Yes, vacuum casting of metal is a well-established process used in various industries, particularly for creating high-quality, intricate metal parts with minimal defects. The process involves melting metal in a vacuum environment to prevent oxidation and contamination, followed by pouring the molten metal into a mold to solidify. This method is especially useful for casting metals that are highly reactive or require high purity, such as titanium, aluminum, and certain alloys. Below is a detailed explanation of the key aspects of vacuum casting metal.
Key Points Explained:
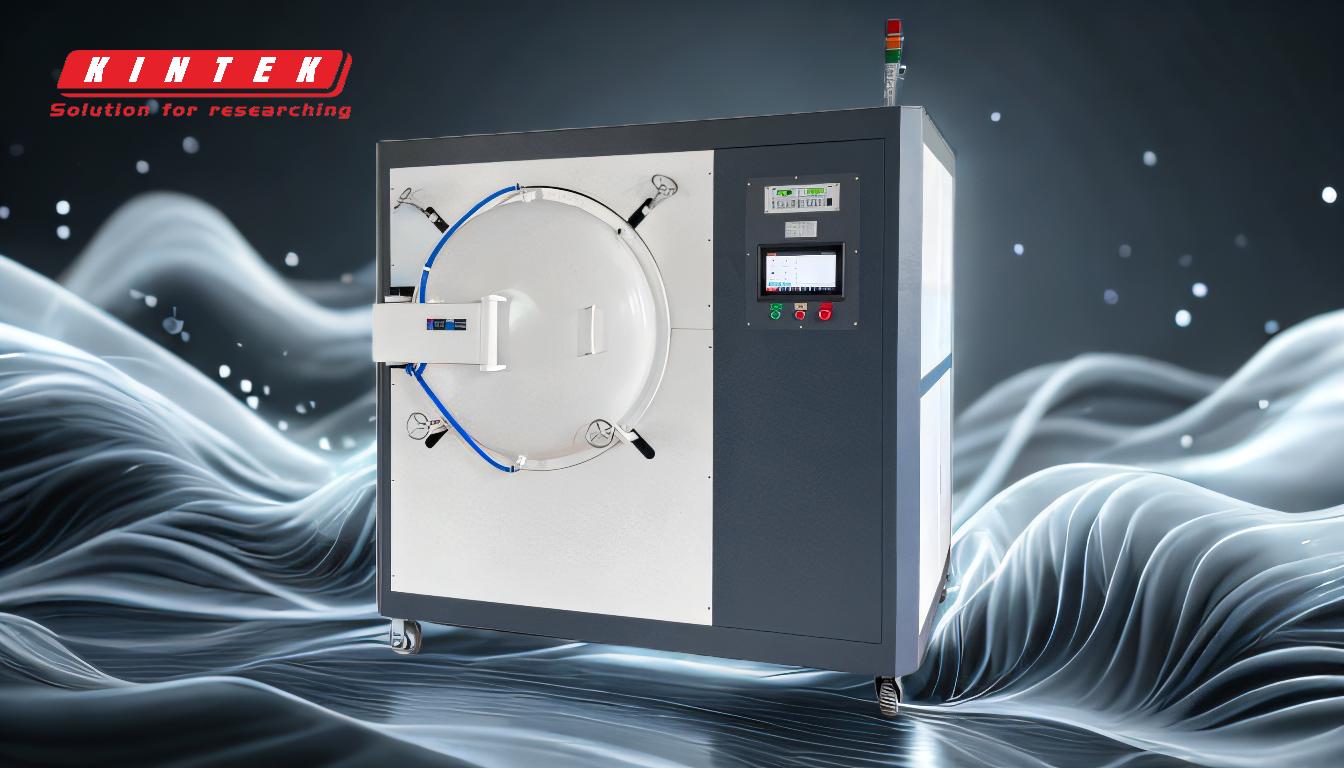
-
What is Vacuum Casting?
