and may involve flux to prevent oxidation and ensure proper bonding.
- Soldering: Can be done with simpler tools like a soldering iron and typically uses flux to clean the surfaces and improve adhesion.
In summary, while soldering and brazing share some similarities, they are distinct processes with different applications and requirements. Solder is not suitable for brazing due to its lower melting point and inadequate strength for high-stress applications. Brazing is the preferred method for creating strong, durable joints in demanding industrial settings.
Summary Table:
Aspect | Soldering | Brazing |
---|---|---|
Temperature | Below 840°F | Above 840°F |
Filler Material | Soft metals (e.g., tin-lead, silver) | Hard metals (e.g., copper, aluminum) |
Joint Strength | Suitable for low-stress applications | As strong as base metals |
Applications | Electronics, plumbing, jewelry | Automotive, HVAC, cookware |
Material Compatibility | Limited to softer metals (e.g., copper, brass) | Compatible with steel, copper, aluminum |
Need expert advice on joining metals? Contact us today to find the best solution for your application!