Annealing is a heat treatment process primarily used to alter the microstructure of materials, improving their mechanical and electrical properties, such as reducing hardness and increasing ductility. While its primary purpose is not to change the size of a material, annealing can indirectly affect dimensions due to the relief of internal stresses and changes in the material's microstructure. These changes may lead to slight dimensional adjustments, but the effect is typically minimal and depends on factors like material type, annealing temperature, and cooling rate. In most cases, annealing is not used to intentionally alter size but rather to improve material properties and workability.
Key Points Explained:
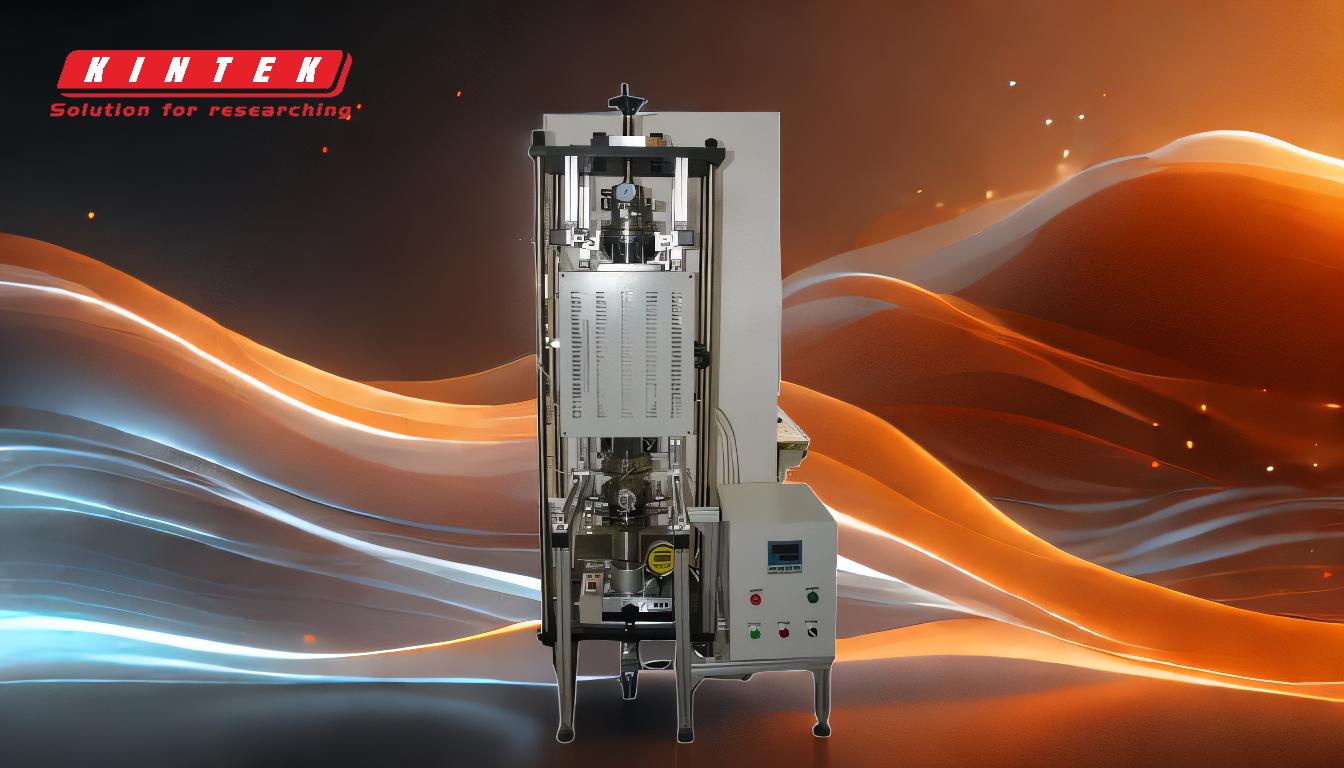
-
Purpose of Annealing:
- Annealing is primarily used to modify the microstructure of a material, improving properties like ductility, hardness, and electrical conductivity.
- It relieves internal stresses caused by processes like machining, grinding, or cold working, which can lead to material failure or distortion.
-
Effect on Material Size:
- Annealing does not directly aim to change the size of a material. However, the relief of internal stresses and microstructural changes can result in slight dimensional adjustments.
- These changes are typically minimal and depend on factors such as the material type, annealing temperature, and cooling rate.
-
Factors Influencing Dimensional Changes:
- Material Type: Different materials (e.g., steel, aluminum, copper) respond differently to annealing due to variations in their crystal structures and thermal properties.
- Annealing Temperature: Higher temperatures can cause more significant microstructural changes, potentially leading to slight dimensional shifts.
- Cooling Rate: Controlled cooling is essential to prevent warping or excessive dimensional changes.
-
Practical Implications:
- In most industrial applications, annealing is not used to intentionally alter the size of a material. Instead, it is employed to improve workability, machinability, and mechanical properties.
- For precision components, any dimensional changes due to annealing are carefully managed through controlled processes to ensure the final product meets specifications.
-
Comparison with Other Processes:
- Unlike processes like forging or rolling, which intentionally change the shape and size of materials, annealing focuses on improving material properties without significant dimensional alterations.
- However, annealing can be a preparatory step for further processing, such as cold working, where dimensional changes are more pronounced.
-
Examples of Materials:
- Steel: Annealing reduces hardness and increases ductility, making it easier to machine or form. Any dimensional changes are usually negligible.
- Aluminum, Brass, and Copper: These materials also benefit from annealing, with similar effects on ductility and workability. Dimensional changes are typically minor.
In summary, while annealing does not directly aim to change the size of a material, it can indirectly cause slight dimensional adjustments due to the relief of internal stresses and microstructural changes. These effects are generally minimal and depend on the material and annealing conditions. The primary goal of annealing remains the improvement of material properties rather than dimensional alteration.
Summary Table:
Aspect | Details |
---|---|
Primary Purpose | Improves mechanical and electrical properties (e.g., ductility, hardness). |
Effect on Size | Indirectly causes slight dimensional adjustments due to stress relief. |
Key Factors | Material type, annealing temperature, cooling rate. |
Practical Use | Enhances workability and machinability, not intentional size alteration. |
Examples of Materials | Steel, aluminum, brass, copper (minimal dimensional changes). |
Curious about how annealing can optimize your materials? Contact our experts today for tailored advice!