- Vacuum casting is a manufacturing process where metal is melted and poured into a mold under a vacuum environment. This technique is used to produce high-quality metal parts with minimal porosity and impurities.
- The vacuum environment prevents oxidation and contamination, which are common issues in traditional casting methods.
-
Advantages of Vacuum Casting:
- High Purity: The vacuum environment ensures that the metal remains free from oxidation and contamination, resulting in high-purity castings.
- Improved Mechanical Properties: Vacuum casting reduces porosity and gas entrapment, leading to better mechanical properties such as strength and durability.
- Complex Geometries: This method allows for the casting of complex and intricate shapes that would be difficult or impossible to achieve with traditional casting methods.
- Reduced Defects: The absence of air and other gases minimizes the risk of defects such as voids, cracks, and inclusions.
-
Materials Suitable for Vacuum Casting:
- Reactive Metals: Metals like titanium, aluminum, and magnesium are highly reactive and prone to oxidation. Vacuum casting is ideal for these materials.
- High-Performance Alloys: Alloys used in aerospace, medical, and other high-tech industries often require vacuum casting to achieve the necessary properties.
- Precious Metals: Gold, silver, and platinum can also be vacuum cast to produce high-quality jewelry and other items.
-
The Vacuum Casting Process:
- Melting: The metal is heated to its melting point in a vacuum chamber. This is often done using induction heating or arc melting.
- Mold Preparation: A mold is prepared, typically made of ceramic or graphite, which can withstand the high temperatures and vacuum conditions.
- Pouring: Once the metal is molten, it is poured into the mold under vacuum conditions to prevent any air or gas from being trapped.
- Solidification: The metal is allowed to cool and solidify in the mold. The vacuum environment ensures that the cooling process is controlled and uniform.
- Removal and Finishing: After solidification, the casting is removed from the mold and undergoes any necessary finishing processes, such as machining or polishing.
-
Applications of Vacuum Casting:
- Aerospace: Vacuum casting is used to produce critical components for aircraft and spacecraft, where high strength and reliability are essential.
- Medical: The process is used to create implants and surgical instruments that require high precision and biocompatibility.
- Jewelry: High-quality jewelry, especially those made from precious metals, often undergoes vacuum casting to achieve fine details and a flawless finish.
- Automotive: Vacuum casting is used for producing high-performance parts for engines and other critical systems in the automotive industry.
-
Comparison with Other Casting Methods:
- Traditional Casting: Traditional casting methods, such as sand casting or die casting, are more prone to oxidation and contamination. Vacuum casting offers superior quality and purity.
- Investment Casting: While investment casting can produce detailed parts, vacuum casting provides better control over the environment, reducing defects and improving material properties.
-
Equipment Used in Vacuum Casting:
- Vacuum Furnace: A specialized furnace that can maintain a vacuum environment while melting and pouring the metal.
- Molds: Typically made of ceramic or graphite, designed to withstand high temperatures and vacuum conditions.
- PECVD Machine: Although primarily used for depositing thin films, a PECVD machine can be part of the process in certain advanced applications where surface coatings are required after casting.
In conclusion, vacuum casting is a highly effective method for producing high-quality metal parts with minimal defects. It is particularly useful for reactive metals, high-performance alloys, and applications requiring precise and intricate details. The process offers numerous advantages over traditional casting methods, making it a preferred choice in industries where material purity and performance are critical.
Summary Table:
Aspect | Details |
---|---|
What is Vacuum Casting? | A process where metal is melted and poured into a mold under vacuum to prevent oxidation and contamination. |
Advantages | High purity, improved mechanical properties, complex geometries, reduced defects. |
Suitable Materials | Reactive metals (titanium, aluminum), high-performance alloys, precious metals. |
Process Steps | Melting, mold preparation, pouring, solidification, removal, and finishing. |
Applications | Aerospace, medical, jewelry, automotive. |
Comparison | Superior to traditional casting methods in quality and purity. |
Interested in vacuum casting for your next project? Contact us today to learn more!