Brazing stainless steel is a precise process that requires careful preparation and the right tools. MAPP gas, a mixture of methylacetylene and propadiene, is often used for brazing due to its high flame temperature, which can reach up to 3,730°F (2,050°C). This makes it suitable for brazing stainless steel, provided that the process is carried out correctly. The key to successful brazing with MAPP gas involves thorough cleaning of the stainless steel surfaces, using the appropriate flux, and ensuring that the brazing is done immediately after cleaning to prevent contamination. The process also requires careful control of the flame to avoid overheating, which can lead to oxidation and weaken the joint.
Key Points Explained:
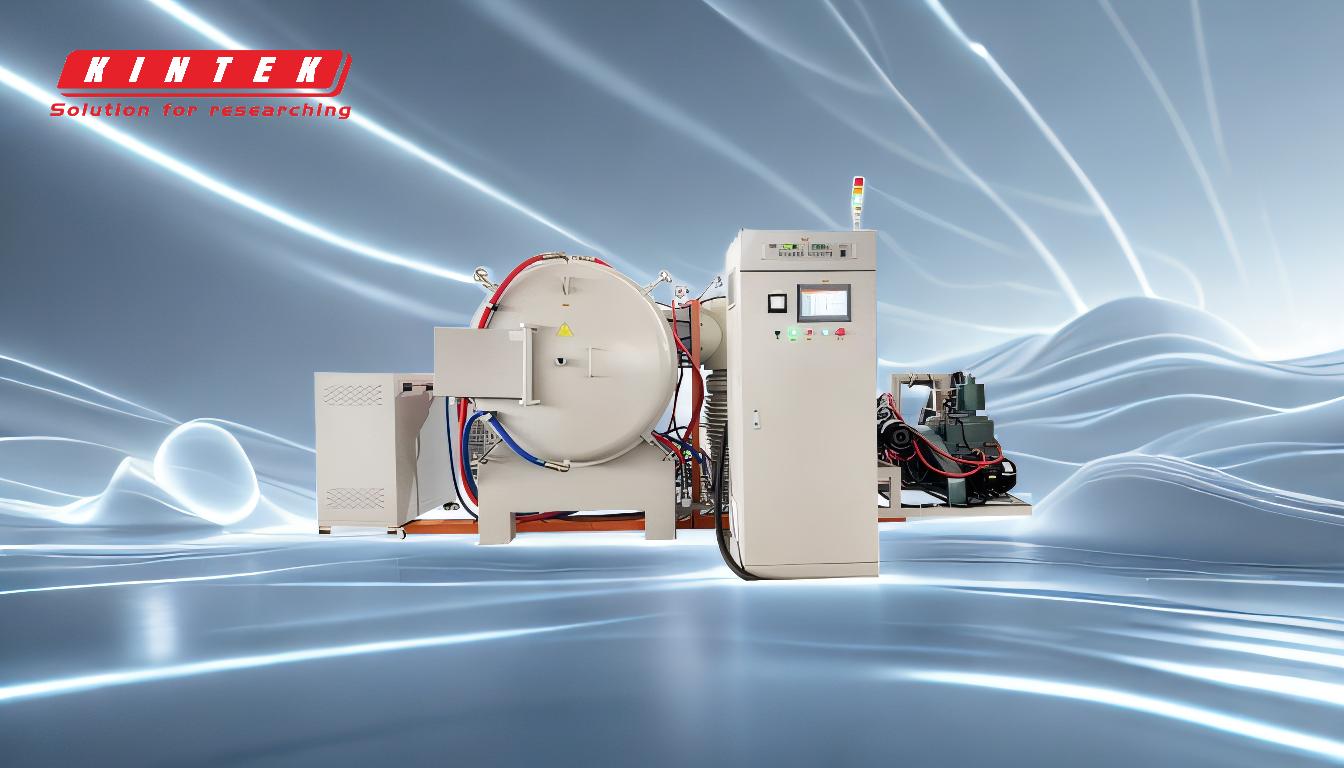
-
Understanding MAPP Gas and Its Suitability for Brazing Stainless Steel:
- MAPP gas is a fuel gas that burns hotter than propane, making it suitable for brazing stainless steel. Its high flame temperature allows for efficient heating of the metal, which is necessary for the brazing process.
- The flame temperature of MAPP gas is sufficient to melt most brazing alloys, which typically have melting points between 1,100°F and 1,500°F (593°C to 816°C).
-
Importance of Cleaning Before Brazing:
- Stainless steel surfaces must be thoroughly cleaned before brazing to remove any grease, oil, or other contaminants. This is crucial because any residue can prevent the brazing alloy from properly bonding with the stainless steel.
- Cleaning can be done using solvents, abrasives, or specialized cleaning agents designed for metal surfaces. After cleaning, the surfaces should be dried and handled carefully to avoid recontamination.
-
Immediate Brazing After Cleaning:
- Once the stainless steel is cleaned, brazing should be carried out as soon as possible. Delaying the process can lead to the formation of oxides or other contaminants on the surface, which can interfere with the brazing process.
- This step ensures that the surfaces remain clean and ready for the brazing alloy to flow and form a strong bond.
-
Use of Flux in Brazing Stainless Steel:
- Flux is essential in brazing stainless steel as it prevents oxidation and helps the brazing alloy flow evenly over the joint. The flux should be applied to the cleaned surfaces before heating.
- The type of flux used should be compatible with stainless steel and the specific brazing alloy being used. Some fluxes are designed to work at the high temperatures achieved with MAPP gas.
-
Controlling the Flame During Brazing:
- When using MAPP gas, it is important to control the flame to avoid overheating the stainless steel. Overheating can lead to oxidation, which weakens the joint and can cause discoloration.
- The flame should be adjusted to a neutral or slightly reducing flame, which provides the right balance of heat and protection against oxidation.
-
Post-Brazing Cleaning:
- After brazing, any residual flux should be removed to prevent corrosion. This can be done by washing the brazed joint with water or using a specialized cleaning solution.
- Proper post-brazing cleaning ensures the longevity and integrity of the brazed joint.
In summary, brazing stainless steel with MAPP gas is feasible and effective when the process is carried out with attention to detail. Proper cleaning, immediate brazing, the use of appropriate flux, and careful flame control are all critical steps to ensure a strong and durable brazed joint.
Summary Table:
Step | Key Details |
---|---|
MAPP Gas Suitability | High flame temperature (up to 3,730°F) ideal for brazing stainless steel. |
Cleaning Before Brazing | Remove grease, oil, and contaminants using solvents or abrasives. |
Immediate Brazing | Perform brazing right after cleaning to prevent contamination. |
Flux Application | Use compatible flux to prevent oxidation and ensure even alloy flow. |
Flame Control | Adjust to neutral or slightly reducing flame to avoid overheating. |
Post-Brazing Cleaning | Remove residual flux to prevent corrosion and ensure joint longevity. |
Need expert advice on brazing stainless steel? Contact us today for tailored solutions!